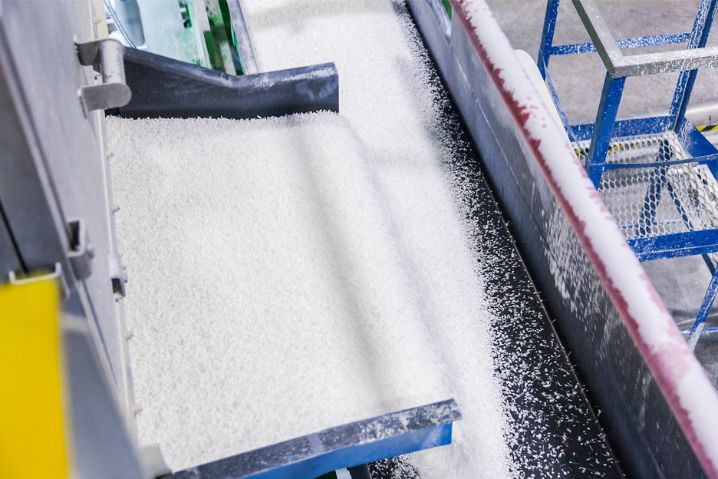
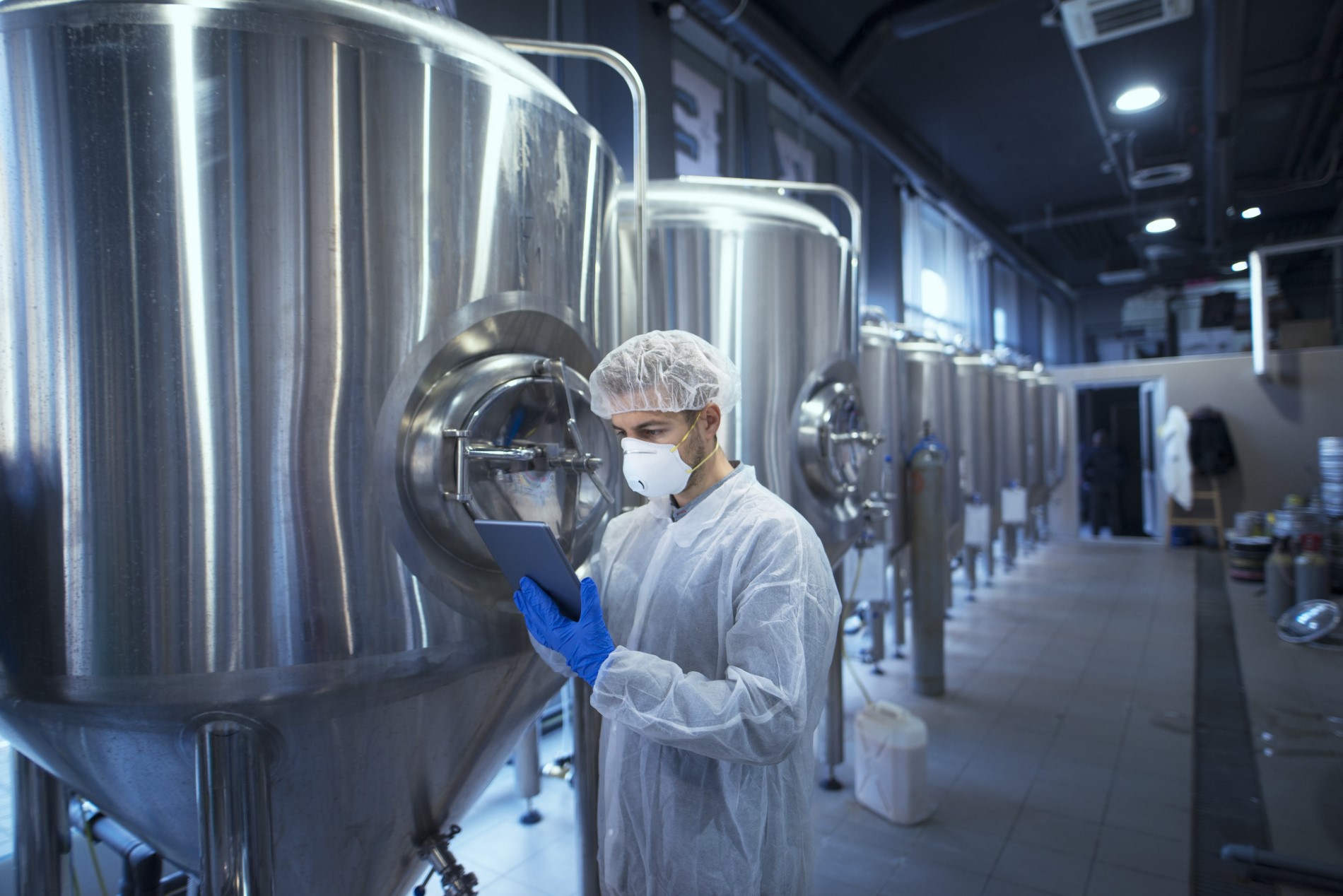
Ensuring the Safety of Facility Through Dust Explosion Test Data
“Could it be a problem if my powder has demonstrated 3mJ of minimum ignition energy and 256 bar.m/s of Kst, while its bulk powder volume resistivity is 5X1015 ohm.m”
Several companies have recently begun to measure their powders’ explosion properties and other metrics before contacting us. This raises the question of how these entities are utilizing the data. This article will help you understand and employ the data obtained through dust hazard analysis in an effective manner.
Instead of overcomplicating the subject, it is best to assess the rudimentary properties of these powders, which are crucial facets for all facilities. It is natural for powders to sometimes self-heat, burn, generate static electric forces, and even explode. It is crucial to embark on this journey by exploring the issue of explosions.
Explosions
It is common knowledge that a powder dispersed in the air can cause an explosion or a flash fire, provided there is a source of ignition. The presence of the dispersed powder within a building or process equipment may lead to explosions. While the process of combustion causing flash fires is the same, containment is not an issue in this case. In this context, it is necessary to understand the potential magnitude of an explosion that your powder can cause and its readiness to ignite. It is also crucial to determine the best practices to safeguard your facility in case of a dust explosion and the preventative methods that must be implemented. Dust explosion tests provide answers to these questions.
In a laboratory, a 20-l spherical test vessel is used to determine the explosion strength by computing the maximum explosion pressure (Pmax) as well as the ‘normalized’ maximum rate of pressure rise (Kst value). There is a positive correlation between the explosion impact and the Kst and Pmax values. Although these metrics can be employed in many ways, we typically leverage them by devising protective measures for various facilities. Design activation pressure and explosion relief vent size are just two of the many measures that can be designed using these metrics.
Various tests conducted to determine the preventative measures for explosions can be used to measure the ease of ignition according to different sources of ignition. In order to determine the smallest spark energy that could cause the ignition of a powder, the MIE test measures are employed. This test is also helpful in determining the criteria for bonding or grounding and the importance of wearing footwear that is static-dissipative when performing operator duties. In a few cases, it also helps emphasize the importance of prohibiting the utilization of materials with insulating properties.
Auto-ignition. In heated settings, powders may occasionally ‘auto-ignite’ to transform into cloud forms. In order to determine and implement process temperatures that are safe, it is crucial to know the dust cloud’s (MIT-cloud) minimum ignition temperature.
There are a few more ignition tests that can be employed, a few of which are outlined below.
Self-Heating
In case of temperatures exceeding the on-set temperature for self-heating, several powders may get ignited automatically (self-ignition). Sometimes, such incidents of self-heating can cause explosions or fire, particularly during operations involving powder drying. To prevent such incidents, it is important to characterize the powders accurately, as it helps determine the safe temperatures for drying and processing. A specialist can help determine what tests are most appropriate for self-heating since it is a complex topic. A complete comprehension of the self-heating characteristics of powders may only be possible through several tests, including the UN self-heating N4 test and the Grewer oven test. The temperature at which a product is safely dried as well as stored depends on a number of factors, including the availability of air, the amount of powder, the thickness of the deposit, and others.
Powders may also self-heat because of the electrical equipment developing hot surfaces, resulting in a fire. To determine the ideal specifications for equipment within your facility, we recommend an additional powder Hot Plate test – MIT-layer – employed in tandem with the aforementioned MIT-cloud test.
Static Electricity
Moving any powder can lead to the generation of static electricity. In powders that demonstrate a high electrical resistivity, the static charge is retained and accumulated, even in instances where the handling is carried out in meta equipment that is bonded and grounded. Occasionally, the build-up of this charge could cause a powder cloud explosion. To identify and compute these hazards and determine ideal precautionary measures, the powder can be tested for electrostatic chargeability, minimum ignition energy, as well as bulk powder volume resistivity.
Fire
An explosion of a powder in the presence of air may lead it to burn in the form of a layer. There is a distinction between powder layer combustion and dust cloud explosion based on the amount of material surface that can combust at a time. To determine the way in which a powder may burn as a layer, companies can conduct a burning rate or fire-train test. It is wise to determine if the bulk combustion of a powder would cause it to merely smolder and gradually extinguish itself, or burn at a quick pace and cause a fire without providing adequate time to react.
Conclusions
It is now possible to determine whether the powder discussed at the beginning of the article is dangerously combustible. According to the metrics, it is highly explosible and the explosion relief vents installed in the facility must be very big. The powder is also highly sensitive to getting ignited due to electrostatic discharges and hence when it becomes charged in this manner, the charge is retained for over one day. Several precautionary measures, including placing them in plastic bags or boxes should be considered.
In order to protect your facility and employees, it is highly recommended that you leverage the data obtained regarding process safety efficiently.
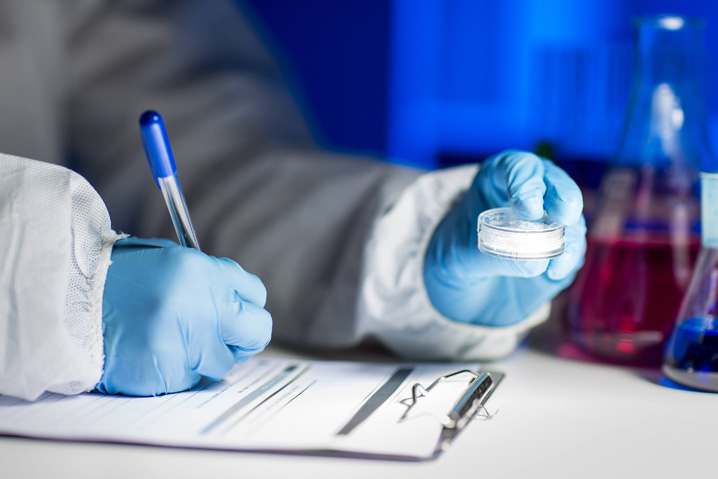
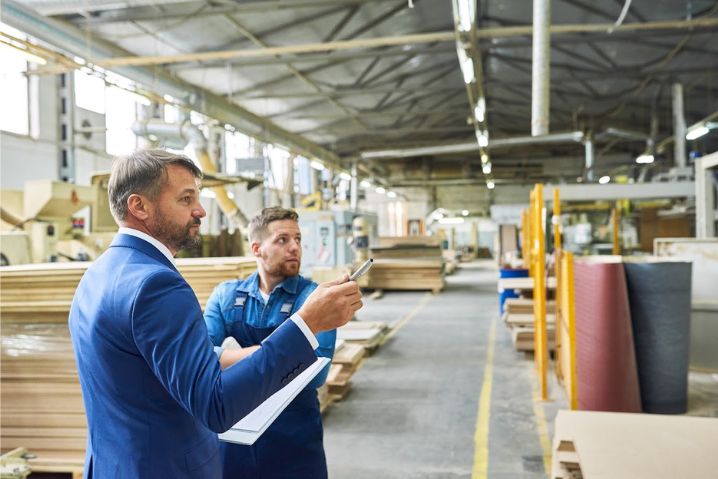
Addressing NFPA 652 Standard Regarding Combustible Dusts
Do you operate a facility that requires you to engage with substances that are dusty or powdery in n
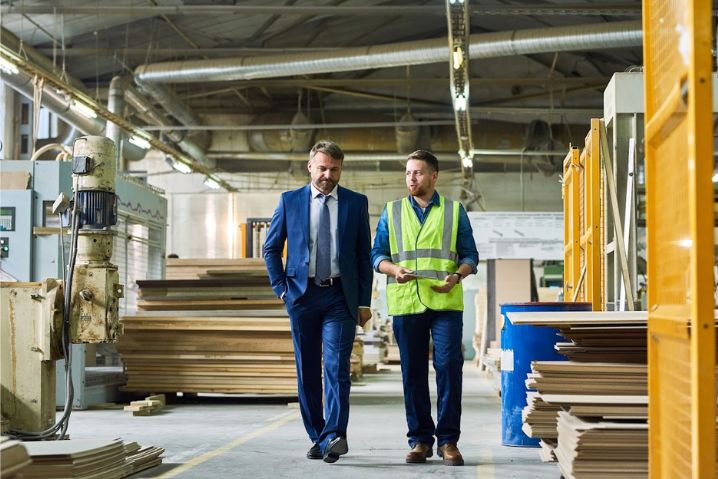
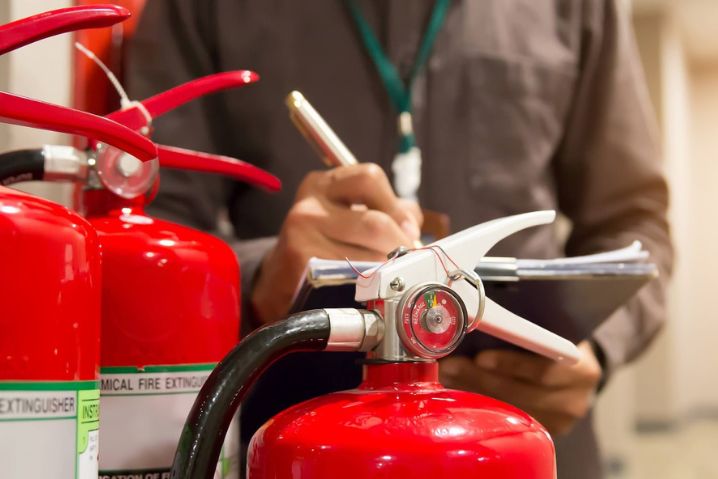
6 Industries Added by OSHA to the Combustible Dust NEP Program
n late January 2023, a new version of the Combustible Dust National Emphasis was issued by the Occup
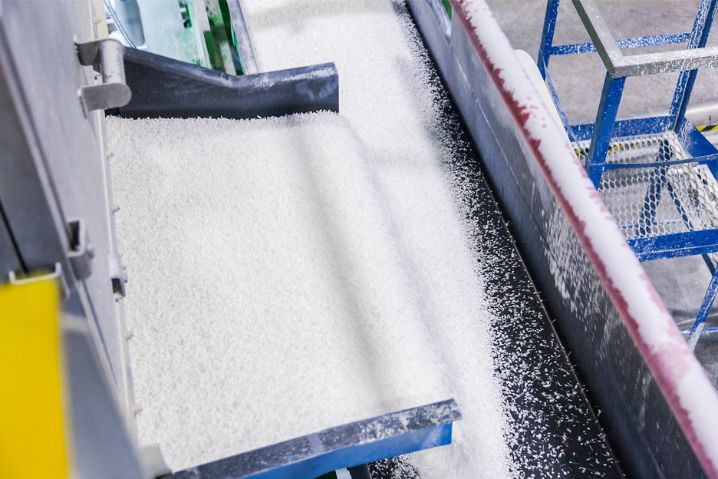
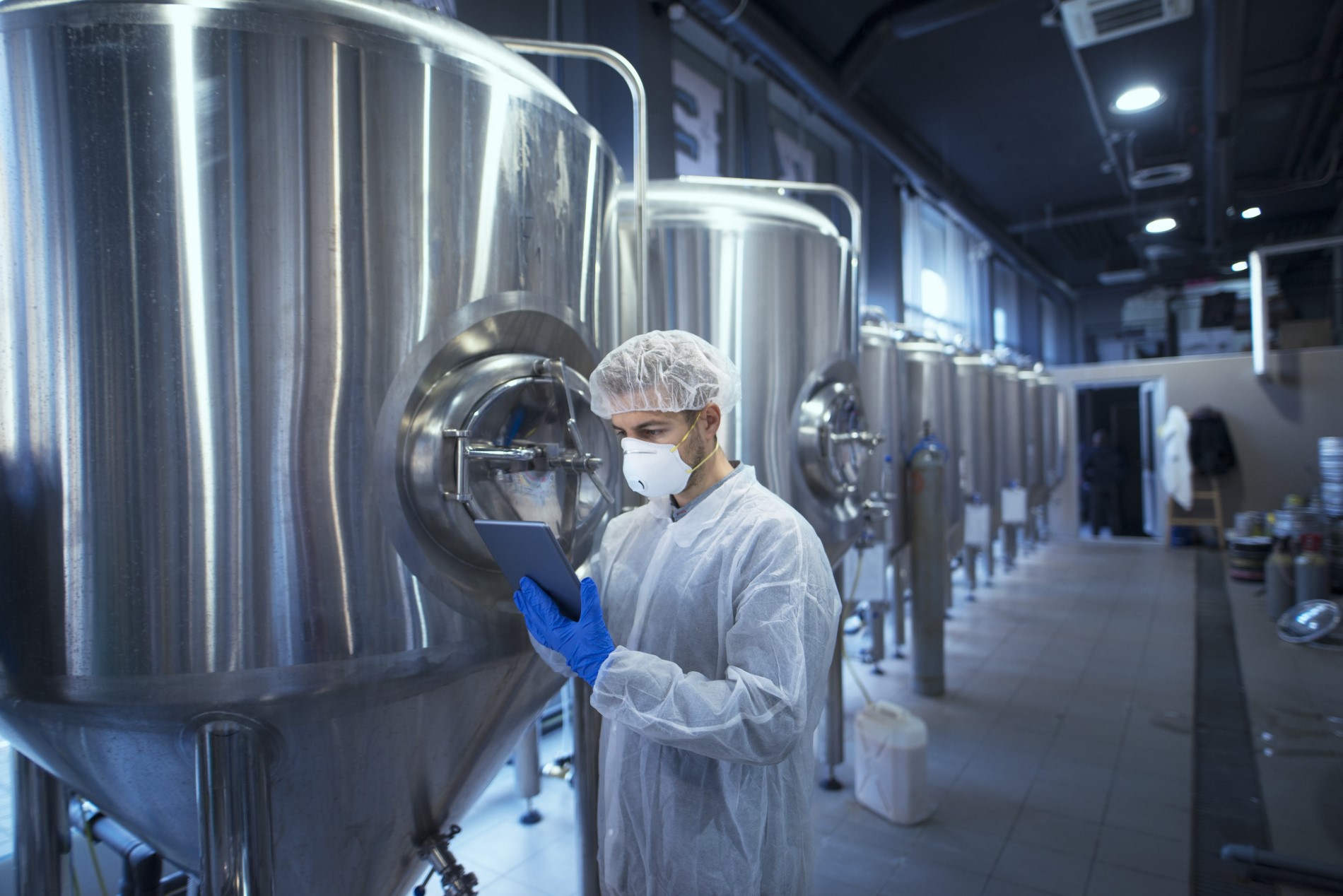
Ensuring the Safety of Facility Through Dust Explosion Test Data
“Could it be a problem if my powder has demonstrated 3mJ of minimum ignition energy and 256 bar.m/