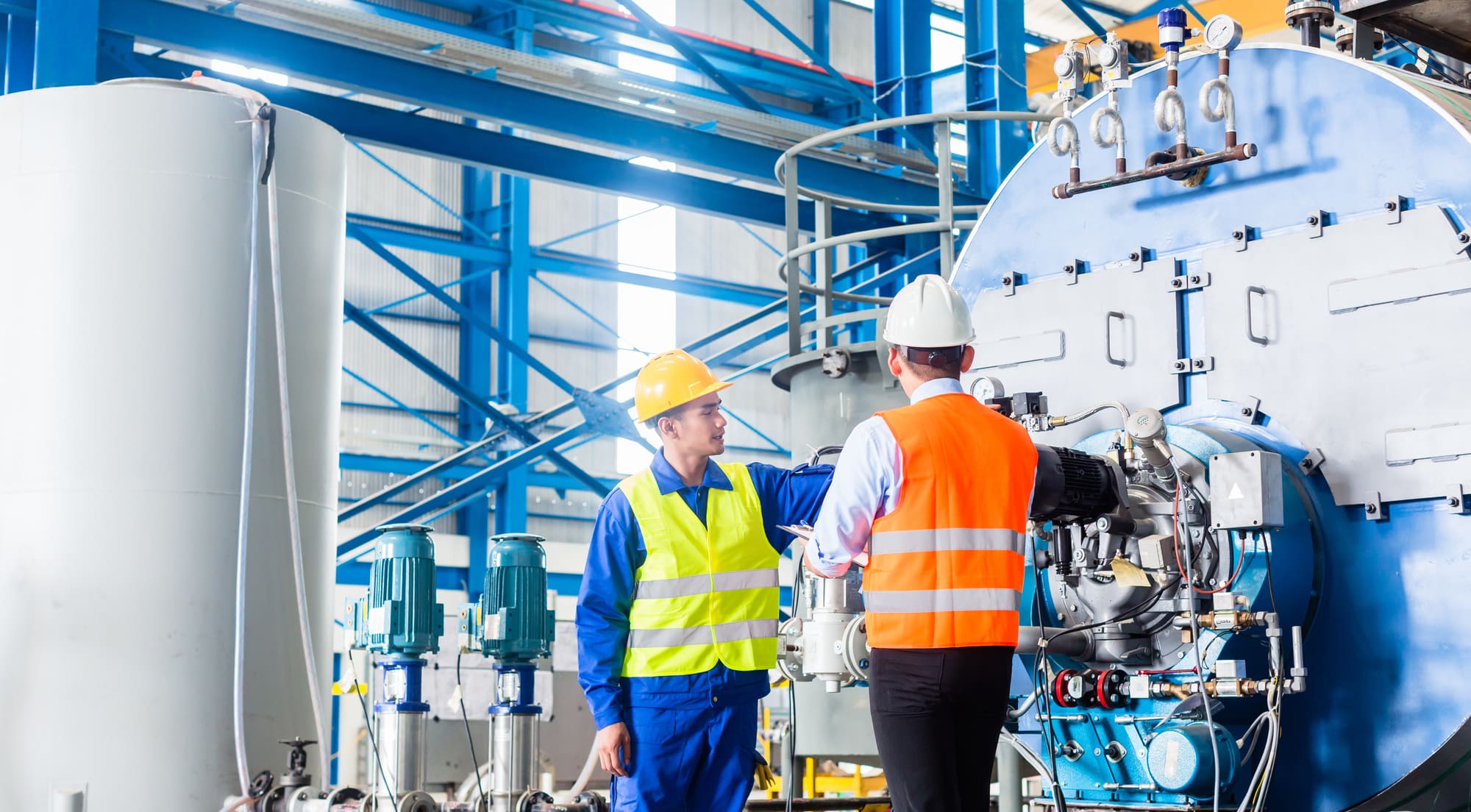
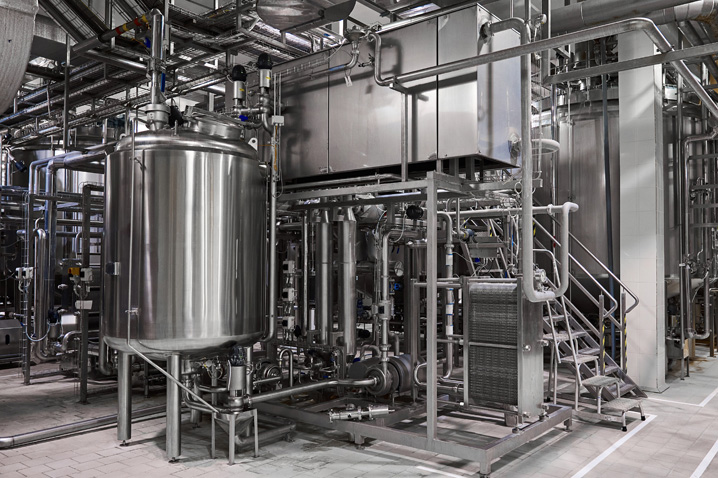
What is a dust explosion and how do I know if my facility is at risk?
A dust explosion is a catastrophic event that occurs when finely divided particles of combustible material (such as dust, grain, flour, or sugar) become suspended in the air and make contact with an ignition source, such as a spark, flame, or hot surface. This creates a rapid combustion process that generates a wave of pressure, heat, and flames that can cause significant damage, injuries, and fatalities.
Dust explosions are particularly dangerous because they can occur in a wide range of industries and settings, including (but not exclusive to) manufacturing, agriculture, food processing, and woodworking. Dust explosions are triggered by a variety of sources, such as static electricity, overheated machinery, friction, and welding, among others. To prevent hazardous dust explosions, it is important to properly manage and control dust accumulation, minimize potential ignition sources, and implement appropriate safety measures such as ventilation, dust collection, and explosion suppression systems.
A dust explosion occurs when the right elements are consistently present, known as the “Dust Explosion Pentagon.” These elements are:
- Combustible Dust: This is the fuel for the explosion. It can be anything from wood dust to sugar, grain, coal, plastics, and metal dust, among others.
- Oxygen: Oxygen is the oxidizing agent that supports combustion.
- Ignition Source: This is the spark or heat source that initiates the explosion. Ignition sources can be anything from electrical equipment, open flames, welding, friction, and static electricity, among others.
- Dispersion: The dust must be in a finely divided state to create a combustible mixture with air.
- Confinement: The dust cloud must be confined within a space, such as a vessel, room, or pipe.
When these five elements come together, a dust explosion can occur. Typically, the initial explosion will cause a pressure wave that can disperse more dust and ignite secondary explosions, leading to a chain reaction that can rapidly spread throughout a facility.
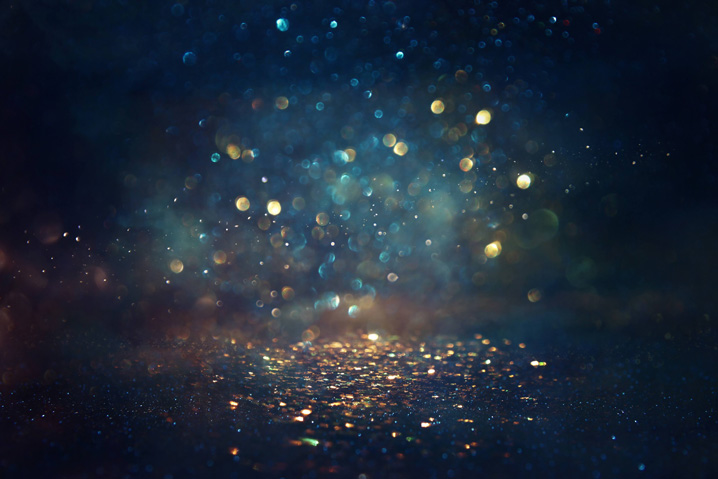
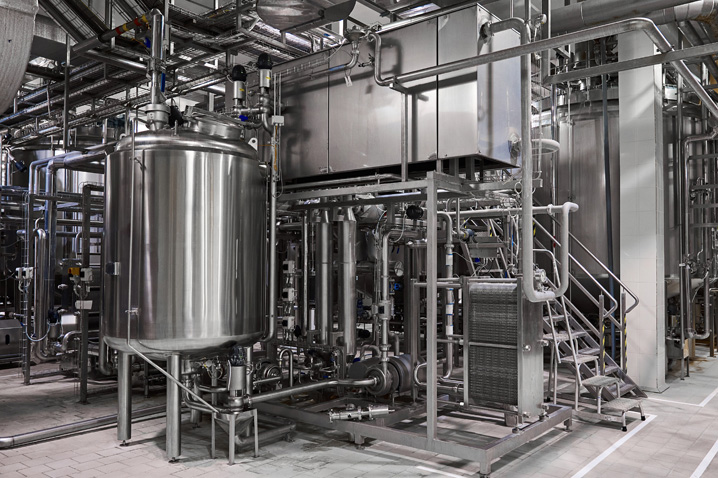
Secondary Explosions
In some tragic situations, a secondary dust explosion may occur. A secondary explosion is a subsequent explosion that occurs as a result of the primary dust explosion. The primary explosion typically releases a shockwave and fire that can disperse more combustible dust into the air, creating a secondary explosion that can be even more powerful and destructive than the initial explosion.
Secondary dust explosions are particularly dangerous because they can occur when personnel are responding to the primary explosion and can also cause further damage to equipment and structures. They can also be more difficult to control, as the initial explosion may have damaged or compromised any explosion protection systems that were in place.
To prevent secondary dust explosions, it is important to take measures to control and contain the primary explosion, such as isolating the affected area, using explosion suppression systems, and implementing emergency response plans. Additionally, it is crucial to prevent the accumulation of combustible dust in the first place, and to implement appropriate safety measures to minimize the risk of primary dust explosions.
Preventing a dust explosion requires a combination of engineering controls, administrative controls, and employee training. Here are some key measures that can be taken to prevent a dust explosion:
- Control dust generation: Implement engineering controls, such as dust collection and ventilation systems, to minimize the generation of combustible dust.
- Minimize dust accumulation: Use administrative controls, such as regular cleaning and maintenance, to prevent the accumulation of combustible dust in work areas and equipment.
- Eliminate ignition sources: Use engineering controls, such as grounding and bonding equipment, to eliminate ignition sources, such as static electricity.
- Implement explosion protection systems: Install explosion protection systems, such as explosion vents, suppression systems, and isolation systems, to reduce the risk of explosions and minimize their effects.
- Train employees: Train employees on the hazards of combustible dust and the appropriate safety measures to prevent dust explosions.
- Conduct regular inspections and audits: Conduct regular inspections and audits of the workplace to ensure that all safety measures are in place and functioning effectively.
By implementing these measures, you can significantly reduce the risk of a dust explosion and ensure the safety of workers and equipment. It is important to work with safety professionals and follow all relevant regulations and guidelines to ensure the best possible protection against dust explosions.
The National Fire Protection Association (NFPA) provides guidelines and recommendations for preventing dust explosions through its NFPA 652 Standard on the Fundamentals of Combustible Dust.
Some key recommendations from the NFPA 652 include:
- Hazard assessment: Conduct a thorough hazard assessment to identify and evaluate the risks of combustible dust in the workplace.
- Dust management: Implement a comprehensive dust management program to minimize the accumulation of combustible dust, including regular cleaning and maintenance, effective dust collection and ventilation systems, and proper handling and storage of materials.
- Ignition control: Implement measures to control ignition sources, such as static electricity, hot surfaces, and electrical equipment.
- Explosion protection: Install and maintain appropriate explosion protection systems, such as explosion vents, suppression systems, and isolation systems.
- Employee training: Provide comprehensive training to employees on the hazards of combustible dust and the appropriate safety measures to prevent dust explosions.
- Management of change: Implement a management of change program to ensure that changes in equipment, materials, or processes do not create new or increased hazards.
- Emergency planning: Develop and implement an emergency plan that includes procedures for responding to dust explosions, including evacuation, fire suppression, and medical treatment.
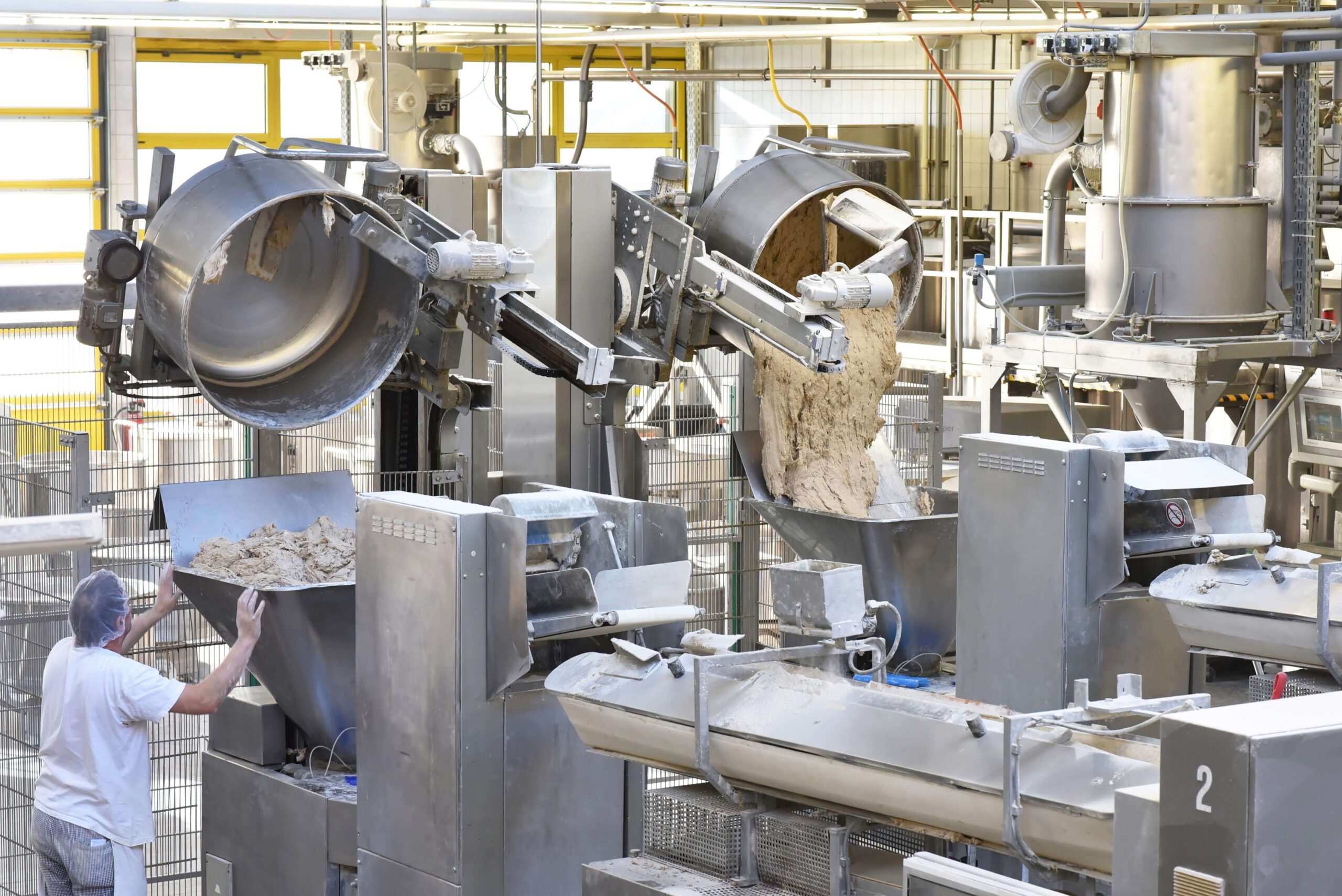
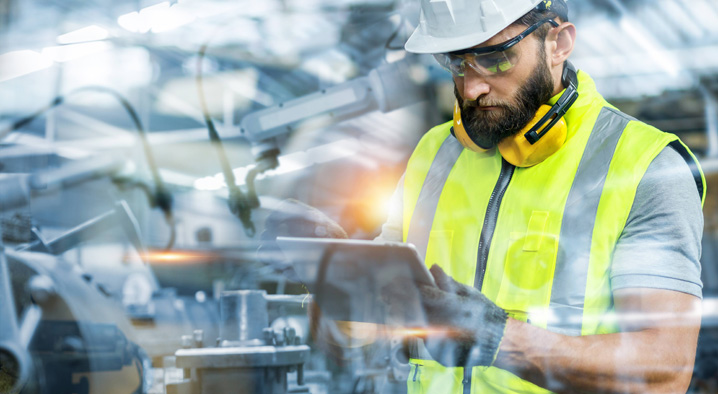
To determine if your facility is at risk of a dust explosion, you should consider the following factors:
- Dust Generation: Evaluate the processes and materials in your facility that have the potential to generate combustible dust. Common sources include grinding, cutting, sanding, pulverizing, and handling powdered substances.
- Dust Accumulation: Assess whether combustible dust is accumulating in your facility. Dust can settle on surfaces, equipment, and ventilation systems. Accumulated dust increases the risk of an explosion as it provides fuel for combustion.
- Dust Concentration: Determine if there is a high concentration of combustible dust in the air. Dust particles become more hazardous when they are finely divided and dispersed in the atmosphere. High dust concentrations increase the likelihood of a dust explosion.
- Ignition Sources: Identify potential ignition sources in your facility. These can include open flames, sparks from electrical equipment, hot surfaces, welding operations, static electricity, and even spontaneous combustion. It’s essential to prevent these sources from coming into contact with combustible dust.
- Ventilation and Containment: Evaluate the effectiveness of your facility’s ventilation systems. Proper ventilation helps control dust accumulation and disperses any potential dust clouds, reducing the risk of an explosion. Similarly, ensure that equipment and processes are appropriately enclosed to contain dust and prevent its dispersion.
- Safety Measures: Review the safety measures in place at your facility. This includes implementing proper housekeeping practices, regular equipment maintenance, grounding and bonding procedures, use of explosion-proof electrical systems, and employee training on dust explosion hazards and prevention.
- Industry Standards: Familiarize yourself with applicable industry standards and guidelines, such as those provided by the Occupational Safety and Health Administration (OSHA) or other regulatory bodies. These resources offer specific recommendations for assessing and mitigating the risk of dust explosions in various industries.
If you suspect that your facility may be at risk of a dust explosion, it is crucial to consult with safety professionals or experts in industrial hygiene to conduct a thorough hazard assessment. They can help identify potential risks, suggest appropriate preventive measures, and ensure compliance with relevant safety regulations.
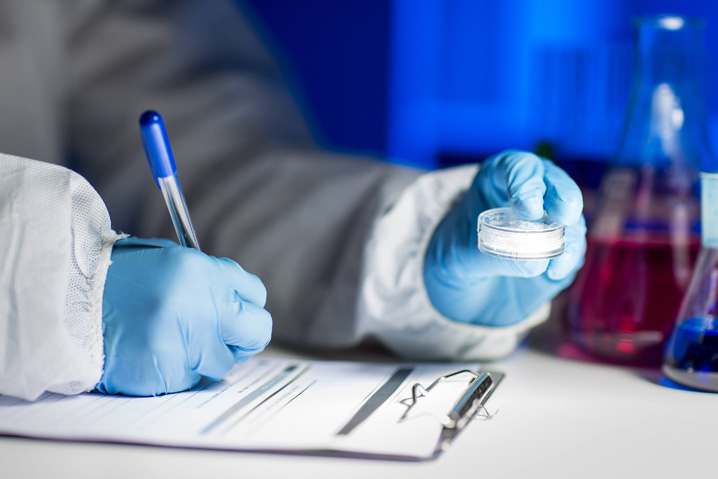
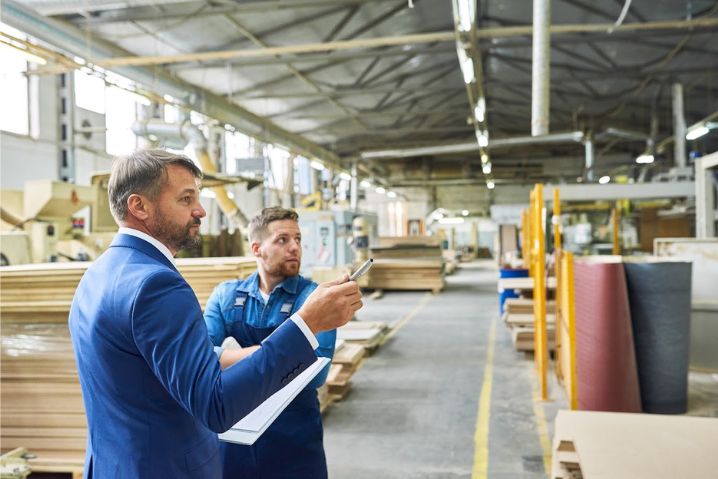
Addressing NFPA 652 Standard Regarding Combustible Dusts
Do you operate a facility that requires you to engage with substances that are dusty or powdery in n
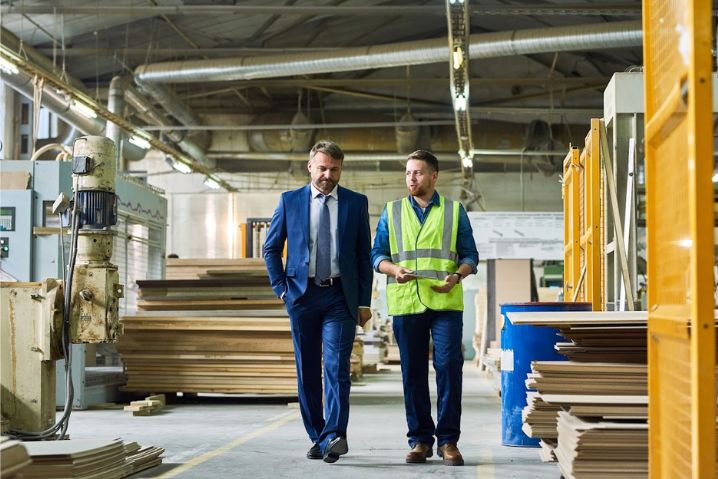
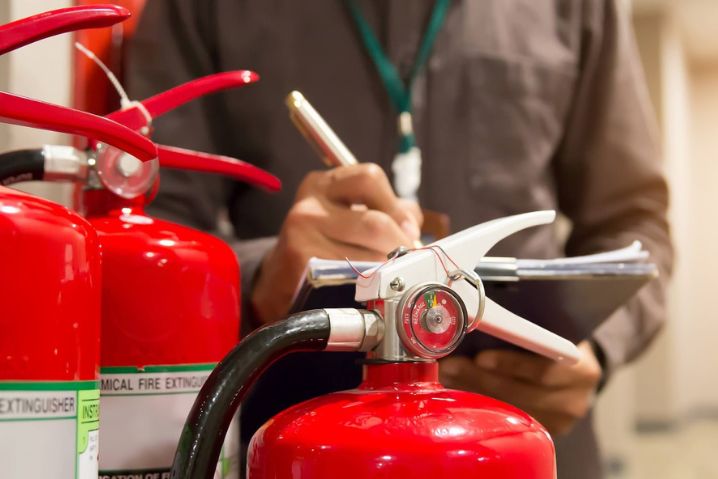
6 Industries Added by OSHA to the Combustible Dust NEP Program
n late January 2023, a new version of the Combustible Dust National Emphasis was issued by the Occup
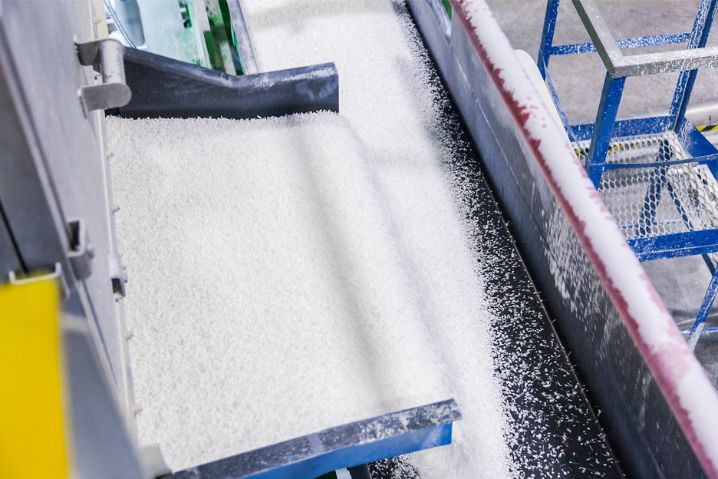
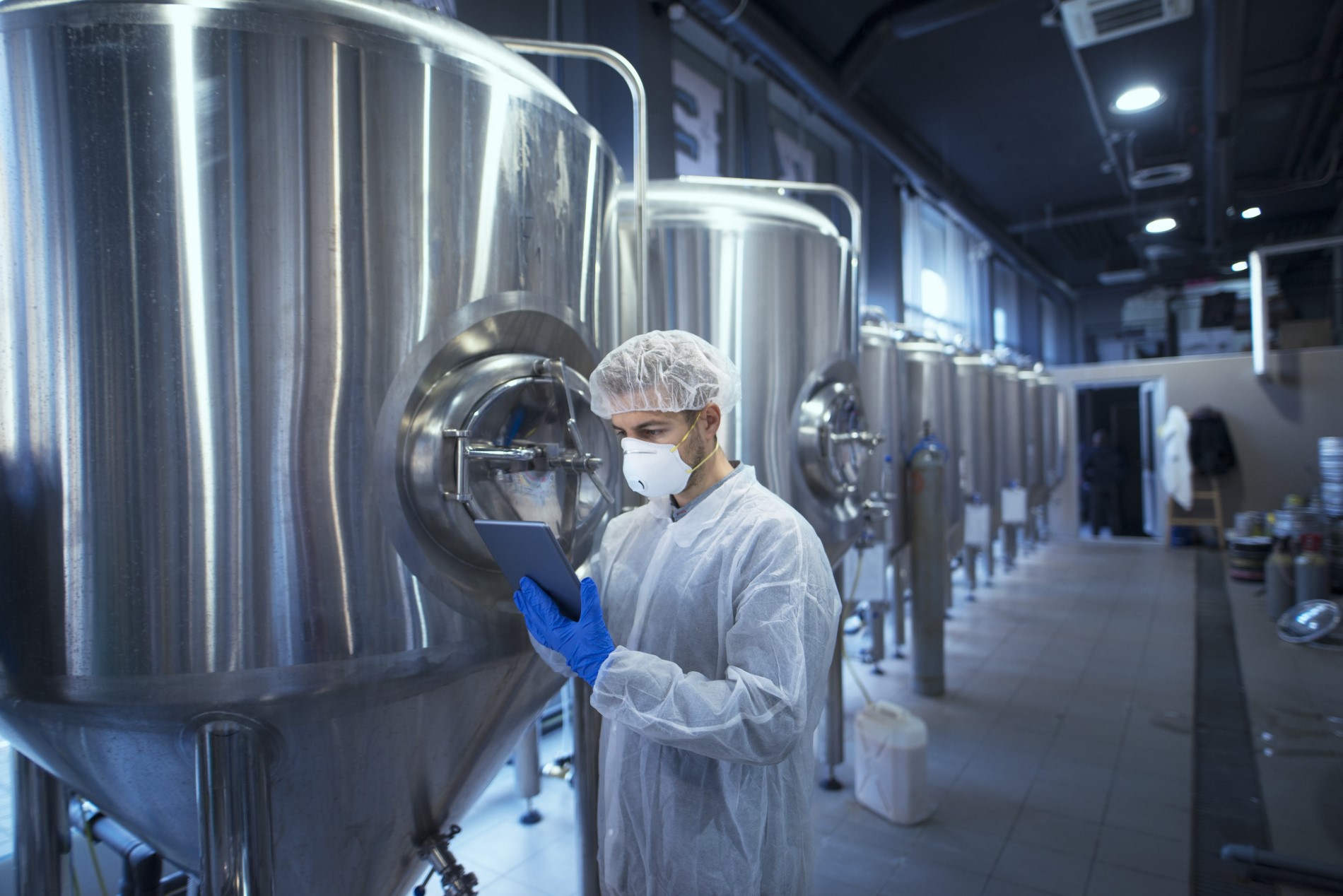
Ensuring the Safety of Facility Through Dust Explosion Test Data
“Could it be a problem if my powder has demonstrated 3mJ of minimum ignition energy and 256 bar.m/