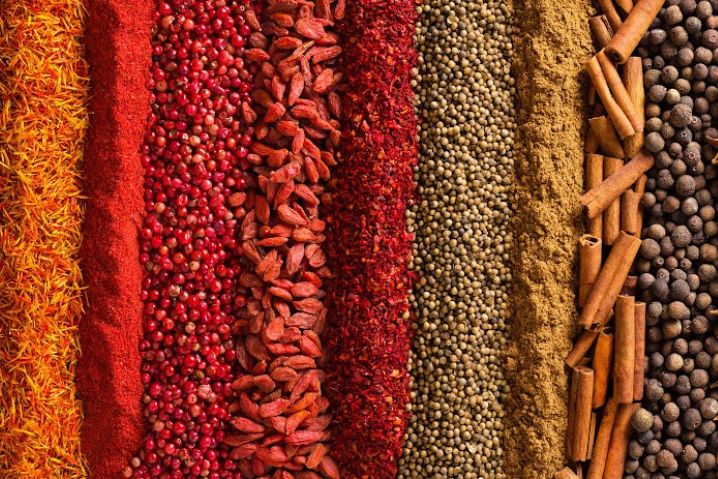
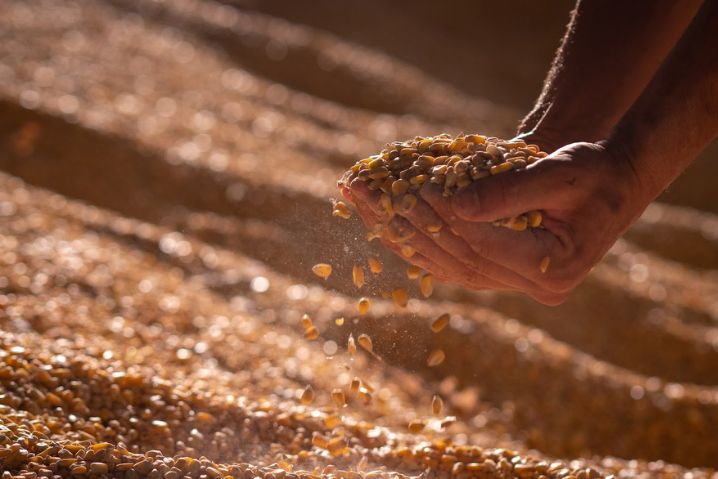
The Challenges of Handling Powders and Bulk Solids
Although when thinking of food and beverage processing, people often don’t consider bulk solids and powders, they form the foundation for a host of food-based products, including baked goods, seasonings, flavoring agents, and beverages.
Regardless of their role in a plant, handling them appropriately is of utmost importance as it could otherwise lead to disastrous effects. This may range from abysmal quality of the end product to equipment undergoing complete destruction in an explosion. These challenges are encountered on an everyday basis by beverage and food processors.
When handling bulk solids and powders, a pertinent challenge is ensuring that the materials’ flow is managed. In order to be successful here, the material that is being handled should be studied.
It is a common fact that the behaviors of solids vary greatly from liquids. By implementing appropriate strategies and designs, it is possible to prevent issues of flow. It is common for bulk solids and powders to stick together when systems are created without taking into account the type of material. This could cause ratholing, bridging, as well as several other blockages. Production may be delayed by these scenarios, which could also cause damage to the equipment and create safety issues.
When working on design, it is necessary to take into account aspects such as temperature, humidity, as well as particle size, coupled with the pattern of the flow of the equipment dealing with the material.
As such, in order to make sure that the materials flow smoothly, it is necessary to ensure that the equipment is designed properly. In both pipes as well as conveyors, the bulk solids and powders keep moving when air flow or vibration is employed. To facilitate the movement of the ingredients, special material may also be used.
When dealing with specific bulk solids and powders, it may be challenging to ensure that the quality and consistency of the product are retained. The final product’s texture, flavor, and nutritional aspects may be affected due to degradation. Segregation is also impacted since during the distribution phase, the mixture undergoes separation due to the various particle sizes, which could eventually deteriorate performance.
If the materials are transferred using hoppers, the cone must be appropriately shaped. If the particles are coarse, it is best to opt for a funnel-flow cone, since the 45-degree slope propagates material using gravity for these free-flowing particles. A funnel-flow cone, however, is not the best option if the mixture’s material is vulnerable to the segregation of various ingredients.
The slope is either 60 degrees or greater when it comes to mass-flow hoppers and they are in place for fine particles, cohesive solids, materials that are degradable and blends prone to segregation within a silo. Even when the sizing of the outlet is not appropriate for the relevant materials, bridging may occur.
Potential Solutions
There are remedies available for processors dealing with any of the aforementioned issues.
It can be challenging to choose between improving existing equipment through retrofitting and employing brand-new systems in order to expand production. The primary hurdle encountered while facing this challenge is access to resources. For a lot of processors, there aren’t adequate resources or people to work within the deadline.
There are also safety issues associated with dealing with bulk solids and powders within the food processing industry. Since the materials are combustible and explosive, disasters could range from the damage of equipment to severe injuries, or worse. When working on the design of the equipment and while setting them up and operating them, it is necessary to be cautious of these risks and implement solutions that can mitigate these hazards.
Processes must adhere to safety regulations and best practices when operating the equipment. Combustible dust accumulation can be mitigated using dust collection systems. The prevention of the buildup of static electricity and electrical malfunctions is possible by employing relevant safety measures.
In food and beverage facilities, safety, efficiency, and quality are all crucial aspects of dealing with powders and bulk solids. While it is crucial to ensure that the materials flow consistently and seamlessly, the quality and safety of the products and facilities should not be compromised. Employees can gain significant knowledge and skills required to deal with bulk solids and powders through effective training and development.
It is possible for workers to play a key role in preventing problems from becoming disasters by standing on the frontlines. Simultaneously, operations pertaining to the handling of bulk solids and powders must be cautiously designed and monitored to ensure the production of top-notch products without compromising on safety.
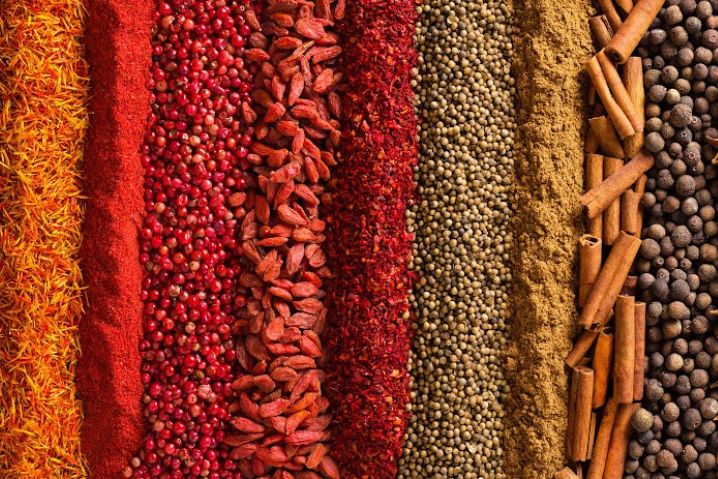
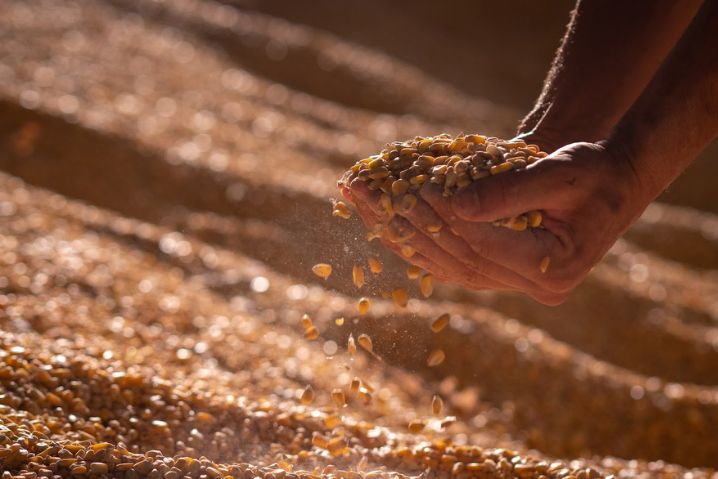
The Challenges of Handling Powders and Bulk Solids
Although when thinking of food and beverage processing, people often don’t consider bulk solids an
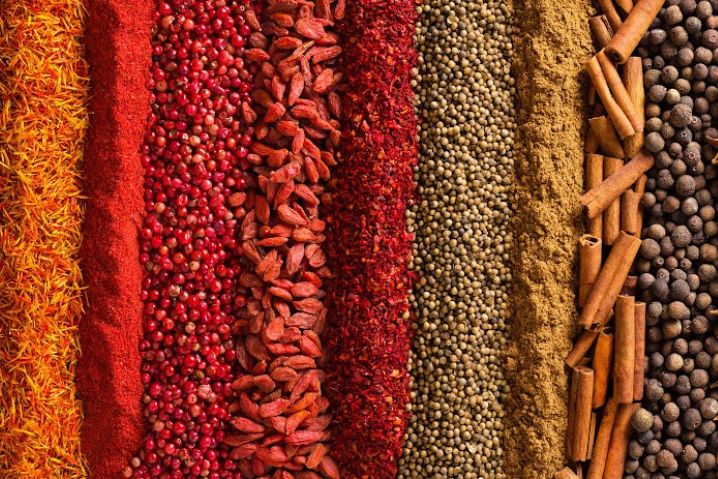
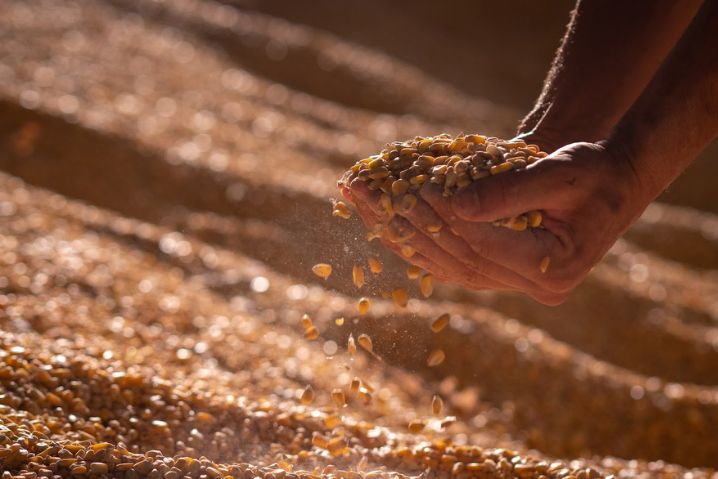
Challenges Associated With Processing Bulk Solids and Powders
There are several reasons why it is particularly difficult to handle bulk solids and powders in faci