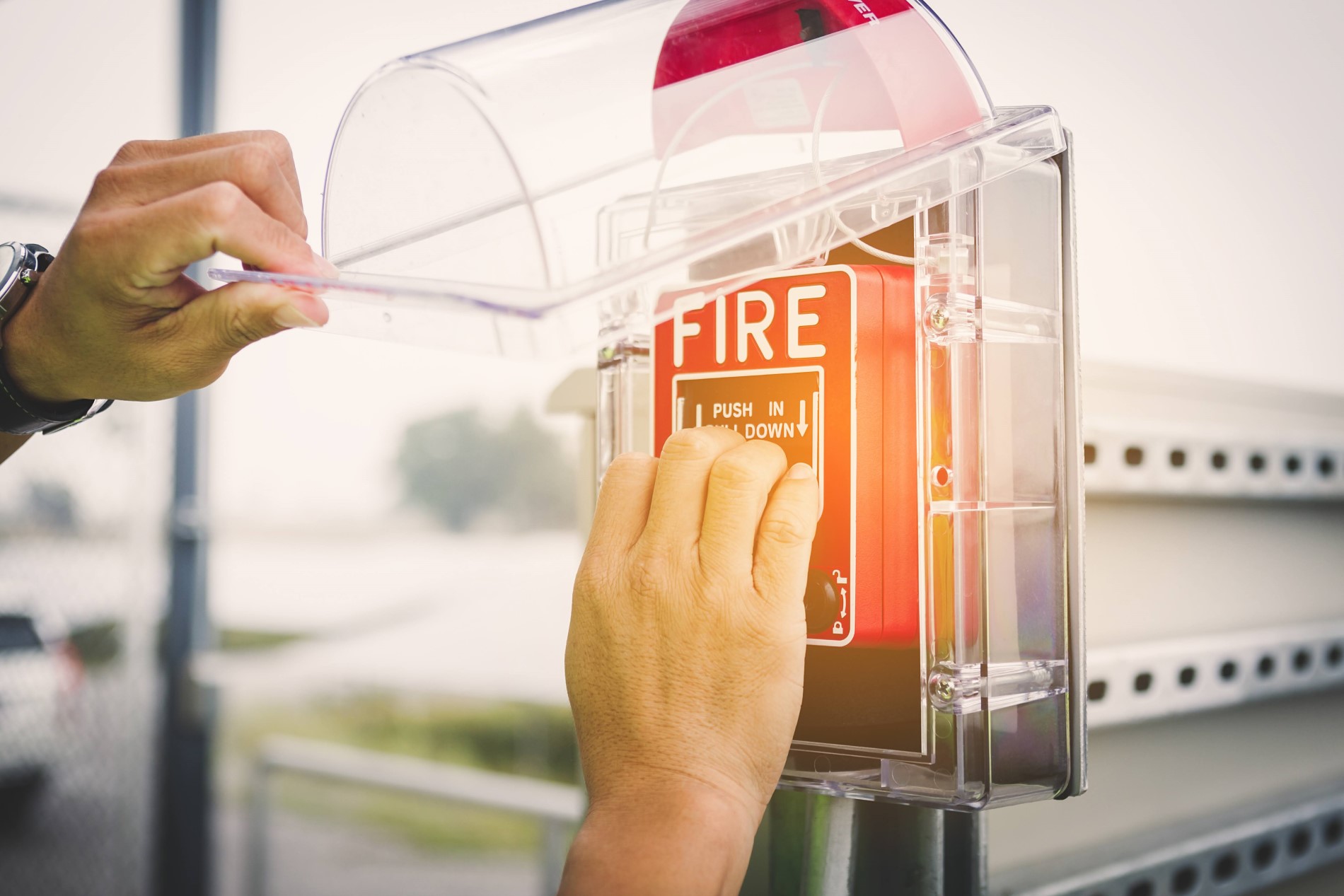
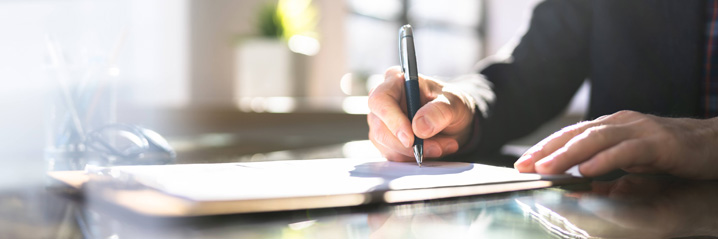
Compliance management for combustible dust in manufacturing
Standards to Protect You
For preventing fire, the National Fire Protection Association (NFPA) has been established, which developed NFPA 652 to eliminate the ambiguity surrounding the standards that are specific to industries and commodities (NFPA 61, 484, 664, 654, 655). By devising a hierarchy involving these standards, it makes sure that industries, dust types, and processes are all taken into account when it comes to managing explosions and combustible dust fires. It is crucial to adhere to this standard if the objective is to prevent combustible dusts. A comprehensive standard will soon be introduced by the NFPA (660), which will be effective from October 2023, as per reports, and will combine NFPA 652, 484, 61, 655, 654, and 652.
The NFPA’s safe housekeeping requirements cannot simply be ignored by industries without a specific standard that addresses combustible dust. Dust tests are mandated by NFPA 652, and the results must be documented.
Why makes the Dust Test Pertinent?
Previously, location class was employed by companies to select equipment. That does not suffice today since combustible dusts might be handled in non-classified hazardous locations in some cases. The steps to take to remain compliant and safe are determined by the dust, which is why a dust test is important.
The dust’s class is determined by the Kst value and if the latter is greater than 0, a dust hazard analysis (DHA) is mandated by NFPA 652. Other properties of the dust, such as its minimum ignition energy (MIE), should be taken into account when determining your risks. However, dust classified ST1 and above requires a DHA.
Cleaning Documentation and Follow-up
The housekeeping procedures must be documented in a DHA and must also entail particular items for the safety of your facility and employees. Housekeeping is very important for managing combustible dust and may be a truly effective method for minimizing your risks, provided the processes are followed properly and using the right equipment.
There are recommendations provided by OSHA and NFPA when it comes to cleaning. According to the OSHA National Emphasis Program, these measures are recommended :
* Periodically, dust residues should be cleaned
* The cleaning methods employed should not cause dust clouds in the presence of sources of ignition
* Dust must only be collected using vacuum cleaners
* All of the horizontal surfaces must be cleaned frequently to avoid the buildup of dust within procedural areas of the plant
* The thickness of the buildup of dust should not exceed 1/32-in.
* Any cleaning device that is electrically powered must be approved for the hazard classification before getting utilized in dusty regions
Similar recommendations are provided by NFPA 652, which suggests the use of a vacuum cleaner for cleaning on an everyday basis. However, vacuuming is not ideal in scenarios such as bulk spills, in which case vacuuming should follow shoveling. A washdown is also an option, provided your application is suitable for this method. One section in NFPA 652 discusses compressed air blowdown and claims that it poses a serious hazard since it can create hazardous dust plumes. It must only be employed if other measures can cause even serious hazards.
Housekeeping is emphasized heavily by both NFPA and OSHA. Proper cleaning can help prevent both primary and secondary explosions.
Utilize Good Cleaning Equipment
NFPA specifies vacuum design requirements, even though the organization does not approve or certify equipment. It is sometimes necessary to use third-party certified equipment even in non-classified hazardous areas as per the standard, such as when flammable vapors are present or combustible dust spills occur.
Equipment criteria for hazardous areas are also specified by OSHA, NEC, and NFPA, which mandate “approved” equipment. Ensure your equipment manufacturer has NRTL certification if you are required to use “approved” equipment by your local AHJ or by your classed location. Determine the best equipment with the assistance of your DHA and AHJ.
When it comes to maintenance plans, instruments such as compressed air, brooms, mops, and vacuums are all important. Several employees, unfortunately, do not consider the ramifications of employing inefficient equipment. When the wrong equipment is used for the cleanup of combustible dust, it may lead to exorbitant costs in terms of fines, health insurance, and labor. In order to ensure safety and avoid the imposition of fines when collecting combustible dusts, it is best to employ industrial vacuum cleaners that are equipped with effective filters, including ULPA and HEPA filters.
A vacuum cleaner as a whole can be certified and is the safest type to use in hazardous environments. Manufacturers of vacuums may advertise certification for parts such as motors and switches, indicating the entire vacuum is not NRTL-certified. To find out whether your vacuum manufacturer has NRTL approvals, consult your vacuum manufacturer.
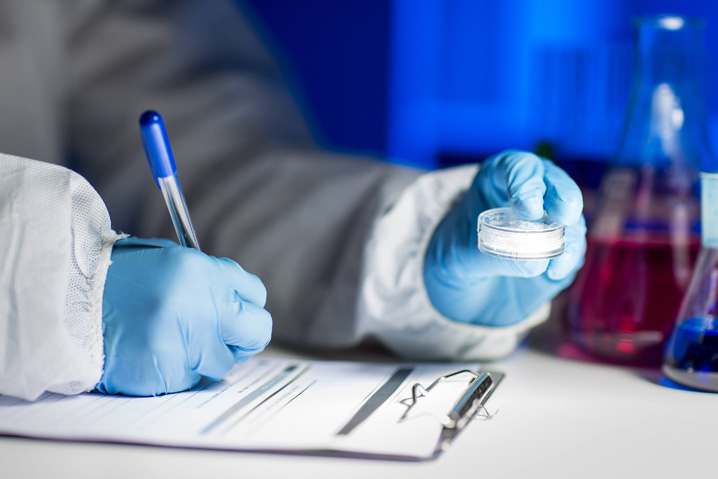
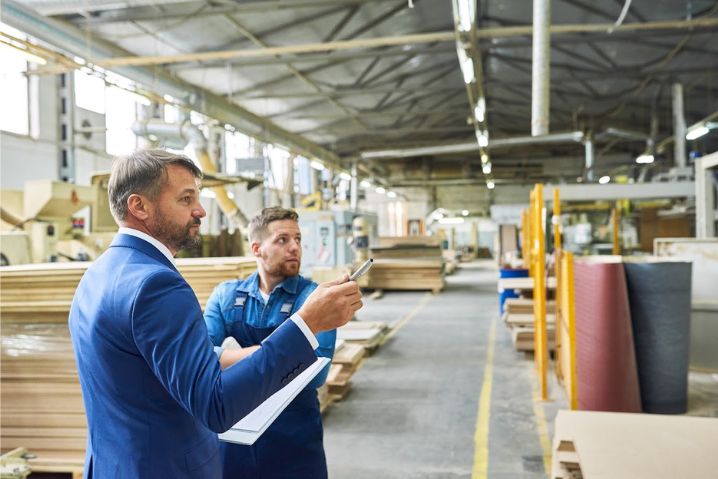
Addressing NFPA 652 Standard Regarding Combustible Dusts
Do you operate a facility that requires you to engage with substances that are dusty or powdery in n
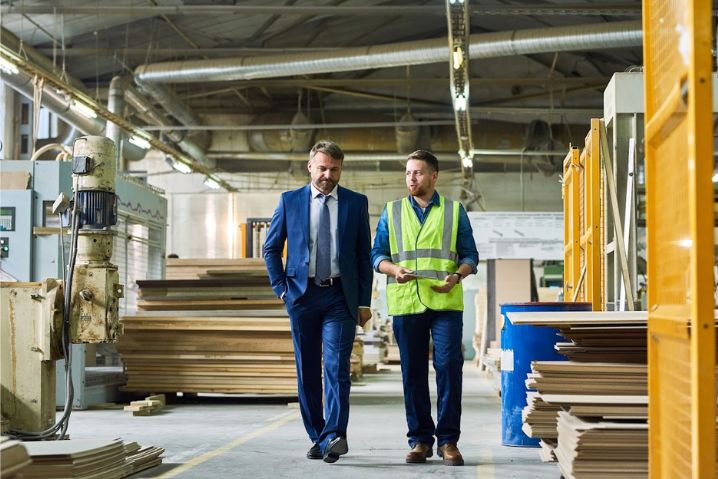
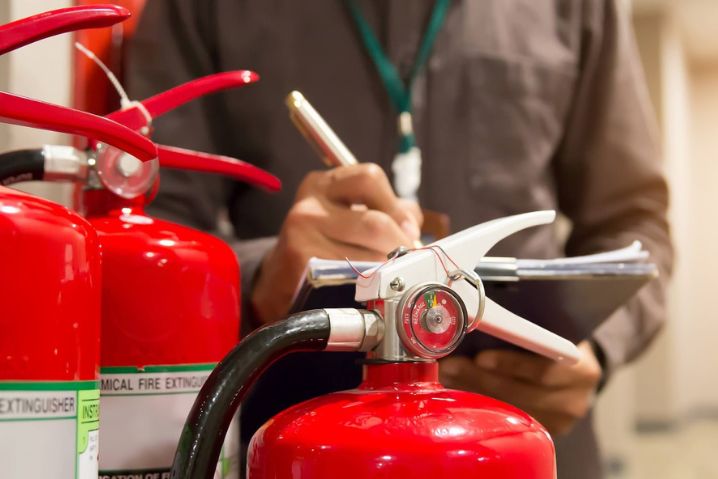
6 Industries Added by OSHA to the Combustible Dust NEP Program
n late January 2023, a new version of the Combustible Dust National Emphasis was issued by the Occup
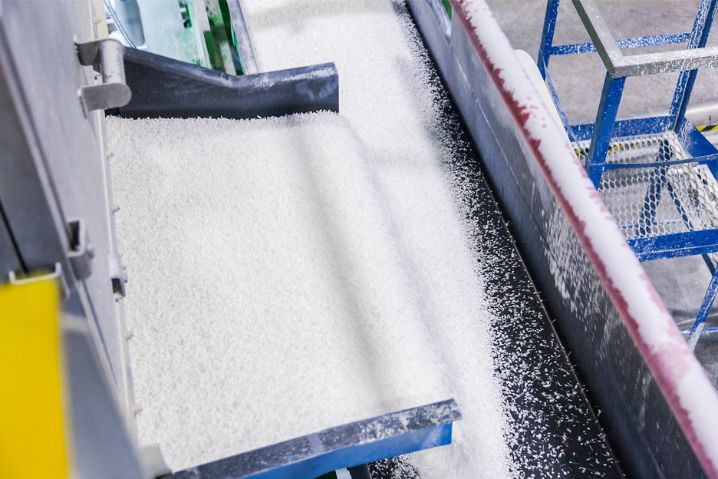
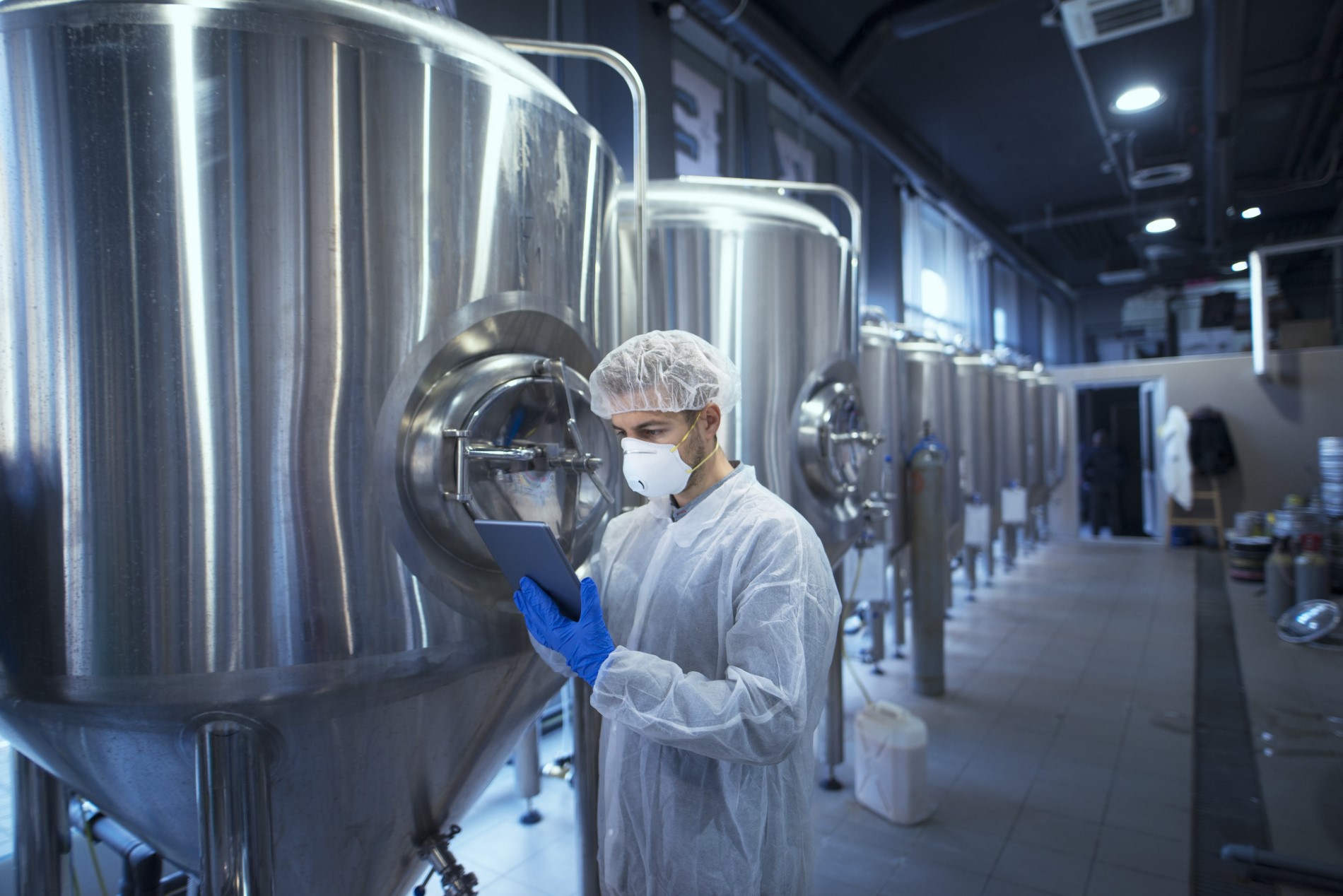
Ensuring the Safety of Facility Through Dust Explosion Test Data
“Could it be a problem if my powder has demonstrated 3mJ of minimum ignition energy and 256 bar.m/