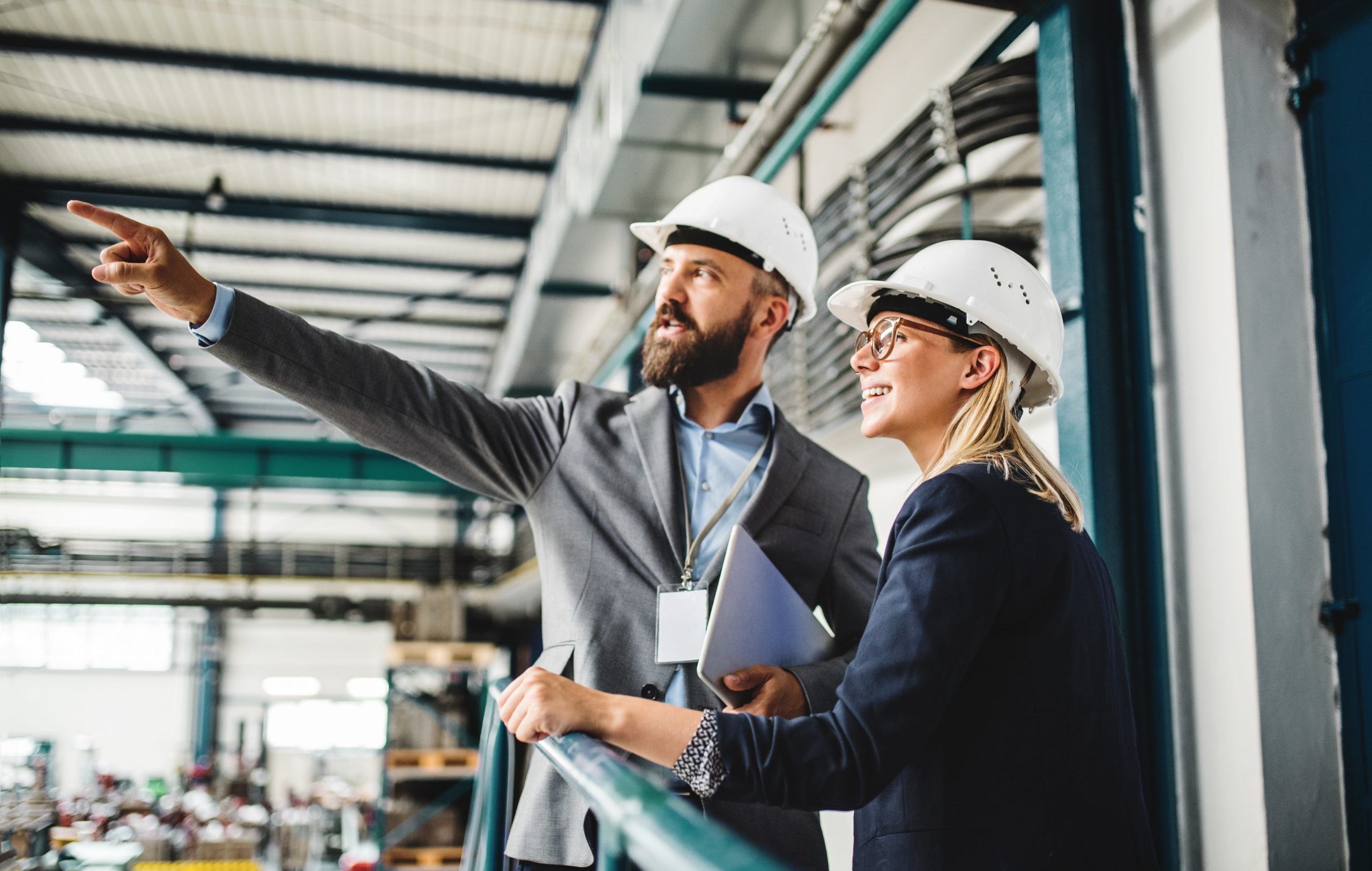
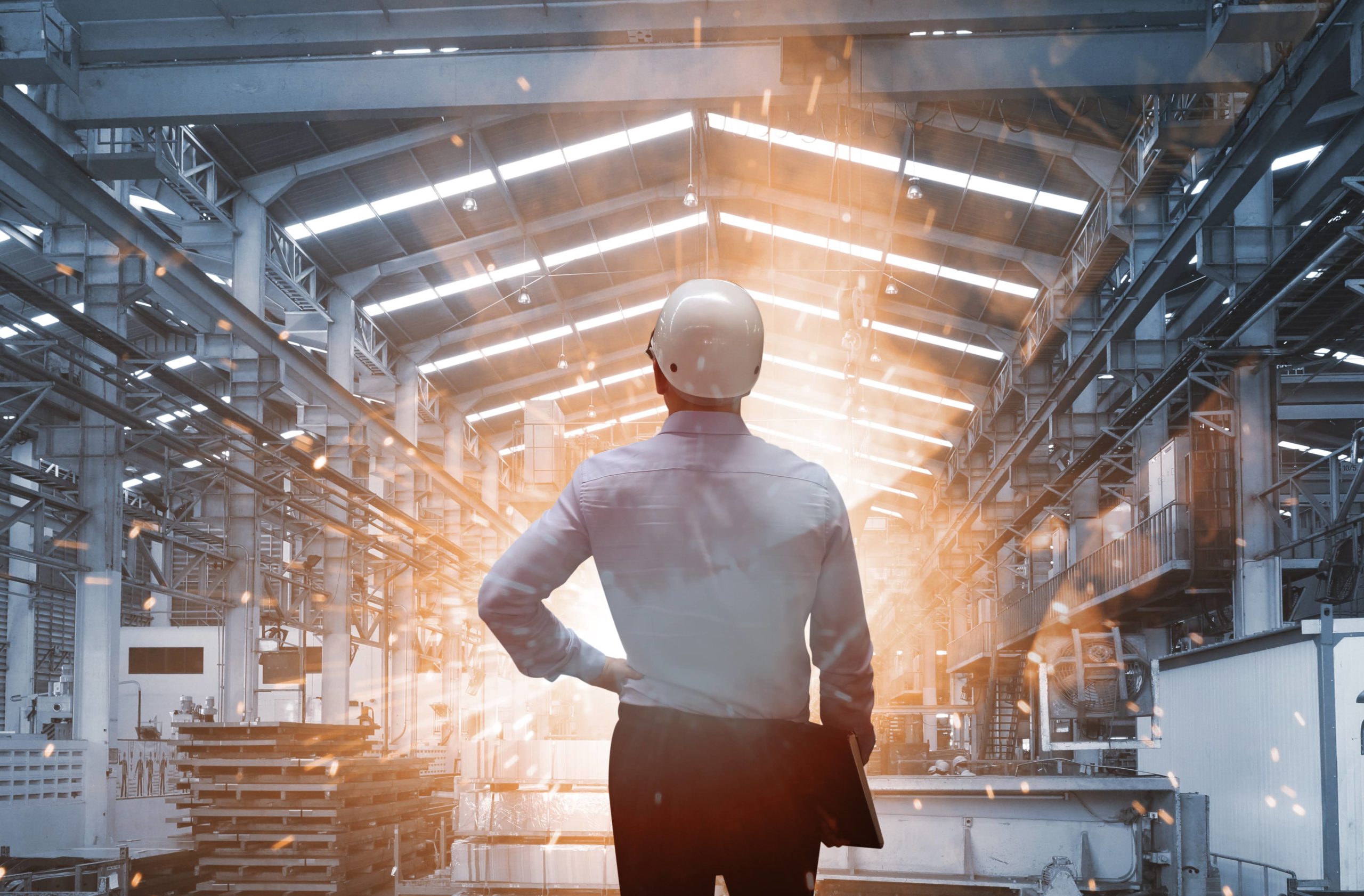
Hazardous Area Cleanup: Ensuring Safety and Minimizing Risks during Hazardous Material Remediation
Hazardous area classification (HAC), also known as electrical classification, is a crucial process used to identify and assess areas where the presence of flammable vapors, gases, combustible dust, or fibers could potentially lead to fires or explosions. By determining the hazardous areas, proper safety measures can be implemented to minimize the risk of incidents, such as property damage, injuries, and loss of life.
Originally, HAC was primarily focused on selecting electrical equipment suitable for hazardous atmospheres, ensuring that ignition sources were prevented. However, the application of HAC has expanded to include broader risk assessments in various industries. It is now used not only in chemical plants but also in sectors such as food processing, power generation, oil and gas, pharmaceuticals, mining, and many others.
Regulatory bodies and organizations worldwide recognize the importance of HAC in ensuring workplace safety. In the United States, the Occupational Safety and Health Administration (OSHA) and the National Fire Protection Association (NFPA) reference HAC in their safety regulations and model consensus standards. In Europe, the ATEX (Atmosphères Explosibles) and DSEAR (Dangerous Substances and Explosive Atmospheres Regulations) directives provide guidelines for hazardous area classification.
By implementing proper HAC procedures, organizations can effectively mitigate the risks associated with flammable and explosive atmospheres, thus safeguarding employees, facilities, and the surrounding environment.
When is an area considered hazardous?
A hazardous area for combustible dust is an area where the presence of combustible dust particles in the air can create a potential fire or explosion hazard. Combustible dust refers to fine particles or dust that can ignite and propagate a fire or explosion when exposed to an ignition source, such as sparks, open flames, or electrical equipment.
When assessing an area for combustible dust hazards, several factors are taken into consideration:
- Presence of combustible dust: The first step is to determine whether there is a presence of combustible dust in the area. This could include various materials such as metals (e.g., aluminum, magnesium), wood, coal, plastics, pharmaceutical powders, food products (e.g., flour, sugar), and many others.
- Dust particle size: The size of dust particles is important as it influences their ability to become airborne and remain suspended in the air. Fine particles with smaller sizes are more likely to form explosive dust clouds compared to larger particles.
- Dust concentration: The concentration or accumulation of combustible dust in the area is another critical factor. High concentrations of dust increase the likelihood of a fire or explosion if an ignition source is present.
- Dispersion and suspension: The potential for dust dispersion and suspension in the air is assessed. Processes or activities that generate dust, such as material handling, grinding, cutting, or conveying, need to be evaluated to determine if they create hazardous conditions.
- Ignition sources: Identifying potential ignition sources within the area is essential. Ignition sources can include open flames, sparks from electrical equipment, hot surfaces, welding operations, or static electricity.
Based on these factors, hazardous areas for combustible dust are classified into zones to indicate the level of risk. The zones are typically classified as Zone 20, Zone 21, and Zone 22, following the European classification system.
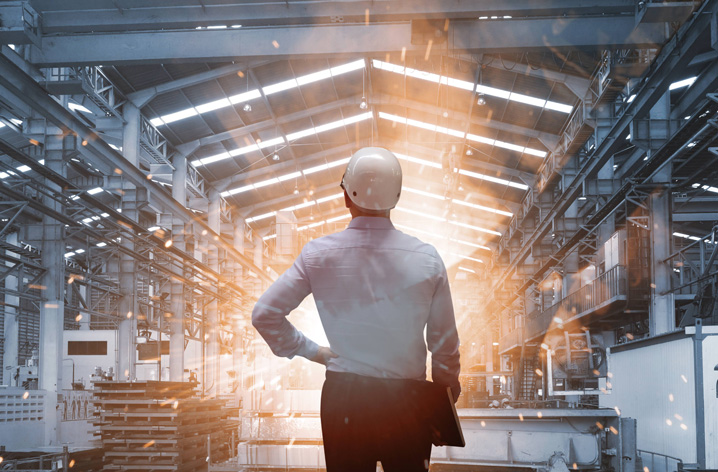
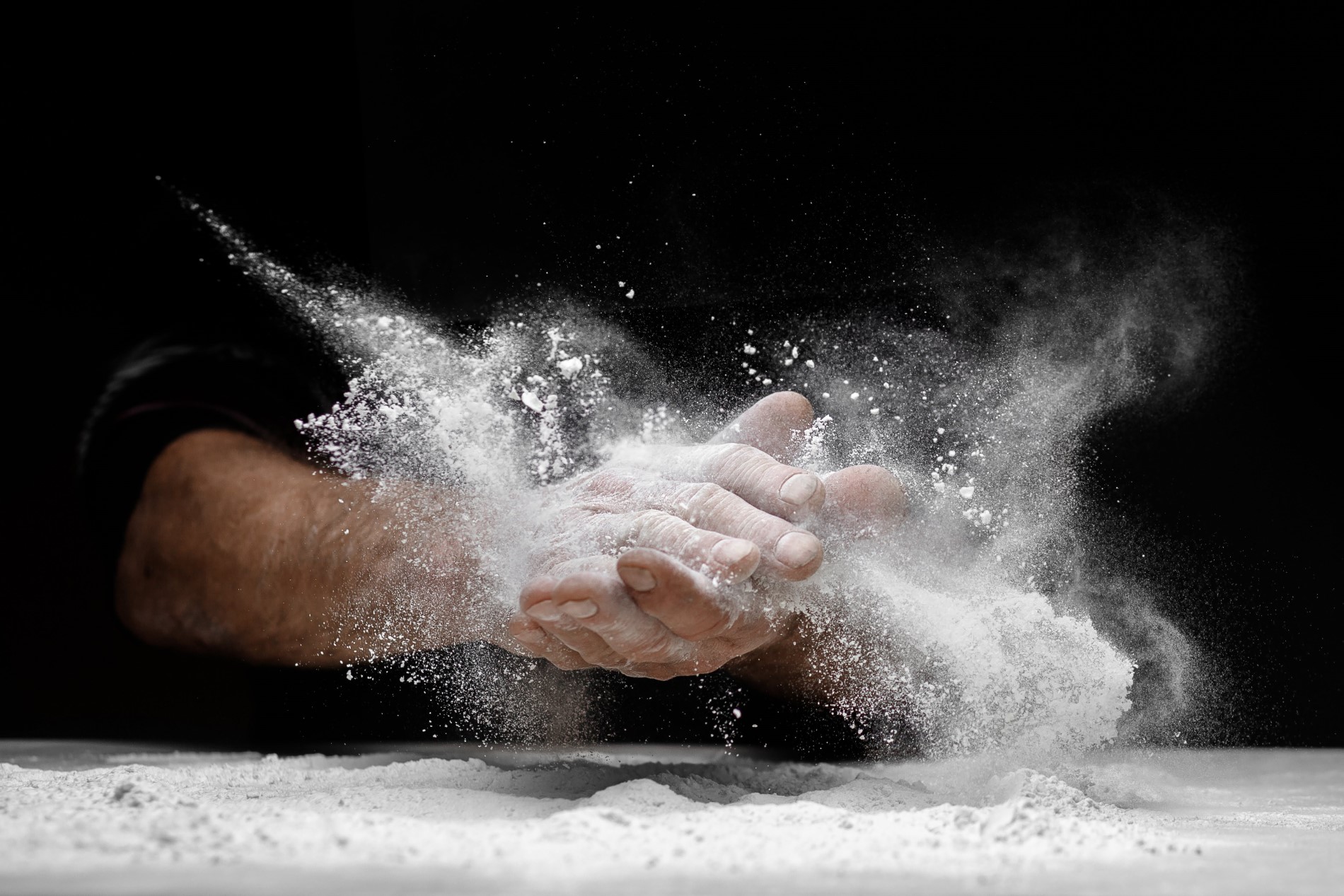
Hazardous Zone Classification:
The zones used in hazardous area classification for combustible dust are categorized based on the likelihood and duration of the presence of combustible dust. The zone classification system provides guidance on the level of risk and assists in determining appropriate safety measures. Here are the three main zones:
- Zone 20: In Zone 20, the presence of combustible dust is continuously or for long periods. This zone is characterized by the highest risk level. It typically applies to areas where combustible dust is present in sufficient quantities to form explosive dust clouds or layers continuously or frequently. Examples of Zone 20 areas include the inside of a dust collector, a pulverized coal storage silo, or a milling operation with high dust generation.
- Zone 21: Zone 21 covers areas where combustible dust is likely to occur during normal operations. Although the dust may not be continuously present, it is expected to be present intermittently or periodically. This zone is relevant to areas where dust release can occur due to process activities, such as material handling or occasional spillage. Examples include the interior of equipment like mixers, grinders, or bucket elevators.
- Zone 22: Zone 22 includes areas where combustible dust is not likely to occur in normal operations but may be present infrequently or for short durations. Dust accumulation in this zone is expected to be minimal or occur only under abnormal conditions, such as equipment breakdown, maintenance activities, or unusual events. Examples include the exterior surfaces of equipment or floors in the vicinity of process operations.
It’s important to note that these zone classifications may differ slightly depending on the specific standards or regulations followed in different regions. For example, in North America, the National Electrical Code (NEC) uses Class II, Division 1 and Division 2 classifications for combustible dust areas.
Proper hazardous area classification for combustible dust is crucial for implementing appropriate preventive measures, such as proper ventilation, dust control systems, explosion protection equipment, and safe work practices, to minimize the risk of fires and explosions. It is important to adhere to relevant safety standards and guidelines, such as those provided by organizations like NFPA (National Fire Protection Association) and OSHA (Occupational Safety and Health Administration).
How to Properly Clean and Maintain a Hazardous Zone
Cleaning up a hazardous area requires careful planning and adherence to proper safety procedures to minimize the risk of exposure and potential incidents. The specific cleanup process will depend on the nature of the hazardous materials or substances present. Here are some general steps to consider when cleaning up a hazardous area:
- Assess the situation: Before initiating cleanup, assess the nature and extent of the hazard. Determine the type of hazardous material present, its potential risks, and the appropriate cleanup procedures to follow. Refer to safety data sheets (SDS) or other relevant resources for guidance.
- Ensure personal protective equipment (PPE): Before entering the hazardous area, ensure that all personnel involved are equipped with appropriate personal protective equipment. This may include gloves, safety goggles, respirators, coveralls, or other specialized equipment based on the specific hazards involved.
- Isolate and secure the area: Restrict access to the hazardous area by posting warning signs or using barriers to prevent unauthorized personnel from entering. Ensure that the area is secure and that all necessary precautions have been taken to minimize risks to workers and the surrounding environment.
- Contain and control the hazard: If possible, contain the hazardous material to prevent its spread or further contamination. For example, if dealing with a liquid spill, use absorbent materials or barriers to contain the spill and prevent it from spreading to unaffected areas.
- Follow proper cleanup procedures: Cleanup methods will vary depending on the specific hazard, but some general principles include:
- Follow any specific cleanup procedures outlined in safety guidelines or regulations.
- Use appropriate cleaning agents or absorbents recommended for the particular hazard.
- Ensure proper ventilation in the area to minimize exposure to hazardous fumes or vapors.
- Use tools and equipment suitable for the cleanup task to avoid generating sparks or other ignition sources.
- Dispose of hazardous materials according to local regulations and guidelines.
- Decontamination and waste disposal: After the cleanup, decontaminate surfaces, tools, and equipment used during the process. Follow proper decontamination procedures to ensure that residual hazardous substances are effectively removed. Dispose of contaminated materials or waste according to applicable regulations, considering their proper segregation, containment, and disposal methods.
- Post-cleanup assessment: Once the cleanup is complete, assess the area to verify that the hazardous material has been effectively removed and that the area is safe for re-entry. Conduct air monitoring or sampling if necessary to ensure that airborne contaminants are within acceptable limits.
It’s important to note that the specific cleanup procedures and requirements can vary significantly depending on the type of hazard involved. It is recommended to consult with experts, such as hazardous materials specialists or environmental health and safety professionals, to develop a tailored cleanup plan based on the specific hazard and regulatory requirements in your region.
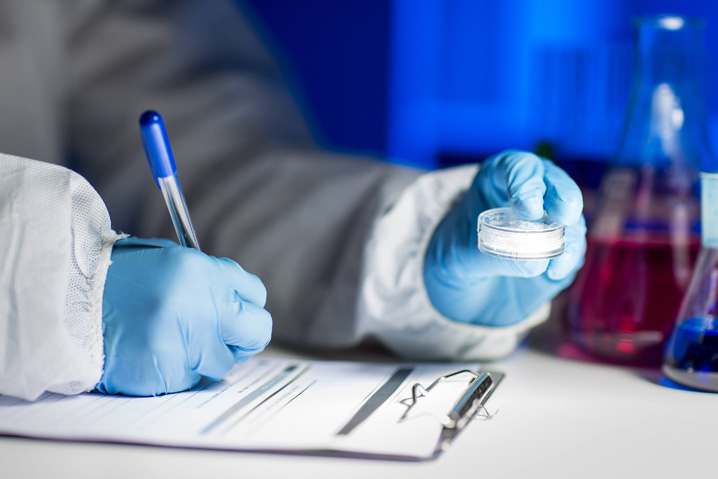
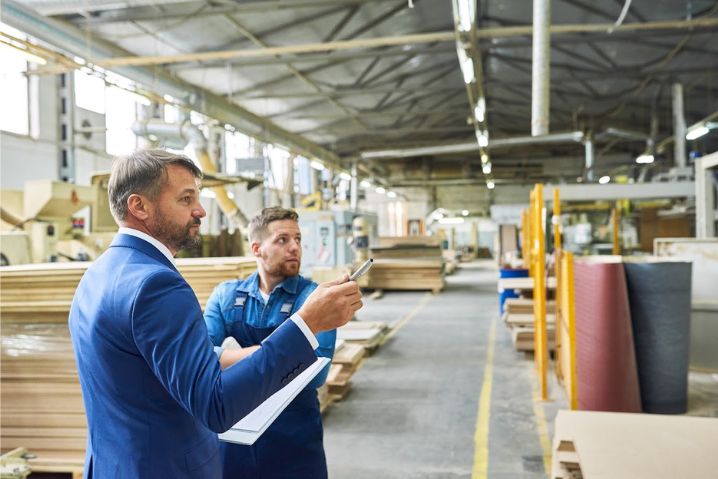
Addressing NFPA 652 Standard Regarding Combustible Dusts
Do you operate a facility that requires you to engage with substances that are dusty or powdery in n
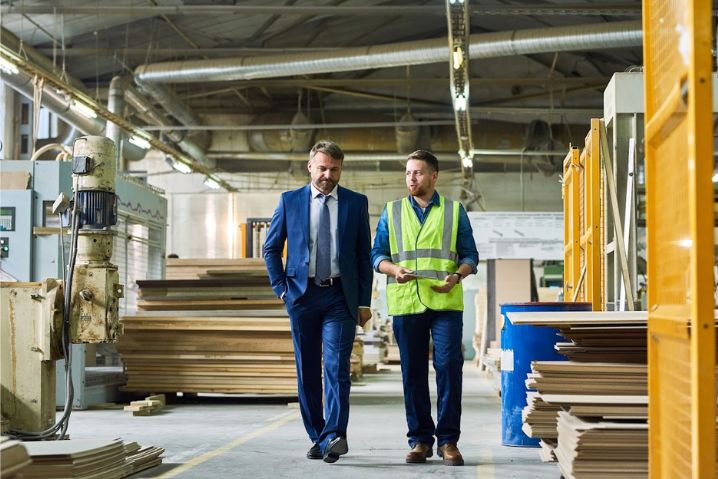
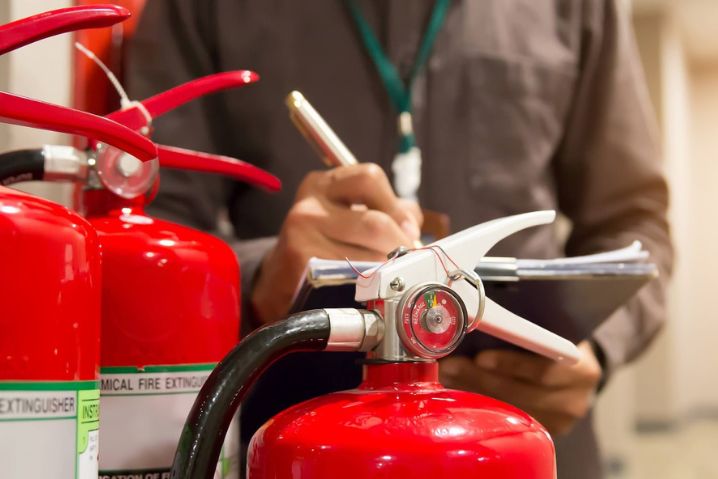
6 Industries Added by OSHA to the Combustible Dust NEP Program
n late January 2023, a new version of the Combustible Dust National Emphasis was issued by the Occup
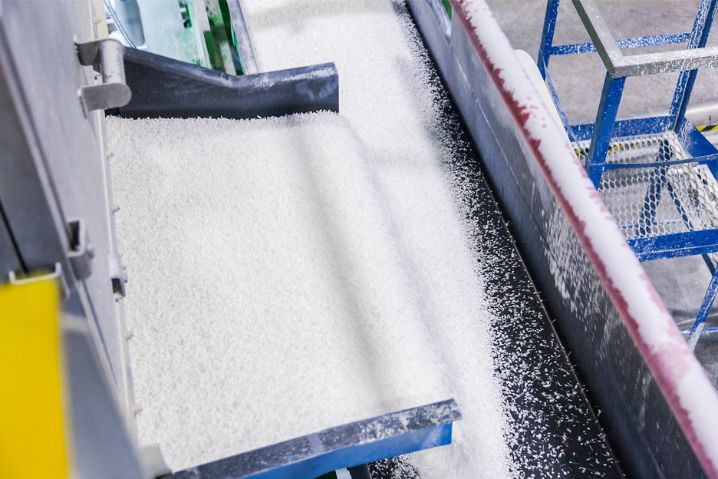
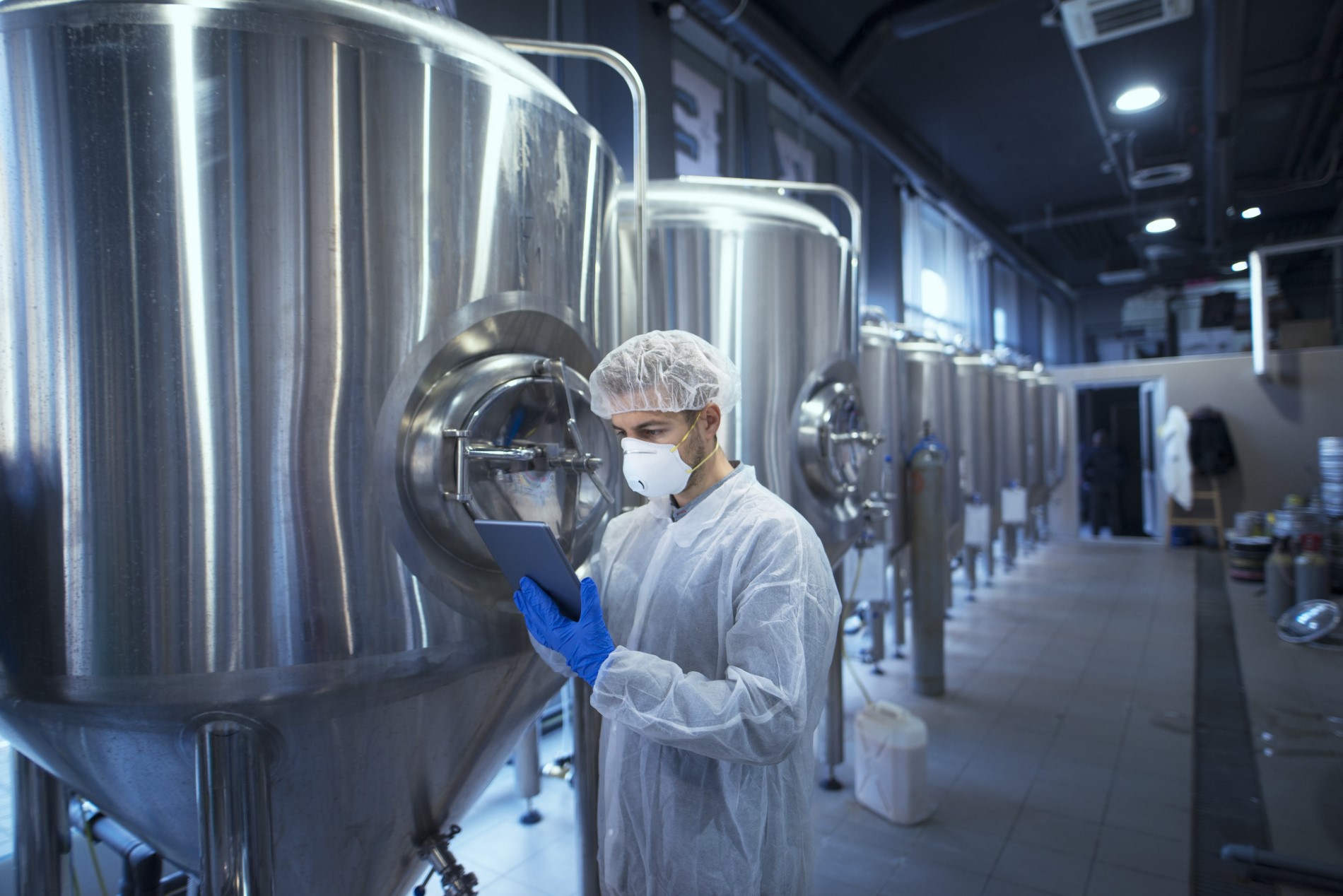
Ensuring the Safety of Facility Through Dust Explosion Test Data
“Could it be a problem if my powder has demonstrated 3mJ of minimum ignition energy and 256 bar.m/