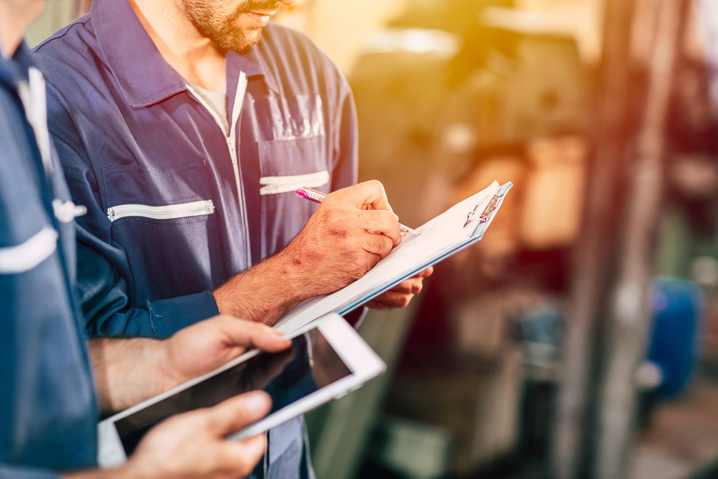
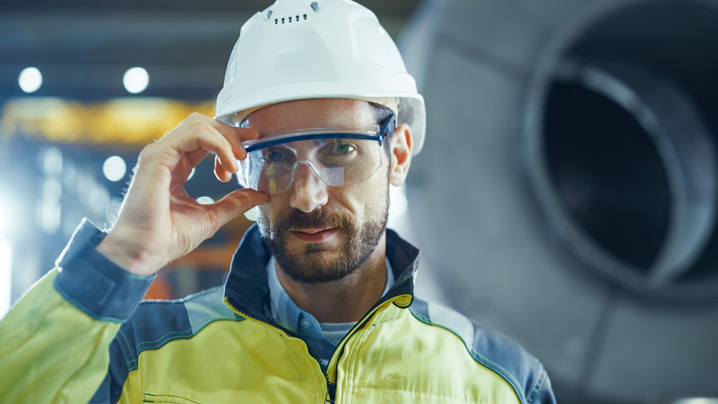
Combustible Dust Services – Testing, Mitigation, and Industry Standards for Ongoing Safety
Combustible dust is prevalent and can become a serious hazard in many industries like manufacturing, food processing, and woodworking. If not managed properly, combustible dust can lead to fires, explosions, and other catastrophic events that can harm people and damage property.
What is Combustible Dust?
Combustible dust refers to fine particles that can ignite and burn when suspended in air under certain conditions. These particles are typically generated during industrial processes such as grinding, pulverizing, crushing, or handling of materials like coal, wood, metals, plastics, chemicals, and agricultural products.
When combustible dust is dispersed in the air, it can form a flammable mixture that, if ignited, can result in a fire or explosion. The severity of such incidents depends on various factors, including the concentration of the dust cloud, the presence of an ignition source, and the confinement of the space.
In recent years, there has been a growing awareness of the risks associated with combustible dust, and as a result, there has been a corresponding increase in demand for combustible dust services. These services can include everything from dust testing and analysis to dust control and mitigation.
Start with a Dust Hazard Analysis
Dust Hazard Analysis (DHA) is a systematic process used to identify and evaluate the potential hazards associated with combustible dust in a facility. It involves analyzing various aspects of the dust-handling processes and systems to determine the risk of dust-related fires and explosions. The goal of a DHA is to identify potential ignition sources, assess the likelihood of a dust explosion, and recommend appropriate control measures to mitigate the hazards. By conducting a thorough dust hazard analysis and implementing appropriate control measures, organizations can effectively reduce the risks associated with combustible dust and create a safer working environment for employees.
DHA is performed by a team of experts, including process safety engineers, industrial hygienists, and safety professionals who have knowledge and experience in dust-related hazards. It is important to conduct DHAs periodically, especially when changes are made to the processes, equipment, or materials used in the facility.
The DHA process typically involves the following steps:
- Dust Inventory: Conduct a comprehensive assessment to identify all areas and processes where dust is generated, handled, or stored. This includes examining equipment, ventilation systems, storage facilities, and any other areas where dust accumulates.
- Dust Properties: Determine the physical and chemical characteristics of the dust, such as particle size, moisture content, and combustibility. This information helps in understanding the potential for dust explosion and selecting appropriate control measures.
- Hazard Identification: Identify potential ignition sources, such as sparks, open flames, hot surfaces, electrical equipment, or static electricity, that may come into contact with the combustible dust. Assess the likelihood of these ignition sources causing a fire or explosion.
- Risk Assessment: Evaluate the risk of a dust-related incident by considering factors such as dust concentration, containment, ventilation, and the presence of ignition sources. This assessment helps prioritize areas of high risk for implementing control measures.
- Control Measures: Based on the identified hazards and risk assessment, recommend and implement appropriate control measures to mitigate the risks associated with combustible dust. These measures may include improved housekeeping, dust collection systems, ventilation controls, explosion protection systems, and employee training.
- Documentation: Document the findings, analysis, and control measures in a DHA report. This report serves as a reference for ongoing safety improvements, regulatory compliance, and future reviews or audits.
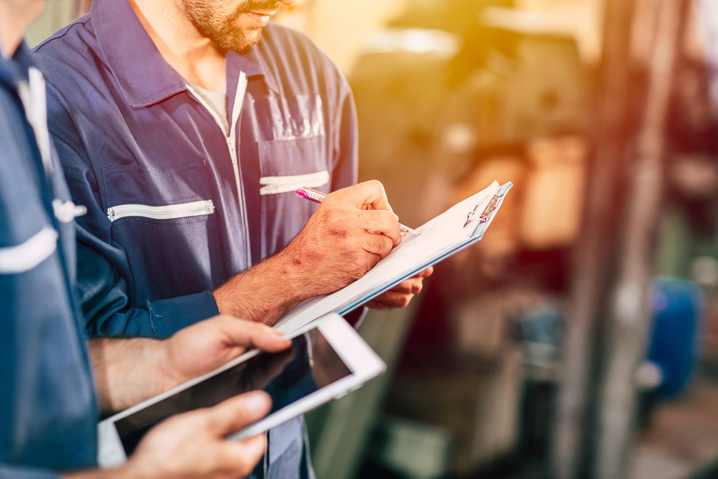
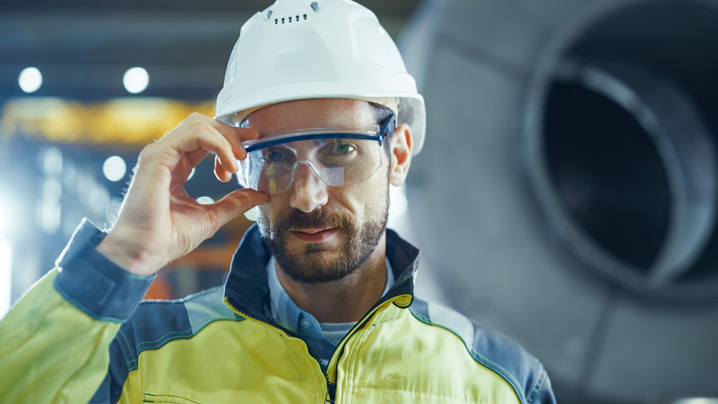
Mitigation is key to Reducing the Risks of Combustible Dust
To mitigate the risks posed by combustible dust, it is crucial to implement effective safety measures. Some common preventive measures include:
- Housekeeping: Regular cleaning and removal of dust accumulations from surfaces, equipment, and ventilation systems to minimize the potential fuel source.
- Explosion venting: Installation of explosion vents or panels in enclosures or equipment to allow the release of pressure and prevent the rupture of vessels during an explosion.
- Dust control: Employing engineering controls like local exhaust ventilation systems or dust collection systems to capture and contain dust at its source.
- Ignition control: Eliminating or minimizing potential ignition sources such as sparks, open flames, hot surfaces, electrical equipment that may generate sparks, or electrostatic discharges.
- Training and awareness: Educating workers about the hazards of combustible dust, safe handling practices, and emergency procedures in case of a dust-related incident.
It is important for employers and employees to be aware of the risks associated with combustible dust and to follow proper safety protocols to prevent accidents. By implementing appropriate preventive measures and maintaining a safe working environment, the potential for dust-related fires and explosions can be significantly reduced.
Standards and Safety Guidelines for Combustible Dust
Combustible dust safety refers to the practices and measures implemented to prevent and mitigate the risks associated with combustible dust in industrial settings. The goal of combustible dust safety is to protect workers, property, and the environment from the potential hazards of dust-related fires and explosions. In addition to the preventative measures notes above, here are some additional key aspects of combustible dust safety:
- Hazard Awareness and Training: Workers should receive training and education about the hazards of combustible dust, including its properties, potential ignition sources, and safe work practices. This awareness helps employees recognize and respond appropriately to potential risks.
- Emergency Response Planning: Developing and regularly reviewing emergency response plans specific to combustible dust incidents is crucial. This includes procedures for evacuation, firefighting, and containment, as well as providing training to employees on their roles and responsibilities during emergencies.
- Regulatory Compliance: Familiarize yourself with applicable regulations, such as the OSHA Combustible Dust Standard in the United States or similar guidelines in other countries, and ensure compliance with the requirements to maintain a safe workplace.
Regular inspections, audits, and ongoing monitoring of dust levels, equipment, and safety procedures are important to ensure the effectiveness of combustible dust safety measures. By adopting a proactive approach to combustible dust safety, organizations can significantly reduce the risk of dust-related incidents and protect the well-being of their workers and assets.Top of Form
It is important for companies to stay up to date with the laws and regulations that apply to their industry and their specific facility. Failing to comply with these regulations can result in fines, legal liability, and even criminal charges in some cases. Properly managing combustible dust risks can help protect employees and ensure the long-term success of the company.
Overall, combustible dust services are an important part of managing the risks associated with combustible dust. These services can help companies identify potential hazards, develop effective control and mitigation strategies, and ensure that employees are trained and educated to work safely in environments where combustible dust is present.
As awareness of the risks associated with combustible dust continues to grow, it is likely that the demand for combustible dust services will continue to increase. Companies that prioritize the management of combustible dust risks will not only protect their employees and their property, but they will also ensure their continued success and profitability in the long term.
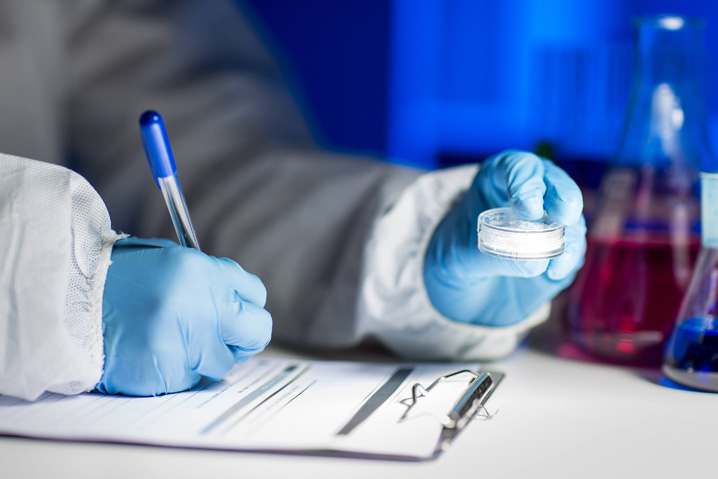
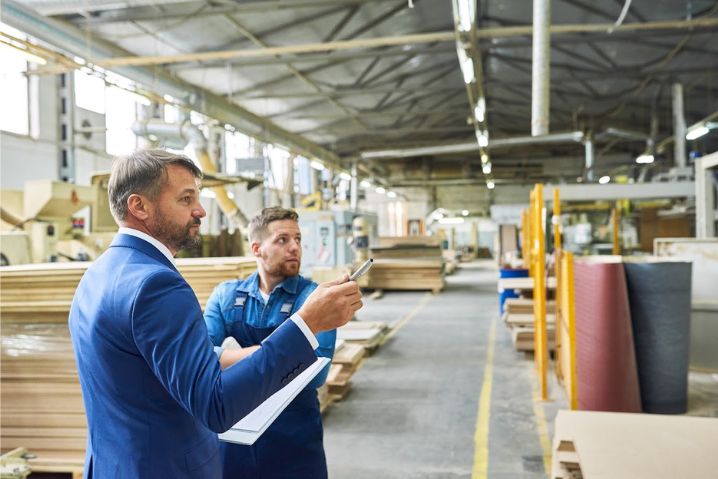
Addressing NFPA 652 Standard Regarding Combustible Dusts
Do you operate a facility that requires you to engage with substances that are dusty or powdery in n
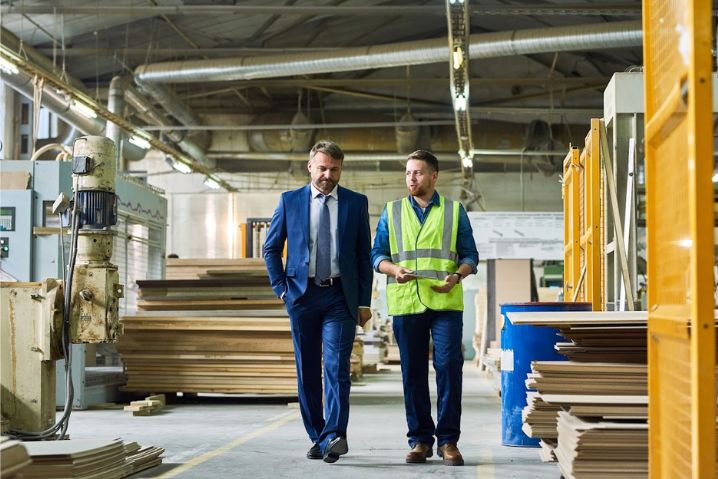
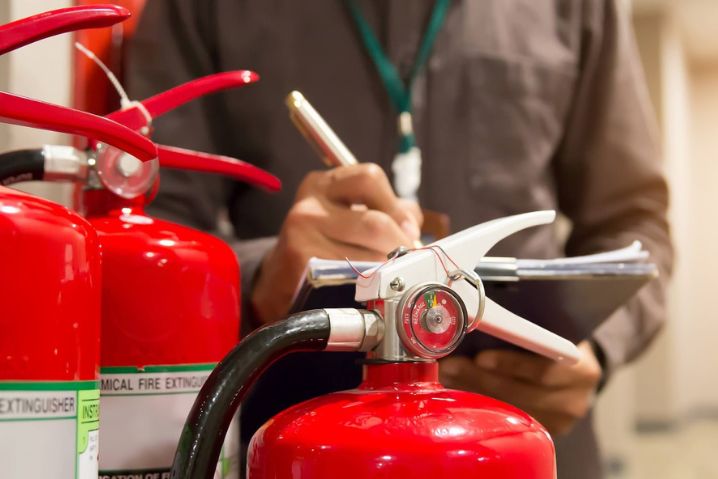
6 Industries Added by OSHA to the Combustible Dust NEP Program
n late January 2023, a new version of the Combustible Dust National Emphasis was issued by the Occup
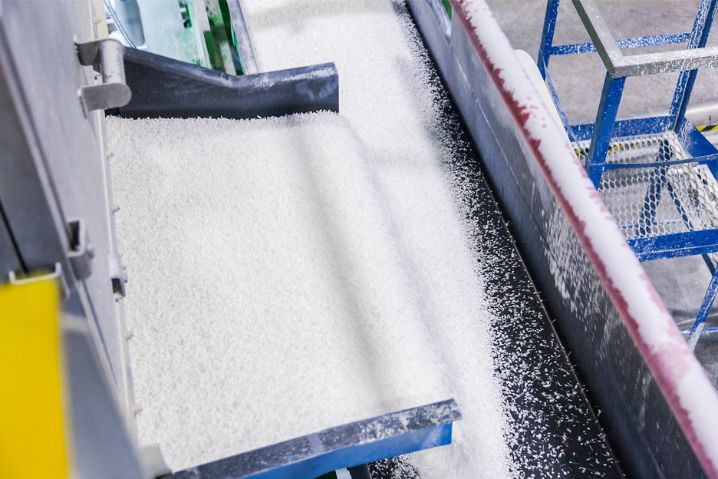
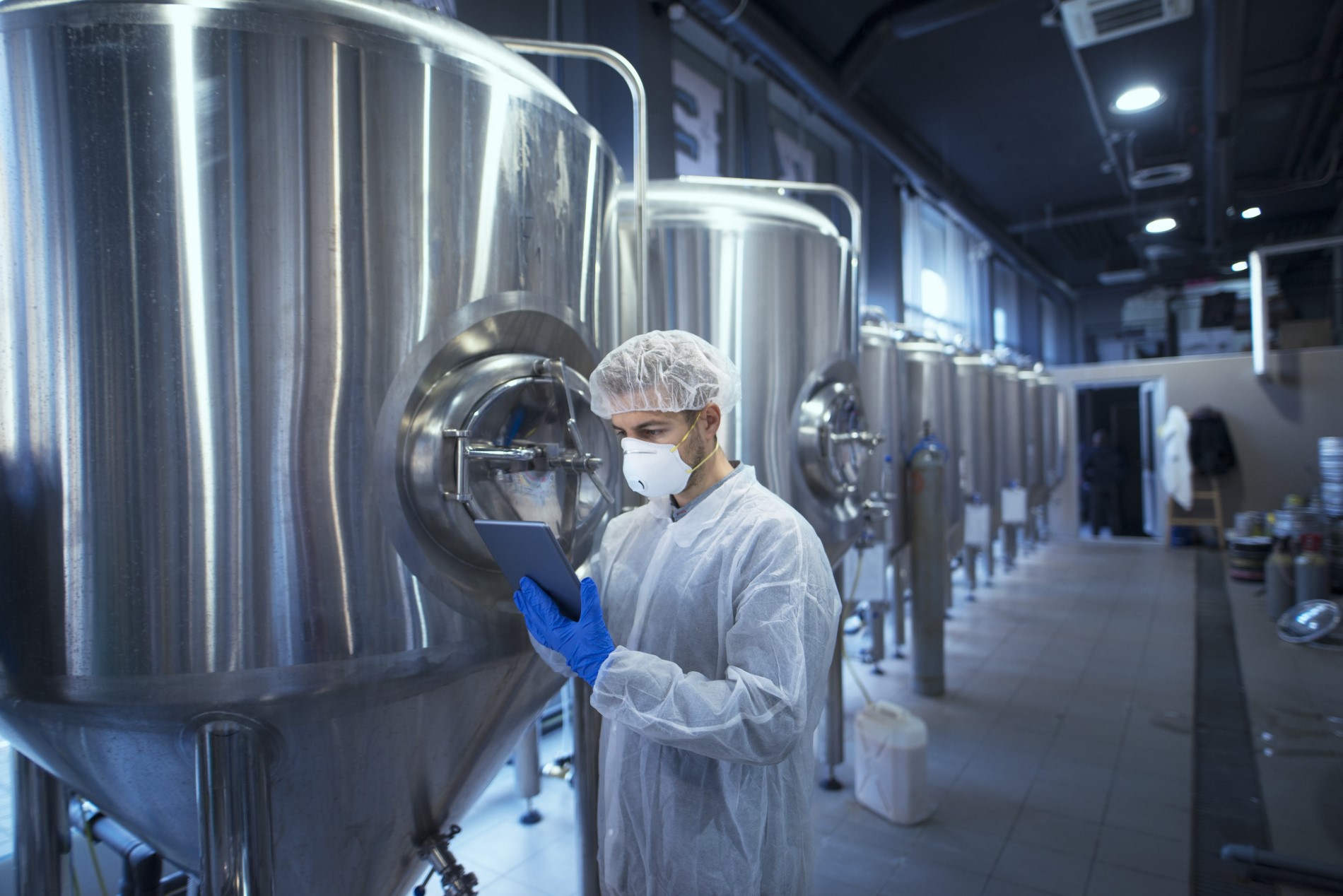
Ensuring the Safety of Facility Through Dust Explosion Test Data
“Could it be a problem if my powder has demonstrated 3mJ of minimum ignition energy and 256 bar.m/