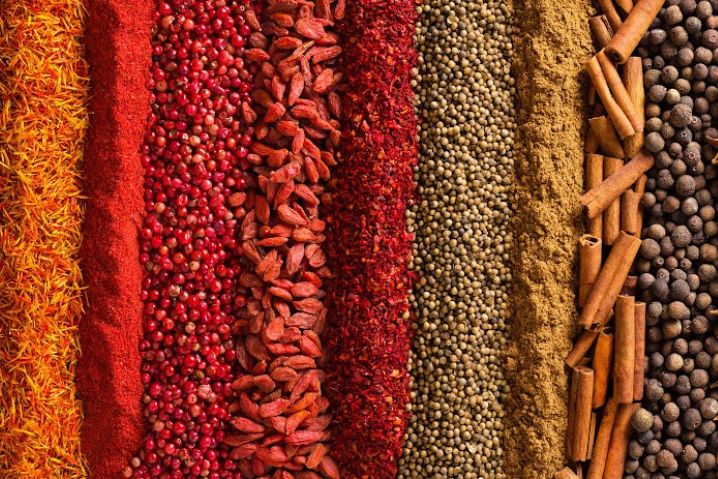
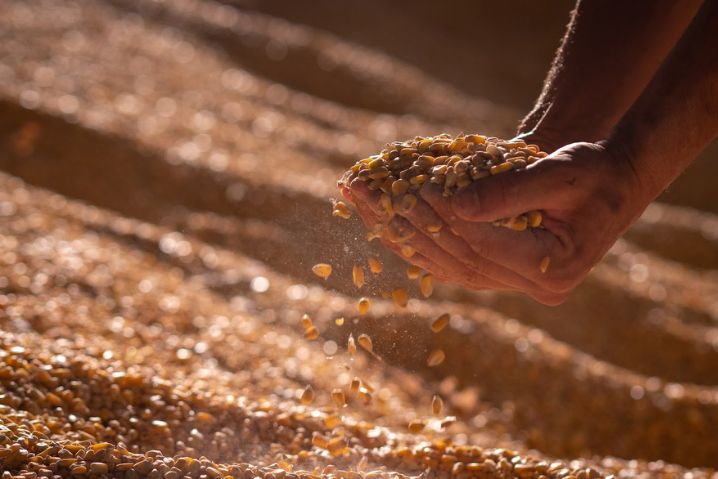
Challenges Associated With Processing Bulk Solids and Powders
There are several reasons why it is particularly difficult to handle bulk solids and powders in facilities that process food or beverages.
In addition to the unique equipment required for unloading, conveying also requires specialized machines. Unlike packages and products, they are not distinct units. Similarly, they are different from liquids since they are not free-flowing. This is the reason various flow interruptions can affect them. If they are left unmanaged, they could result in electrostatic explosions that can be extremely dangerous.
A conveyor system that transports ingredients is the bare minimum in facilities handling food or beverages. It is also important that contamination of ingredients is avoided at all costs. The transportation of powders is particularly tricky since dust should not escape into the facility as it could create explosion hazards.
It can be asserted that the issue of flow is of particular concern. A few powders and bulk solids demonstrate the tendency to stick to surface areas, depending on their fat and moisture content. Gradually, the tubes’ interiors may accumulate a substantial amount of buildup or the product may experience “bridging” or “ratholing” in hoppers, which could prevent their descent. This is particularly pervasive in products such as brown sugar, pancake mix, and almond flour.
Options for Conveyance
When dealing with bulk solids and powders, the importance of aligning them with the appropriate conveying system cannot be overstated. Tubular cable, flexible screw, pneumatic, and vibratory beds are usually highly common.
In order to send any product via a tube, compressed air is employed by pneumatic conveyors. An auger – typically made of stainless steel – is leveraged by flexible screw conveyors with a tube made of stainless steel or polymer. Routing them via any angle is possible, as long as there are no bends or curves. Disks – typically made of polymer – are used by tubular conveyors. Through the pipe’s interior, the disks are tied to a cable, which is used to drag the product. Reciprocating motion is leveraged by vibratory conveyors to transport products over a trough or a bed, wherein no method of propulsion is applied.
The product type determines the right principle: flour and other fine products work better with pneumatic conveyors, while those that will undergo seizing, smearing, caking, or packing may be transported via flexible screw conveyors. For the latter, tubular conveyors also work effectively, as they do for products like trail mix. Lastly, potato chips and other large bulk products that contain fragile materials are better when transported via vibratory conveyors.
Conveying that is dilute- or dense-phase is typical when working with pneumatic conveyors. Simply put, when a product blown through a tube is propagated via a constant stream, it is called the dilute-phase. On the other hand, the slug-based conveyance is enabled via the dense-phase. Dense-phase conveyance is not only more energy-consuming and expensive but is also used when handling heavier products or conveyance over a distance of more than 100 yards.
Cleanliness is Key
Cleaning is primarily a huge challenge for several applications. Regular cleaning is of utmost importance for equipment that handles products vulnerable to smearing or those that stick to surfaces. In particular, this is true with applications that must frequently undergo changeover.
Any system handling material is cleanable if it is equipped with clean-in-place capability or requires very little effort to be disassembled. Usually, it is very challenging to clean pneumatic systems. However, since dense-phase systems lead to sticky materials clinging less to the surface, they tend to be easier.
Usually, the augur can be easily removed in flexible screw conveyors, while an oversized “pig” attachment that resembles a sponge can help clean tubular conveyors and their interior surfaces.
In vibratory conveyors, product flow is particularly crucial, as they convey products toward open beds. It is necessary to spread the product evenly across a bed in order to efficiently feed freezers, dryers, sorters, or whatever equipment lies underneath. In the case of an oily product or a frozen environment, this becomes challenging since the movement across the conveyer bed can get inhibited.
Companies employ vibratory conveyors that are equipped with steam pipes below the bed coupled with belt conveyors that have specialized tail rolls in order to resolve this issue. This tail roll is essentially a shaped roller that helps eliminate the ice over the belt.
For bulk products that must undergo screening, one more issue is that nuts and other large materials tend to get stuck within screen holes. However, when two screens are sandwiched with rubber balls (food-grade, of course), they tend to bounce and remove anything that gets stuck within a screen.
Unloading and loading
Only the conveyor responsible for handling does not encounter challenges that underlie transporting bulk solids and powders. A primary challenge that is pervasive across facilities is the process of loading products and unloading them.
Similar to several other challenges, employing proper equipment can resolve this issue. The bags that unload the products and those into which they are loaded must be appropriate.
When unloading, you must ensure that a bulk square-shaped bag is set in place to hold the material. It should also remain hanging to ensure that the bottom expands when materials start to flow in.
The material moves to the corners when you place the bag in the pallet to create a stable base. This way, the bag will remain erect and thus, will be much easier to handle.
The right type of equipment should also be used with each bag. Flow may be interrupted, leading to dusting, when a discharge spout is used, which is very short or extremely small in diameter.
Avoiding flood feeding is crucial when unloading into bulk bags since it could cause material overflow. Alternately, during the flow, the chomping of material is also a possibility. In order to avoid such issues, vibratory feeders are equipped with the ability to meter their flow when pushing any output to a stream that is already even.
The emptying of fine powders into bags that are bulk is typically accompanied by dust. Although it can definitely help to clamp the discharge spout to the neck of the bag, it may not work all the time. It is possible to find dust collectors that can operate independently or within an integrated system.
One more hazard is explosions. When electrons build up around powder articles, dust explosions could occur. This buildup could gradually cause a spark, which in the wrong setting, could lead to an explosion.
In order to avoid explosions, it is necessary to ensure the proper grounding of the equipment. This way, electrons cannot flow as powders to pass along into the particulates. Mitigating dust is enabled by using easy-to-clean equipment. It can be even more helpful if compressed air or other means are used to operate it instead of electricity.
There are several challenges associated with handling bulk solids as well as powders. Identifying potential challenges and determining the appropriate equipment will ensure better flow.
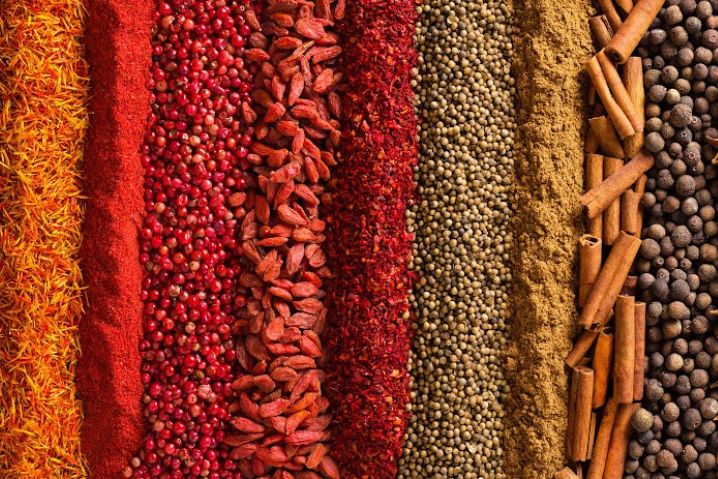
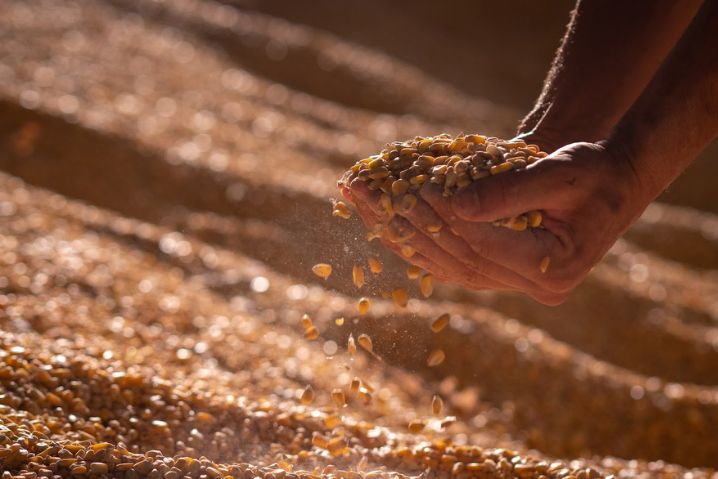
The Challenges of Handling Powders and Bulk Solids
Although when thinking of food and beverage processing, people often don’t consider bulk solids an
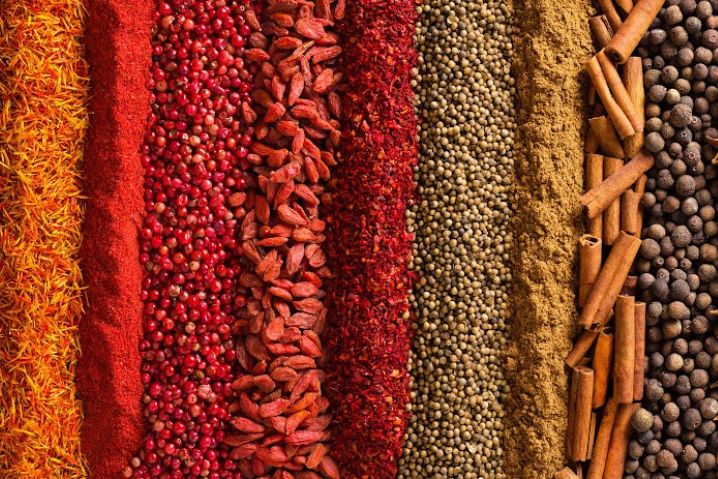
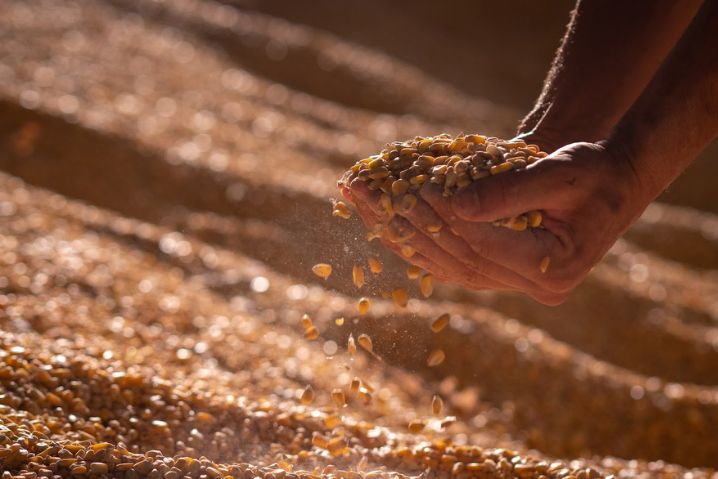
Challenges Associated With Processing Bulk Solids and Powders
There are several reasons why it is particularly difficult to handle bulk solids and powders in faci