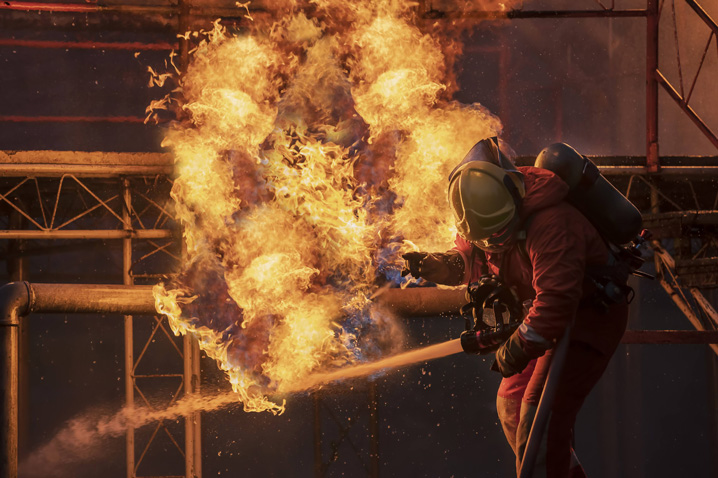
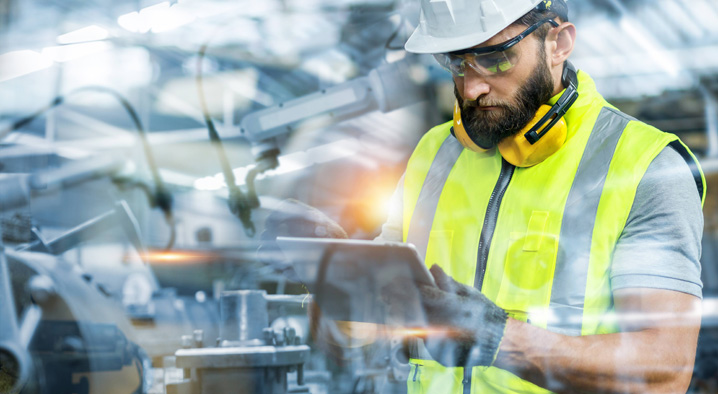
Preventative Maintenance to Reduce Electrical Classification & Housekeeping
A Case Study
During a recent Dust Hazard Analysis (DHA) walkthrough, our consultants were on the scene of a major cheese and dairy producer whose sites in the United States, consist of liquid milk products processing, spray drying of powdered milk products, and production of cheese products.
The plant in question has been in operation for almost 15 years without a major explosion. However major fires have occurred at the facility in both the spray drying area and the lactose milling systems. Each of these fires have resulted in major interruption to production, firefighter emergency response, and evacuation of staff during the incident. No one was hurt in either of the two major fires. Site management is embarking on the first steps of their combustible dust journey in completing this dust hazard analysis.
Summary:
– A cheese and dairy producer in the United States is storing powder products from a drying operation.
– The plant has been in operation almost 15-years without a major explosion. However, major fires have occurred recently in the Spray Drying and Lactose Milling Systems.
– During a Dust Hazard Analysis (DHA) walkthrough, our consultants happened upon scenes such as these shown in the photos.
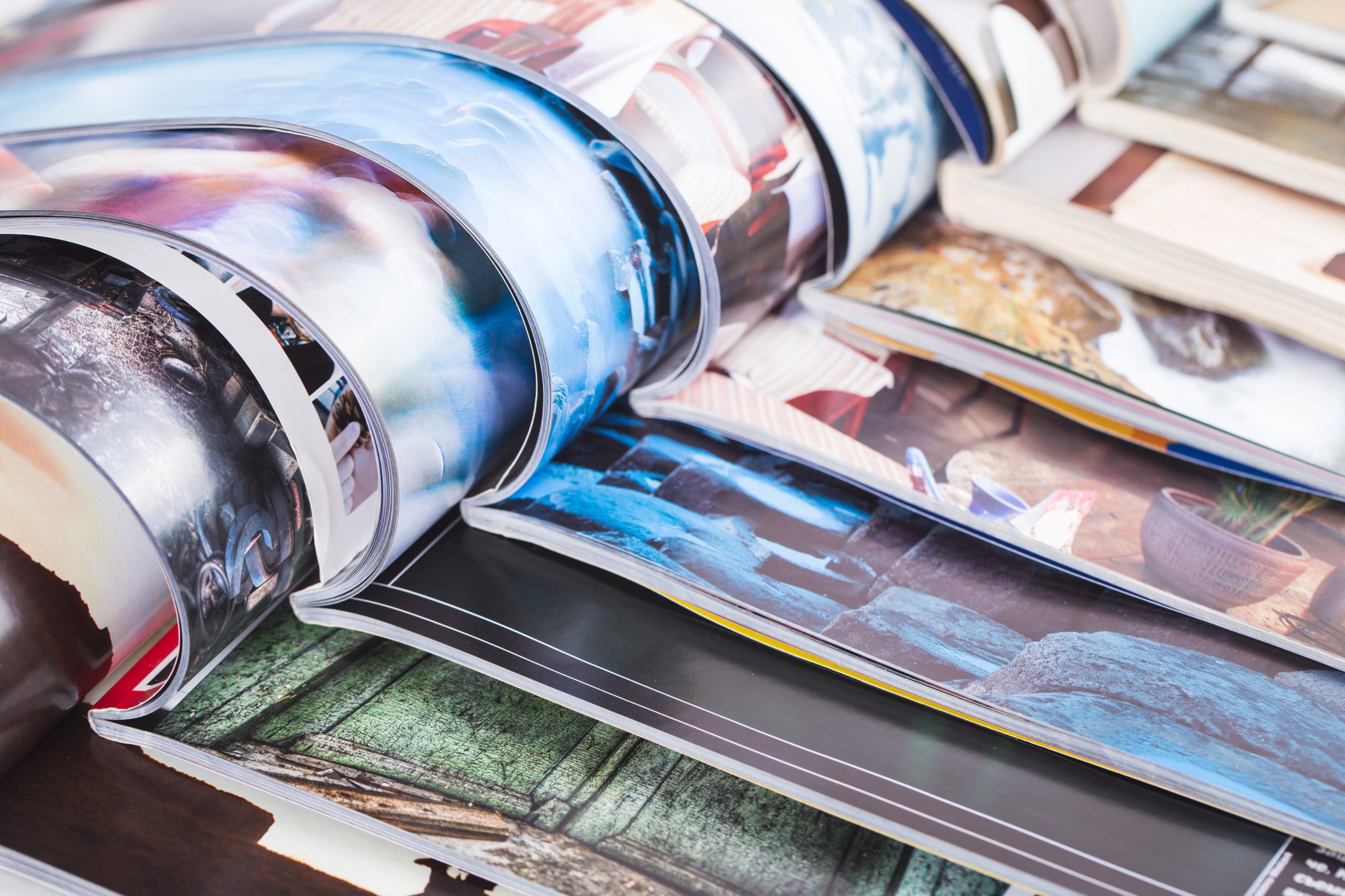
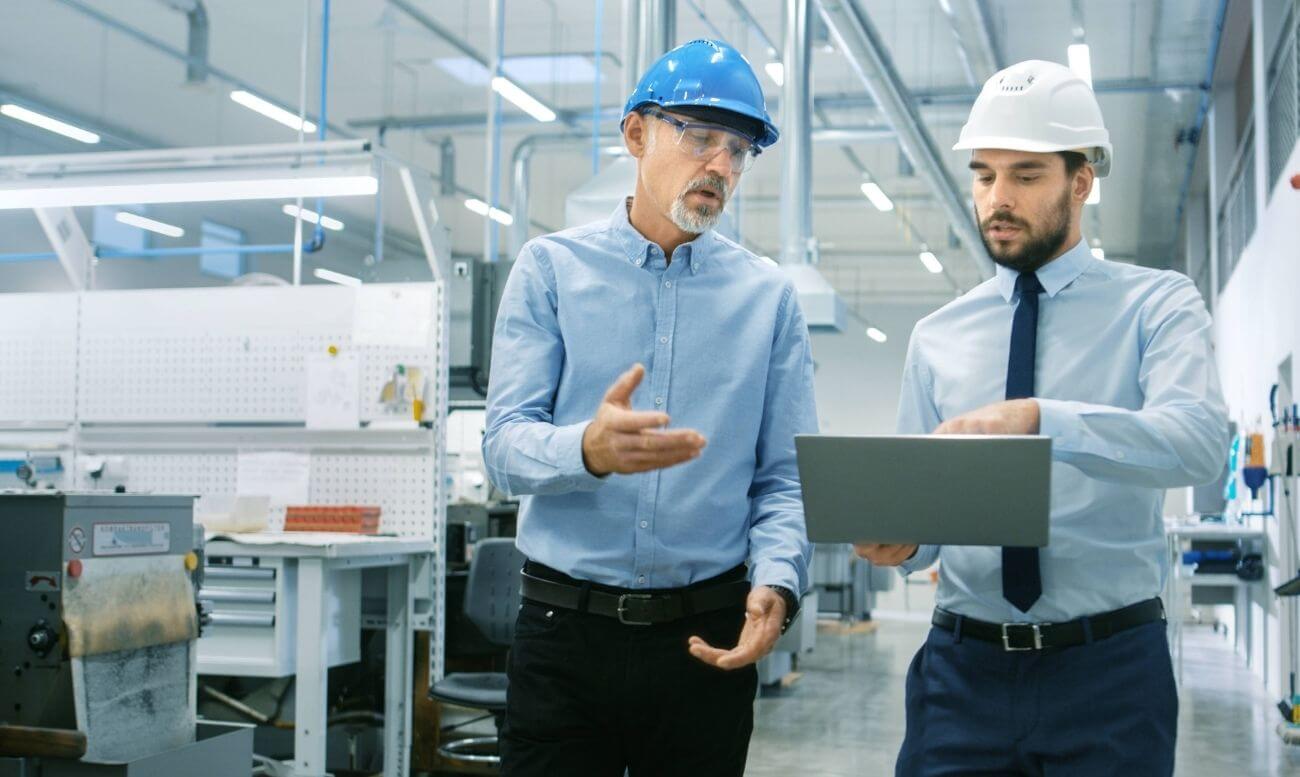
Starting Point
During the walk through, our consultants happened upon a room in which lactose and whey products are stored in large silos with equipment located on multiple grated levels. It is very normal for an operation like this to have some amount of dust buildup due to fugitive dust escape throughout the building from places such as access doors, pipe connections, and process openings. However, in this case there were several areas that exhibited very thick dust accumulations, especially on the lowest levels. It was noted that the largest layers of dust accumulation were present directly below process equipment which were fitted with flexible duct connections.
In evaluating the various dust accumulations, it was noted that there were electrical enclosures and conduit with layer thicknesses approaching 1/2 inch.
Accumulations below silos and beneath a grouping of convey piping were almost 2 inches thick! The dust emissions were so excessive, an orange tarp was secured over a blower package to prevent material from falling from above and accumulating atop the equipment.
While this system was equipped with electrical enclosures, motors, and lighting fixtures that were appropriate for the Class II division 2 Group G application (for the most part), this area far surpassed the allowable powder accumulation that would result in a Class II, Division 2 hazardous location. As a result, it should now be upgraded to Class II, Division 1, Group G due to the large amounts of dust in the area.
It’s important to note, that there is not a centralized dust collection system in this building and there are no centralized vacuum systems that can be used for the easy removal of powder from the area. On certain levels, there were portable vacuum cleaners available to operators that were properly rated for combustible dust applications. However, there are very few of these portable vacuum systems compared to the number of levels in the structure, thus requiring operators to carry these large vacuums between levels and making is difficult to effectively clean the areas.
Thickness of Dust Layer | Classification |
>3.0mm (⅛ in.) | Division 1 |
<3.0mm (⅛ in.), and surface color not discernible | Division 2 |
Surface color discernible under the dust layer | Unclassified |
Key Points:
Thick accumulations of powder are everywhere!
Some areas almost 2” thick!
Facility electrical equipment was designed for and is maintained to be suitable for Class II, Division 2, Group G meaning that enclosures are dust tight. (for the most part!)
Would you consider this to be a Class II, Div. 1 or a Class II, Div. 2 area?
No Dust collection or Centralized Vacuum System available in these areas.
The Costs
Upgrading to a Class II Division 1 Group G area was discussed as part of the DHA closeout meeting with plant management, engineering support, and the safety team.
It was immediately understood by all parties that that would be an incredibly expensive endeavor. Additionally, it was determined that even with 3rd shift “helpers” (contract employees) that are utilized in some areas of the plant to assist with housekeeping, their efforts are being undermined by the amount of dust accumulating during each day. It is estimated that if these positions could be eliminated, there would be $50,000+ /year in savings to the operating budget.
In looking at the potential cost impact to this client for the upgrade of all electrical equipment in the area, this upgrade to a Class II, Division 1 location would likely cost upwards of $1MM against their capital budget over the next 2-4 years. Such an upgrade would require that many electrical enclosures, conduit, and lighting fixtures be removed and replaced with NEMA 7/9 type enclosures and/or intrinsically safe circuits. Furthermore, there are certain pieces of equipment that would not be able to be upgraded in such a way. An example of this is the explosion suppression system that was installed on the silos to prevent a deflagration from rupturing the vessel, which is not equipped for Class II, Division 1 installation.
Lastly, the amount of dust accumulated in this area poses an enormous risk for a secondary explosion if a combustible dust cloud wherever to be ignited within this portion of the operation. The consequences from such a secondary explosion would not only cripple the operations ability to make product but would also likely result in injury or fatality.
Key Points:
– If nothing changes, costly electrical upgrades will be needed to get equipment up to Class II, Division 1, Group G
– Up to $1MM in capital expenditures
– Additional headcount is employed to help keep up with the housekeeping burden
– 2 helpers spend 3rd shift sweeping and cleaning – ongoing expense ~$50,000/yr
What is Going On Here?
During the course of our DHA walkthrough and our subsequent conversations with the client, it was determined that there are multiple reasons for the large amount of powder spillage and dust accumulation throughout the building compartment.
1. It was determined that maintenance activities such as magnet cleanouts, inspection of screw conveyors, and they need to open and unclog milling equipment were all factors in why maintenance teams were frequently required to open the process equipment and in some cases remove product from the equipment for access purposes.
2. There were flexible boots beneath each of the silos that were fluctuating between positive pressure and high vacuum which caused excess fatigue and ultimately resulted in a failure. These flexible boots when they fail allow for an enormous amount of material to be discharged into the surrounding area. This was the reason for most of the dust and powder that had built up beneath the silos.
As previously mentioned, portable vacuum cleaners were available on certain levels of this structure. However, there were seven different levels, each with grated flooring. It would be unreasonable to ask operators to bring the vacuum up and down the stairs as part of their normal cleaning operations.
Key Points:
– Maintenance activities (such as magnet cleanouts) often require that flexible boots are removed and equipment be disassembled. This leads to powder spills into surrounding areas.
– Flexible boots beneath silos failover time due to pressure/vacuum swings. Many were found to be worn and leaking.
– Portable vacuum cleaners were available only on certain levels without an easy way to transfer up and downstairs.
The Solution
It was agreed by all parties that upgrading from Class II Division 2 Group G in this building compartment was not a reasonable solution and that the amount of dust generated needed to be controlled.
First and foremost, by investing in additional portable vacuum cleaners (that are combustible dust rated!) By training of maintenance staff and operators, the maintenance activities that had previously caused large amounts of powder spillage were now controlled. It would be incumbent upon the supervisors and maintenance managers to ensure that the retraining took place, and that operators and maintenance staff were adhering to the new procedures which would help to greatly reduce the amount of spilled powder.
Secondly it was decided that investing in higher quality flexible boots to be placed on the outlet of each silo would be needed to reduce the burden on maintenance staff who are often replacing worn flexible connections. They were previously so quick to fail that preventative maintenance activities could not keep up. With the addition of these new higher quality flexible connections, the life was extended, fewer leaks developed, and they could be replaced on a fixed schedule before leaks developed.
An additional recommendation was made to include a centralized dust collection system in areas surrounding pieces of equipment that must be opened and cleaned often. For example, surrounding the mill where fugitive dust can escape quite readily anytime the equipment is plugged or needs to be cleaned.
This room is now classified as a Class II, Division 2, Group G hazardous location and the existing electrical equipment is still in place. There were some upgrades of non-rated electrical items that required replacement to achieve this Class II Division 2 rating, but the cost was orders of magnitude less than the upgrade
would have been for replacing all electrical equipment in the area to meet Class II Division 1 Group G requirements.
Key Points:
– By investing in additional portable vacuum cleaners (combustible dust rated!) AND through retraining of maintenance staff and operators, the maintenance activities that previously caused large amounts of powder spillage are now more controlled.
– Investing in higher quality flexible boots that can withstand the pressure fluctuations of the silos has led to reduced wear and longer service life…and fewer leaks!
– The room is now classified as Class II,
• Division 2, Group G and the existing electrical equipment is still in place.
Conclusions
When looking at an area that appears to require electrical classification, it is imperative to ask the question “Could this area be classified as a less significant hazard given a more effective dust control and removal mechanism”?
In many cases, we will find that Class II Division 1 Group G is appropriate only for those areas which are releasing the most fugitive dust and powder. Furthermore, we find that in many cases it is possible to reduce the classification from a Division 1 area to a Division 2 area simply by removing the fugitive dust escape mechanisms.
Referenced Standards:
NFPA 70 – National Electrical Code,
NFPA 499 – Recommended Practice for the Classification of Combustible Dusts and of Hazardous Locations for Electrical Installations in Chemical Process Areas,
NFPA 652 – Standard on the Fundamentals of Combustible Dust,
NFPA 654 – Standard for the Prevention of Fire and Dust Explosions from the Manufacturing, Processing, and Handling of Combustible Particulate Solids,
Dustcon Solutions, Inc.
Authored by Timothy Heneks, PE
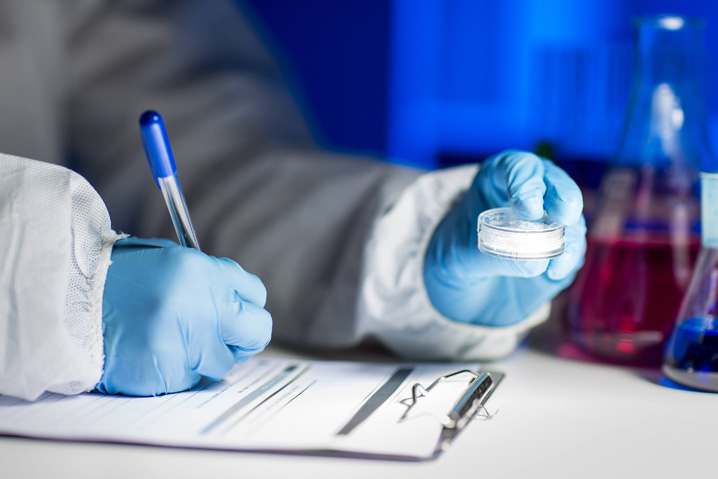
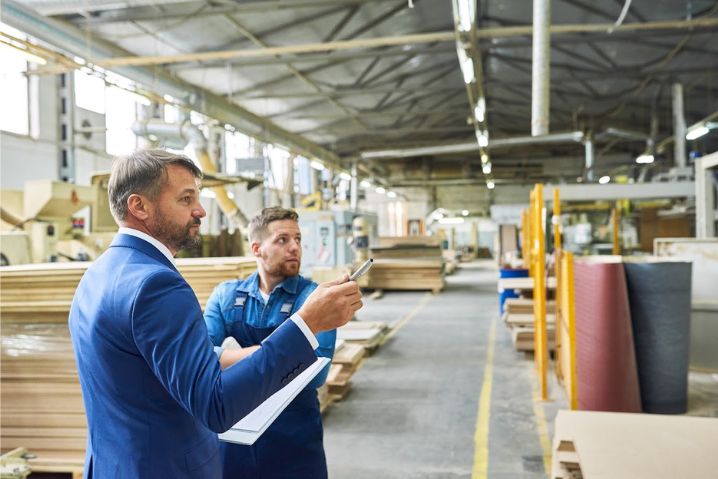
Addressing NFPA 652 Standard Regarding Combustible Dusts
Do you operate a facility that requires you to engage with substances that are dusty or powdery in n
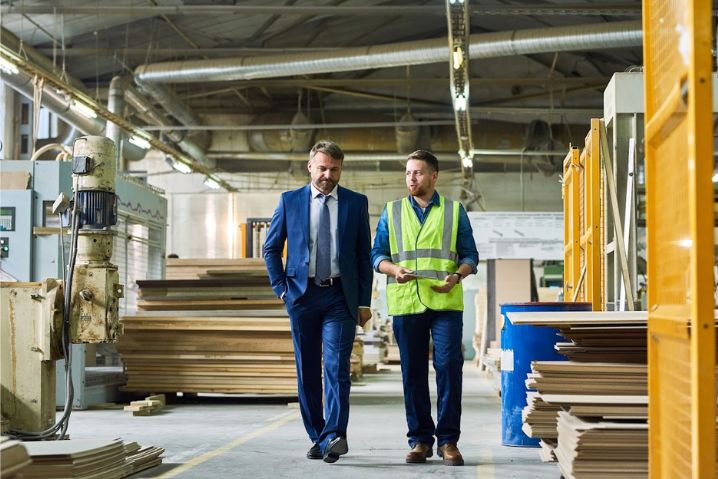
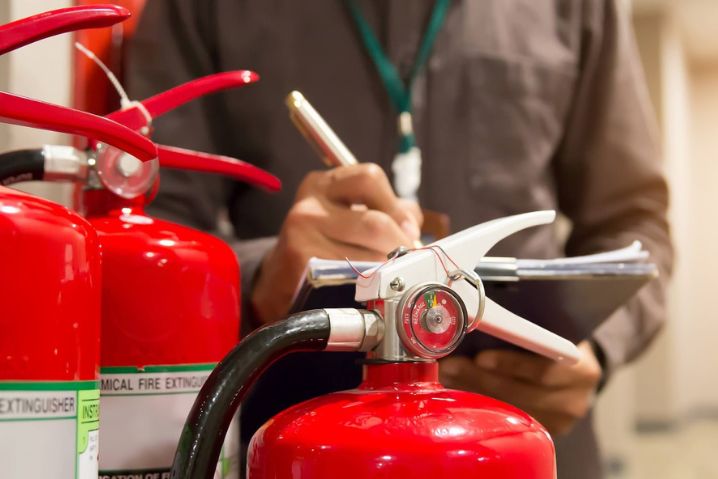
6 Industries Added by OSHA to the Combustible Dust NEP Program
n late January 2023, a new version of the Combustible Dust National Emphasis was issued by the Occup
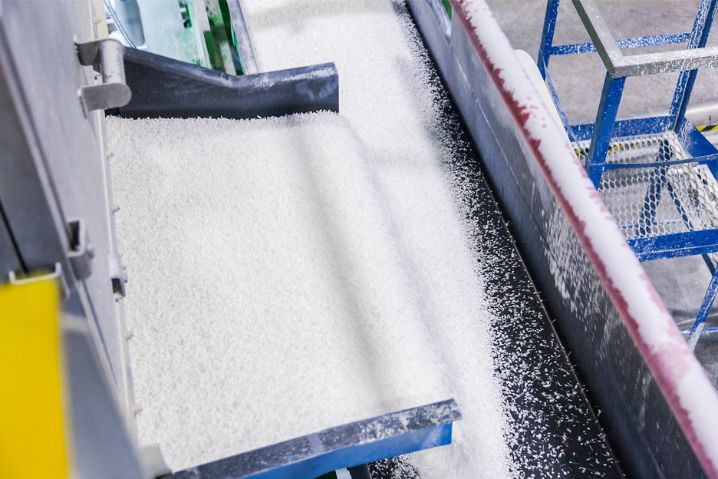
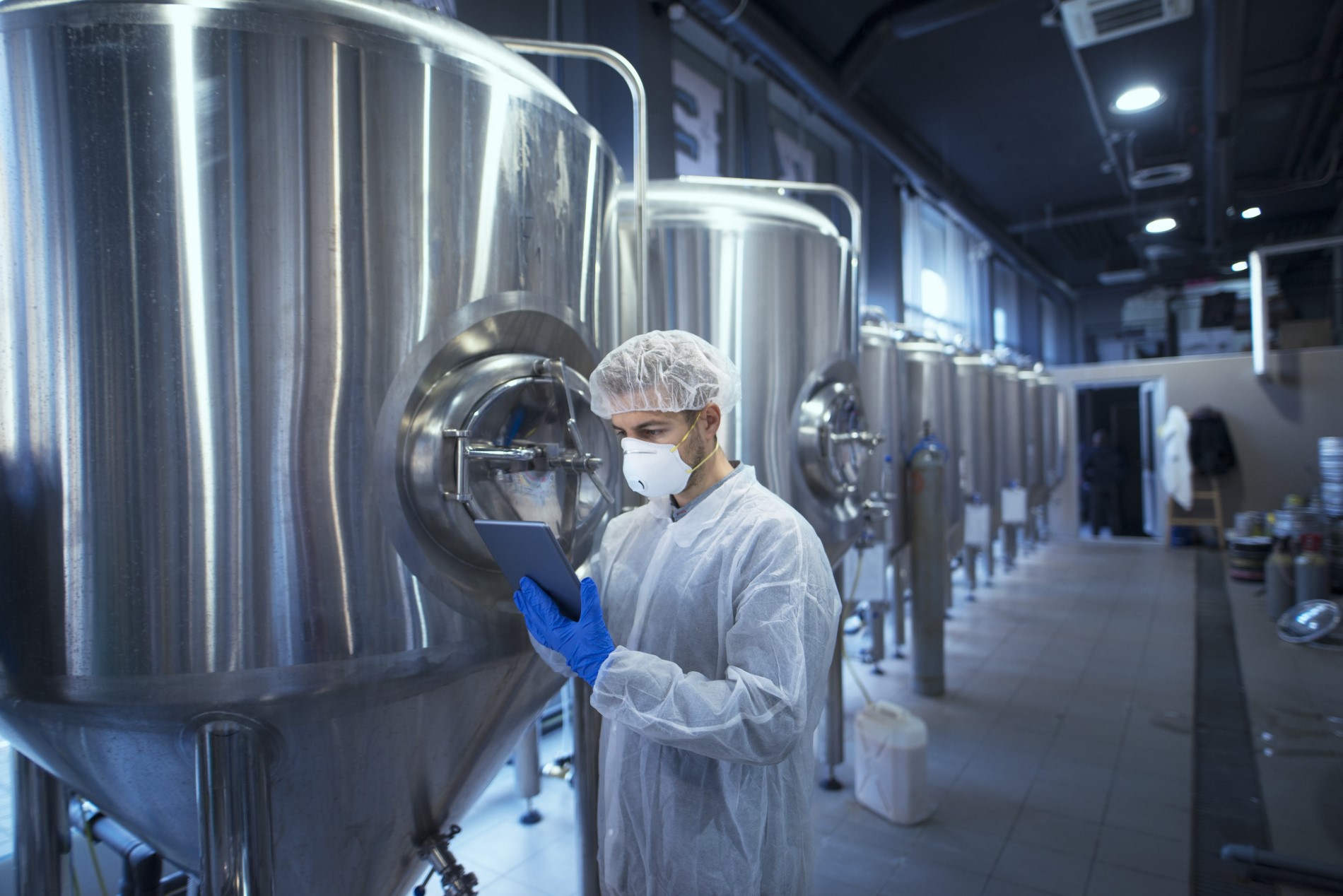
Ensuring the Safety of Facility Through Dust Explosion Test Data
“Could it be a problem if my powder has demonstrated 3mJ of minimum ignition energy and 256 bar.m/