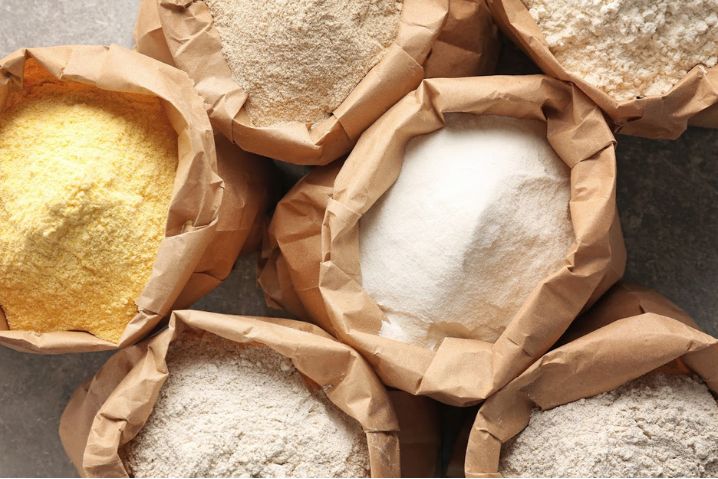
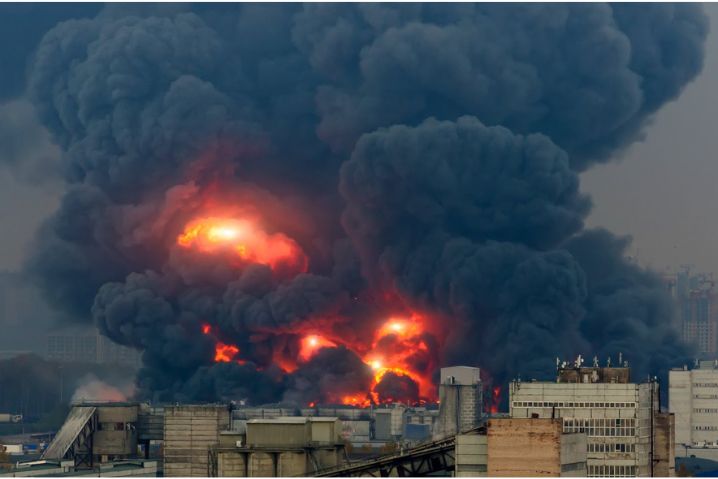
Electrostatic explosions and fires: Prevention
All of us, at some point, experienced electrostatic shocks. This may be at home, at a store, when pressing an elevator button or merely getting out of a vehicle. In all of these instances, we experience shocks because static electricity is discharged suddenly. While being merely annoying at home, in an industrial setup, they could cause catastrophes, such as explosions and flash fires. In particular, this holds true for the chemical process industries (CPI), since flammable solids and liquids are frequently handled in these plants in a manner that would inevitably produce static electricity. Frequently, such materials are flammable and static electricity can ignite them.
Static electric charge often gets generated in instances where two surfaces come into contact before separating. When the movement between the two surfaces is quick and forceful, the likelihood of static energy getting generated is higher. There are several processing operations in the CPI that are capable of generating static electricity, including the flow of liquids through the plant’s pipelines as well as the contact between powder particles and equipment surfaces. As a result, some processes, including fluidized-bed drying, pneumatic transfer, and tanker unloading and filtration, in which turbulent liquid is pumped, produce large amounts of static charge.
In an industrial context, static electricity is a factor to be wary of because it can lead to explosions and fires when electrostatic discharges ignite flammable atmospheres. Operations involving processing typically work with vapors, aerosols, dust clouds, and gasses that are flammable in nature. To prevent a fire, it is crucial to undertake precautionary measures. In terms of explosions and fires, several precautionary measures can be undertaken, although the mitigation of potential sources of electrostatic ignition in areas with flammable surroundings should be the first step.
Static electricity may be regulated in several ways, but it is crucial to learn more about the factors that lead to the generation and accumulation of static charges and the production of hazardous sparks that are extremely disastrous.
In this article, the areas in the CPI where the electrostatic charge can be generated as well as the reasons for its generation and accumulation are discussed. Finally, the pragmatic solutions that can be undertaken to mitigate the risk of flash fires associated with static electricity will also be discussed.
Charge generation theory
Electrostatic charges can be explained by various mechanisms, such as induction charging, double-layer charging, as well as contact electrification. Contact electrification. Contact electrification or triboelectrification, is a common method of electrostatic charge generation in the real world. Simply put, this occurs when two materials separate after brief contact. The electron arrangements within contacting surfaces alter in this scenario, and the surface that has an electron surplus is considered to be negatively charged, while the other is positively charged.
The collision of powder particles during pouring is a common example of such contact, as is the shoe’s sole touching the floor. There are many parameters that influence the extent of charge that emerges through contact electrification, including the surfaces’ chemical nature, the actual area of contact, contact pressure, as well as the conductivity of the surface.
When powders and bulk solids are processed or handled, the static energy generated is quite high due to the electrically insulating nature of the powders, along with their massive surface area per unit mass that is conducive to contact electrification.
Double-layer charging. The handling and processing of liquids generate electrostatic charges due to double-layer charging, which may occur at interfaces of solids and liquids as well as liquids and liquids. At the interface, similar polarity ions are adsorbed, which then attract opposite polarity ions present in the liquid. With this, a double layer is formed proximal to the interface along with its containing structure. Liquid’s potential is heightened by the oppositely charged ions shearing apart as it flows relative to the interface. When this occurs along ion recombination’s competing effect at the wall of the vessel, the charge within the liquid becomes unbalanced. A liquid flowing through a pipe experiences this kind of static charging. A number of factors can aggravate the generation of charges in liquids, including:
- Two-phase flow involving a continuous phase of a second liquid or solid
- Lined filters or strainers
- Any process leading to a lot of spraying as well as splashing
- Stirring or mixing-induced movement
Despite being well grounded, a plant can still undergo double-layer charging. Electrically grounding a plant is important, but will not prevent the generation of charges alone.
Induction charging. If an electrically insulated conductive object either enters or exits an electric field, including one that encompasses a charged object in proximity, it could lead to induction. In such a field, the object that is conductive could lose or gain its charges, wherein the exact rate is determined by its resistance as well as capacitance to ground. The adequate charging of the conductor through induction could lead to electrostatic discharge. It is possible to control these induction charges by grounding conductive objects.
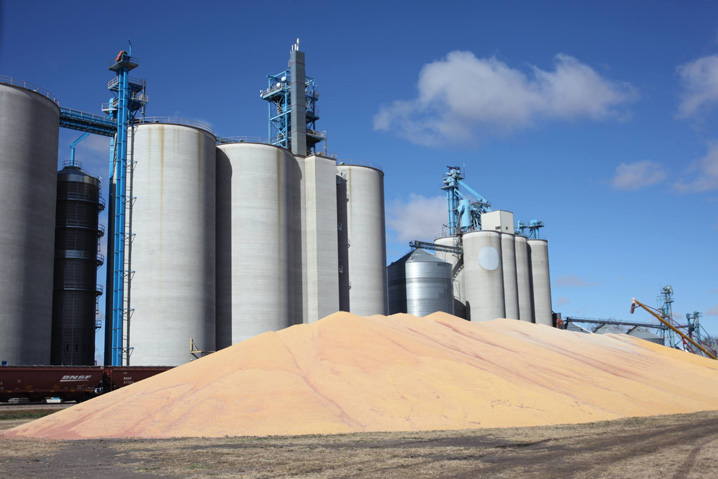
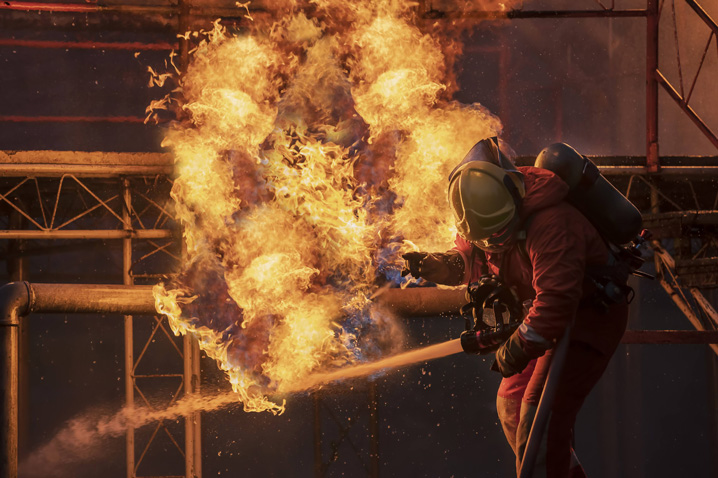
Accumulation of charges
It is not always necessary that electrostatic generation is dangerous. But the buildup of electrostatic charges over facility structures, individuals, liquids, and powders may lead to harmful electrostatic discharges.
Plant, equipment, and personnel. Plant structures, equipment, or people electrically isolated from the ground can accumulate charge when it has no other means to escape. An ignition risk may emerge when the voltage rises as a result of charge buildup in hazardous areas with a flammable environment. If insulating entities or equipment are present in such areas, the insulators’ surface may discharge electrostatic charges to a small extent. Sometimes, they might even result in ignition if they are present in a flammable environment.
Powders and liquids. During charging, any powder or liquid that is not a good conductor (high electrical resistivity), may experience charge buildup. Such materials are capable of holding a charge for long periods of time, even in instances they are physically connected to a structure from the plant that is connected to the ground electrically.
Electrostatic discharges. When there are two surfaces or objects with varying electrostatic potentials, it leads to electrostatic discharges. Increasing the charge on an object or surface intensifies the electric field above it. The strength of the field between two objects can cause an electrostatic discharge if the field strength exceeds the break-down threshold in the atmosphere between them. While the energy content of such discharges varies, it could be adequate to cause an ignition in a flammable environment, particularly in CPI plants with dust clouds, vapors, gasses, as well as aerosols.
The exact amount of charge that builds up as well as the surfaces’ electrical characteristics determine the effective discharge energy. Identifying the type and location of potential discharges gives engineers an idea of how much energy will be generated during the discharge.
Typically, when compared to the discharge from people, the discharge’s maximum energy is significantly higher when it comes from conductors. The former, however, may be higher when compared to discharges from plant equipment (when insulating material is involved) as well as bulk powders. In the sections that follow, we explain how these maximums overlap and how exceptions apply to them.
Thus, both the electrostatic discharge’s static electricity as well as ignition sensitivity to flammable atmospheres determines the ignition potential in the context of a flammable atmosphere. Flammable atmospheres are characterized by a property called ignition sensitivity. It is common for electrostatic discharges to have varying effective energies in a process environment, but most of the time they are limited. In the following sections, we expand on these concepts.
Flammable atmospheres
When it comes to electrostatic discharges, their greatest threat is that they can cause flammable atmospheres to ignite. However, deflagration or a vapor fire only occurs if there is: (1) an oxidant; (2) a fuel; and (3) an ignition source with adequate energy. There are two more elements required for a dust explosion: (4) a mechanism to disperse dust; and (5) an enclosure in the facility or within the machines. However, the presence of all the components is not an adequate determinant, since the concentration of the fuel and oxidant mixture should fall within a particular range in terms of concentration to cause an explosion or a flash fire.
The flammable atmosphere’s minimum ignition energy (MIE) must be less than the effective discharge energy for it to get ignited by an electrostatic discharge. The lowest electrostatic discharge energy that can cause the ignition of a flammable atmosphere, when its concentration makes it easily ignitable, is defined as the MIE. For the majority of organic vapors as well as hydrocarbon gasses, the MIE falls between 0.1 to 1.0 millijoules (mJ), and for the majority of dispersed dusts, the value of MIE falls exceeds 1,000 mJ and can be less than 3 mJ. Since minor differences in composition or physical characteristics can have a significant effect on the MIE of gasses, vapors, and dusts, MIE data should be collected on a process-specific basis. For example, a decrease in the size of a particle or the amount of moisture will lead to a significant decrease in the MIEs of several dusts and powders. It is rational to compare a flammable atmosphere’s MIE with electrostatic discharges’ effective energy.
Regulating electrostatic threats
In CPI plants, it is necessary to mitigate electrostatic hazards by undertaking steps that not only prevent ignition but also safeguard the facility as well as the employees from the implications of an explosion. Sometimes, it is not easy to determine how static electricity is generated and whether it can act as a hazard, so it requires special attention. To control electrostatic hazards, the approach is five-fold:
- Obtain data pertaining to the existing flammable atmospheres, which includes information about their flammability as well as electrostatic characteristics
- Obtain data about the structures in the facility, the equipment used, and the materials employed in various processes
- Conduct a charge generation and accumulation assessment of operations, various facilities in the plant, machines, and people
- Undertake steps for the mitigation of static electricity
- A process safety approach should be undertaken to drive changes with an emphasis on preventing flammable atmospheres, controlling all ignition sources, and protecting people and plant structures from the implications of explosions and fires.
Electrostatic characteristics
When it comes to analyzing electrostatic hazards, it is necessary to obtain information pertaining to n flammable atmospheres as well as the electrostatic characteristics of the substances undergoing processing, handling, and more. This includes:
- Flammable atmospheres’ MIE
- Conductive objects’ resistance-to-ground
- Operator’s body to ground electrical resistance
- Liquids’ and powders’ electrostatic chargeability or during processing, electric field or voltage of the surface
- Powders’ volume resistivity
- Liquids’ conductive nature
- For solid objects, the surface resistivity\
According to National Fire Protection Association (NFPA) Standard 77, Recommended Practice on Static Electricity, there are various measures that can be undertaken when it comes to mitigating the hazards that pertain to static electricity production, discharge, and buildup. The same standard also delves into static electricity’s nature and outlines various guidelines to find and analyze static electricity’s hazards and solutions to mitigate them.
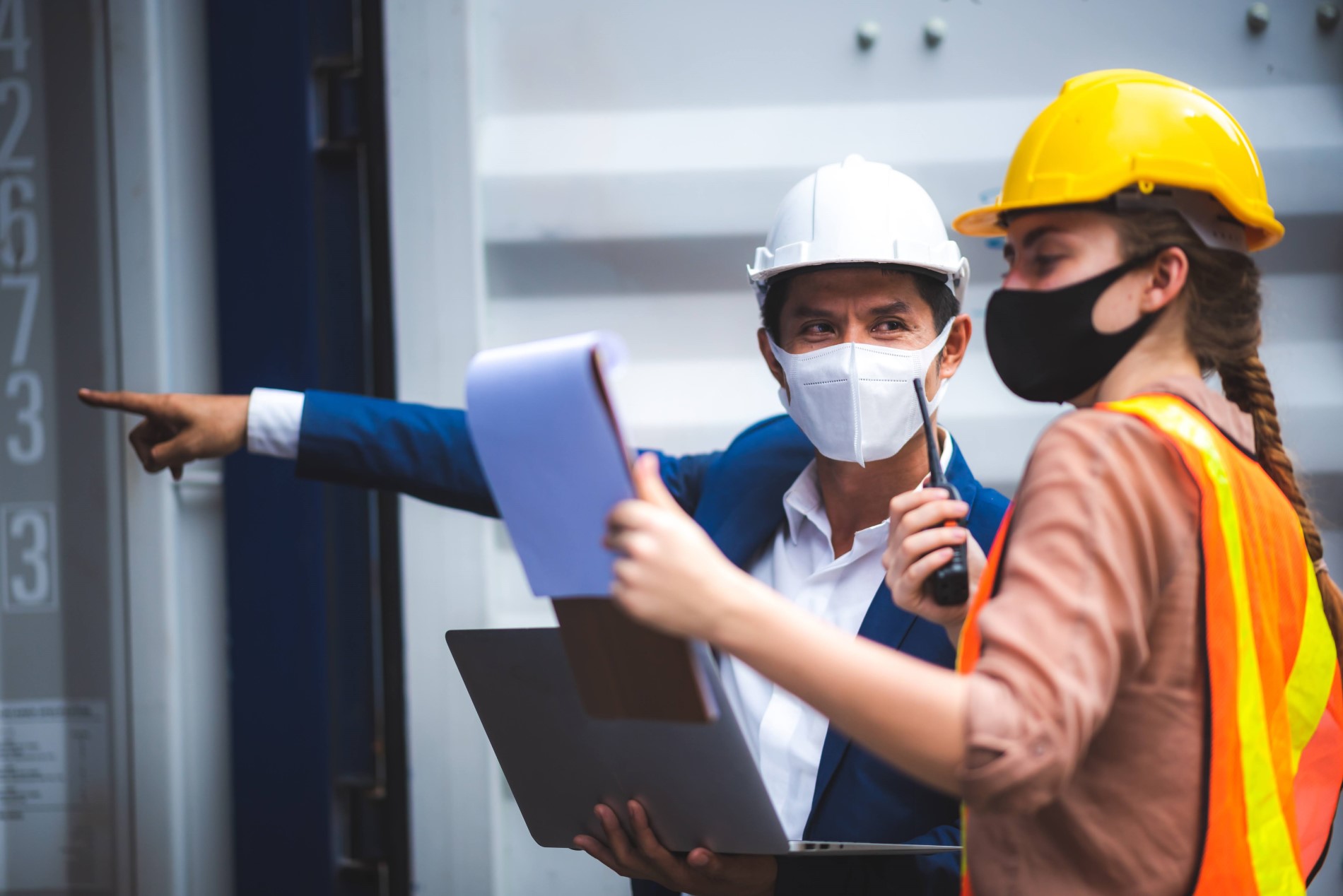
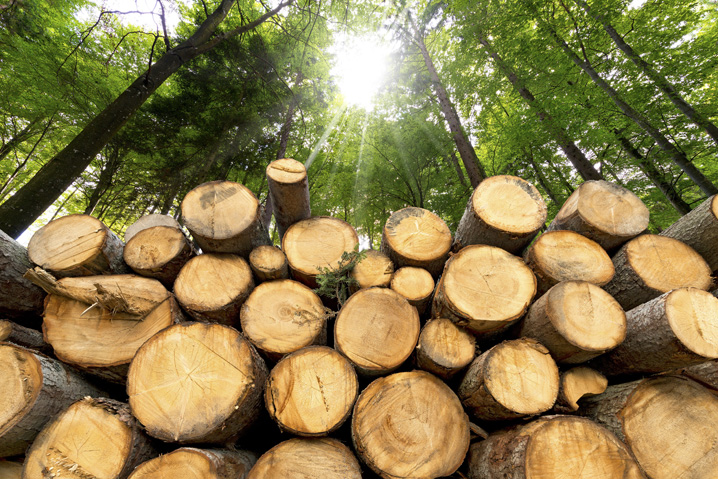
Process, machines, and individuals
It is important to look at the steps to take to mitigate explosions and flash fires that could emerge as a result of electrostatic discharges that are generated during mundane processes at CPIs. We will also look at how processes can be analyzed to determine their risks pertaining to the generations of charges and regulate static electricity.
Conductive structures. Metal pipes, equipment, vessels, and containers should be tested for their electrical resistance to the ground. There must be a direct ground connection if the resistance exceeds 10 ohms. The importance of checking ground connections on a regular basis should be understood by operators and maintenance personnel and it must be practiced regularly.
Employees. Walking around, wearing or removing overalls, or pouring liquids or powders can result in potentials of 10 to 15 kV for employees wearing insulating footwear or working on insulating floors. Sparks with discharge energies up to about 30 mJ can be generated by electrostatically charged individuals. Electrostatic sparks from operators can be reduced by taking the following measures:
- An effective grounding system should ensure that personnel is not more resistant to the ground than 1 ✕ 108 ohm. The best way to achieve this is to install static-dissipative or conductive flooring and wear shoes with ground resistance between 5 ✕ 104 and 1 ✕ 108 ohm
- Whenever static-dissipative footwear is worn, the operator should stand on a surface with a resistance of less than 1 ✕ 108 ohm
Insulating materials. There are many materials with insulating characteristics, such as liners, plastic bags, drums, pipes, and vessels with glass lining, as well as hoses. Their surface resistivity usually exceeds 1 ✕ 1011 ohm/square. Merely rubbing items such as liners can cause them to become electrostatically charged, which creates brush discharges, which are only capable of igniting atmospheres that are flammable sand made up of vapor or gas with a MIE that is less than 4 mJ. When powders are pneumatically conveyed via non-conductive pipes, the latter’s internal surfaces may become extremely charged, which could create propagating brush discharges. When liquids that are highly charged enter containers that are non-conductive, the latter’s internal surfaces can become charged, leading to propagating brush discharges, which are capable of igniting any gas or vapor atmosphere that is flammable and with an MIE that is less than 2,000 mJ.
Electrostatic charges will not be relaxed to the ground due to non-conductive materials undergoing grounding. It is best to employ materials that are static-dissipative or conductive in order to prevent both propagating brush and brush discharges, provided their surface resistivity does not exceed 1 ✕ 1011 ohm/square.
Liquids. Several operations where a liquid is handled could lead to static electricity hazards, which include filtering, mixing, sampling, and filling. When handling and processing liquids, a buildup of electrostatic charges can occur over: (1) bulk liquids that are present in vessels that are non-conductive; (2) liquids with low-conductivity; as well as (3) liquid mists, no matter what the conductivity of the liquid is. To mitigate the hazards of electrostatic ignition, the following steps can be taken:
- Electrically conduct and ground the plant — piping, vessels, containers, and so on, should all be grounded and electrically conductive.
- The conductivity of liquids can be raised — in very small concentrations, antistatic additives can increase liquid conductivity
- Valves and filters must be designed effectively and placed well — Valve diameters should be as large as possible. Avoid placing filters and valves near receiving vessels
- Entry of liquid into a vessel should be regulated — submerged drip legs or bottom inlets should be used for entry
- Here are some guidelines for regulating flow velocity:
- Liquids whose conductivity exceeds 100 pS/m: no restrictions on flow velocity
- Liquids devoid of immiscible components and whose conductivity does not exceed 100 pS/m: a flow velocity that does not exceed 7 m/s
- Liquids with immiscible components and whose conductivity does not exceed 100 pS/m: flow velocity must not exceed 1 m/s
Powders. When powder particles with high charges enter a vessel, the surface of the bulk powder may accumulate discharges when the vessels are being filled. They are referred to as cone or bulk charges and their energy is dependent on the size, electrostatic chargeability, and volume resistivity of the powder as well as the dimensions of the vessel, with their maximum energy usually capped at 25 mJ.
There will be no bulk discharges when the volume resistivity of a powder is less than 109 ohm∙m and if its handling occurs in a plant that is conductive and grounded. But an insulating powder with an MIE that is less than 25 mJ, with an electrostatic charge quantity that is adequate to result in bulk powder’s surface producing discharges, would require these measures:
- Inert-gas blanketing must be employed
- Measures that protect against and isolate explosions should be implemented
- Measures should be taken that mitigate the production and buildup of electrostatic charge
Humidity’s impact on charge buildup. Surfaces absorb water vapor from the air, forming a slightly conductive layer. Surface and atmosphere humidity determine how much water absorbs and increases conductivity. Electrostatic effects may significantly be reduced if the relative humidity is above 65% and at approximately 20°C.
Preventing Explosions
Finally, explosion prevention measures must be explored and implemented while avoiding risk factors, such as flammable atmospheres as well as unrestrained ignition sources.
Removing flammable atmospheres. An explosion or fire is more likely to occur if flammable atmospheres can’t be prevented or all ignition sources can’t be eliminated. Inert gasses can be used to blanket or purge flammable atmospheres to prevent their formation. By reducing a vessel’s or system’s relative oxygen concentration with inert gasses, no fire or explosion can occur, wherein the value is referred to as the limiting oxygen concentration (LOC).
Protection against explosion. A number of measures are available to protect against explosions, including containment, suppression, and relief venting. Having vessels and equipment designed so they can withstand and contain the maximum explosion pressure is an effective way to contain an explosion. A relief vent is a panel installed on equipment that opens at a lower pressure than the equipment’s design pressure. Overpressure is prevented and explosion pressure is relieved to a safe location. When an incipient explosion is developing, a suppressant is quickly introduced to prevent hazardous pressure from building, thus protecting the equipment from damage. In addition to these measures, explosion isolation is often employed, which prevents fire and explosions from spreading between units or transferring between areas.
Conclusion
CPI plants often contain flammable vapors and powders that are ignited by discharges of static electricity. These discharges have caused many industrial fires and explosions. Solids or liquids tend to generate electrostatic charges when they come into contact with one another and are then separated. When flammable liquids and powders are transferred, handled, processed, and packaged, electrostatic charges can form and accumulate, and sometimes discharges can occur as a result. It is when discharges have more energy than necessary to ignite flammable vapors or dust clouds that they cause fires and explosions.
It is, thus, necessary to design and implement protective measures that are customized to your facility’s needs and requirements. Knowledge about these measures should be accessible to every employee.
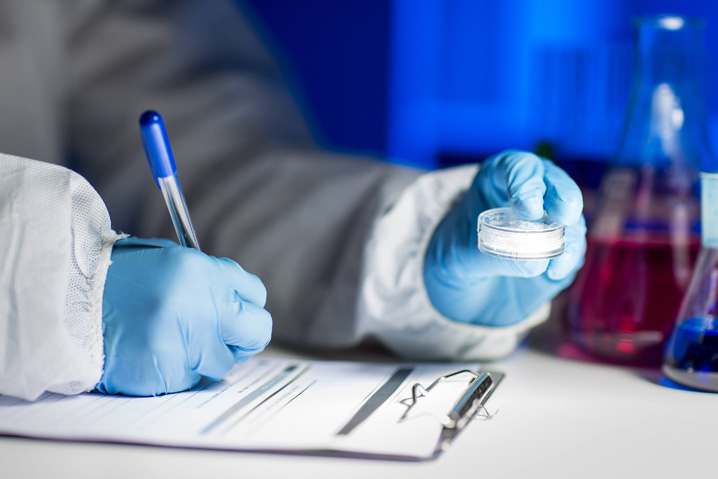
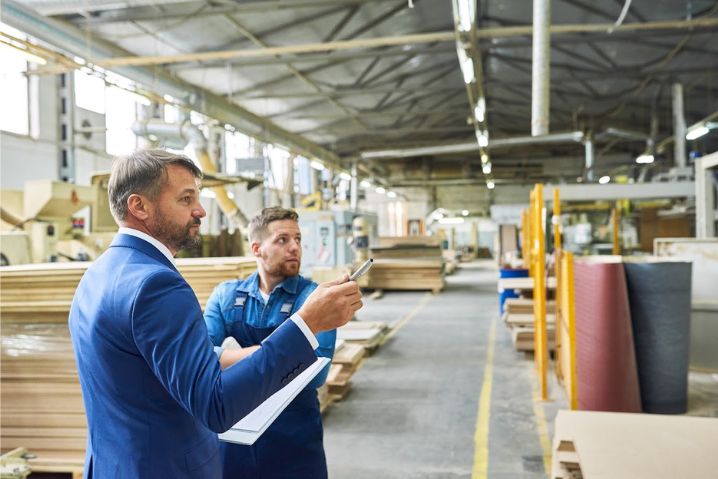
Addressing NFPA 652 Standard Regarding Combustible Dusts
Do you operate a facility that requires you to engage with substances that are dusty or powdery in n
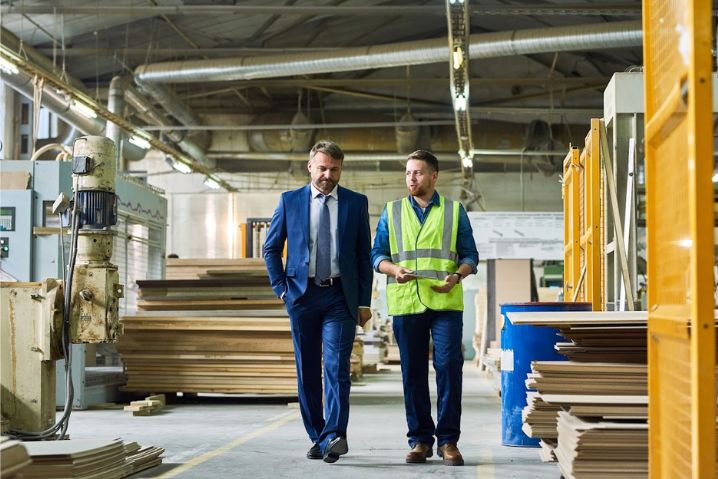
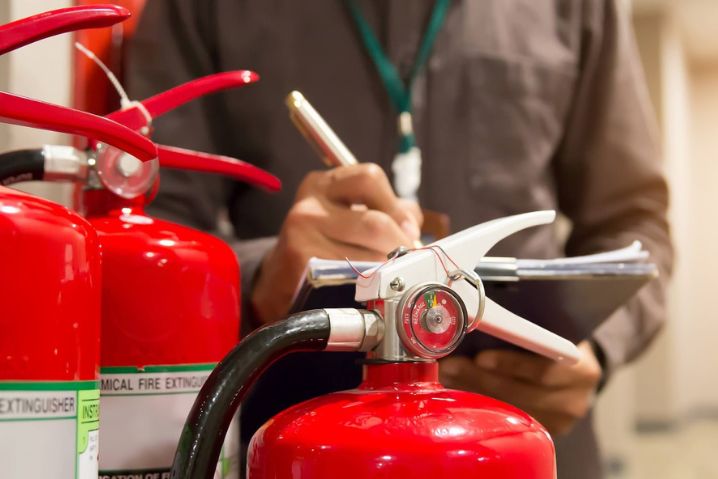
6 Industries Added by OSHA to the Combustible Dust NEP Program
n late January 2023, a new version of the Combustible Dust National Emphasis was issued by the Occup
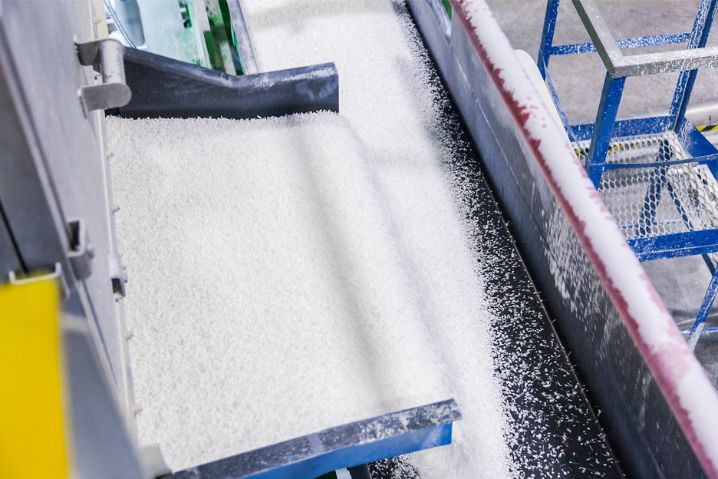
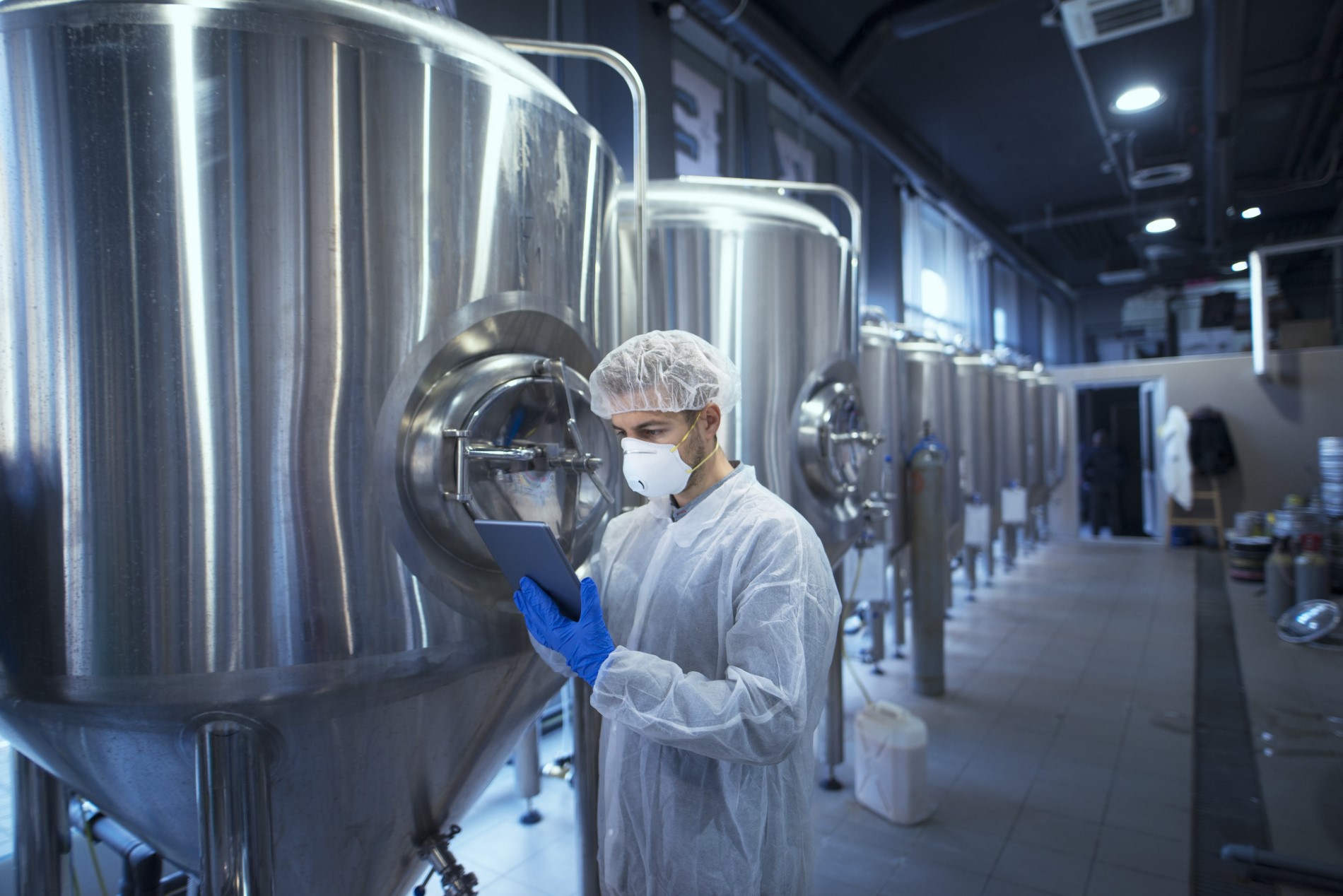
Ensuring the Safety of Facility Through Dust Explosion Test Data
“Could it be a problem if my powder has demonstrated 3mJ of minimum ignition energy and 256 bar.m/