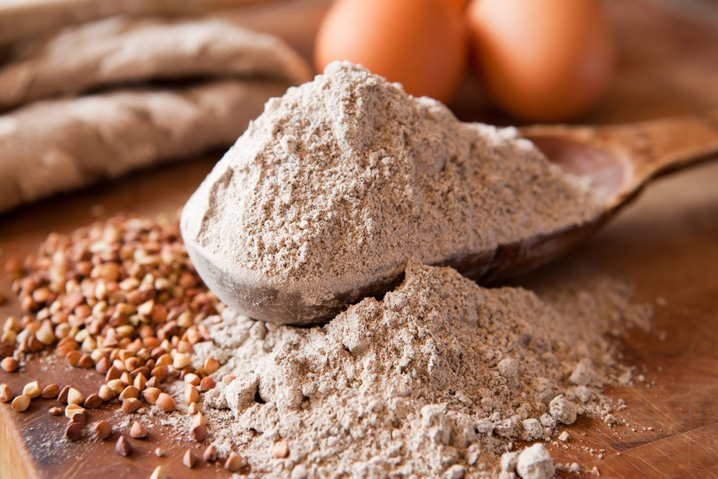
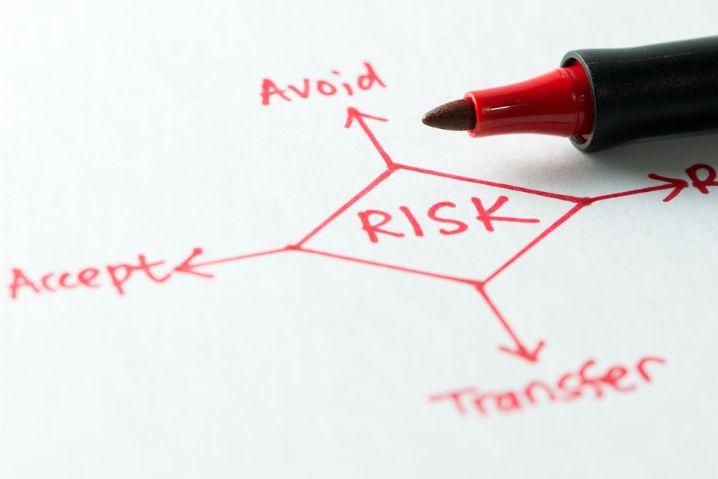
Answers to Frequent Questions on Dust Hazard Analysis (DHA)
1) What are the steps to undertake if I have not adhered to the deadline imposed in NFPA 652 pertaining to the performance of a Dust Hazard Analysis?
Answer: The deadline outlined in the National Fire Protection Association (NFPA) 652 standard pertaining to the DHA was September 7, 2020. In case your facility handles or processes dusts that are explosive or combustible, this deadline applies to you.
Dustcon Solutions offers its expertise in process safety and the employees have been receiving inquiries regarding DHAs, although the deadline is way in the past.
Since performing DHAs requires external consultants to visit plants and facilities, it can be a slightly time-consuming process. This is why several companies are still lagging behind.
You can get in touch with us if your DHA is still pending because this criterion is still in place and not adhering to it may create unnecessary problems for your facility. More importantly, you are putting your facility and employees at risk of facing various hazards by delaying your DHA.
2) Do I need to comply with any other obligations following a DHA if I want to adhere to NFPA 652?
Answer: Certainly. Once you receive your DHA report, ensure that you implement the recommendations outlined in it.
It is also necessary to remain abreast of any updates in the DHA requirements and ensure that whenever your facility’s equipment, processes, or other aspects are updated, a DHA is conducted to ensure that they meet the relevant criteria. The DHA must also be renewed or analyzed once every five years.
Here are a few tasks you should be performing periodically for optimal safety:
- The operating areas should be reviewed periodically to ensure that the employees are adhering to the operating procedures as well as other best practices underlying safety.
- Written procedures concerning facility operation and equipment must be updated.
- It is pertinent to devise a program to inspect, test, and maintain the facility, and must include the following aspects:
- NFPA-compliant equipment to prevent or protect against explosion and fire,
- Equipment used for dust control,
- Standards for housekeeping,
- Sources that could potentially cause ignition,
- Equipment used for various processes, such as process interlocks,
- Changes and updates of processes,
- Bearings lubrication,
- Documentation of this activity is necessary and records must be maintained,
- Devise and implement training programs in line with the combustible dust hazards and solutions for these risks must be determined and applied. Contractors must be recruited for training programs as required.
- An emergency plan should be devised and an annual review of its recommendations is necessary.
- If any incidents emerge, they should be assessed and recorded along with the learnings and any changes that were implemented.
- To protect against hazards and risks associated with any changes, new procedures must be put in place. Change management is critical.
- Documentation concerning the risks of explosions or dust fires must be recorded and managed as per predetermined standards.
Although this is not an exhaustive list, this is a good starting point. Refer to NFPA 652 for further information.
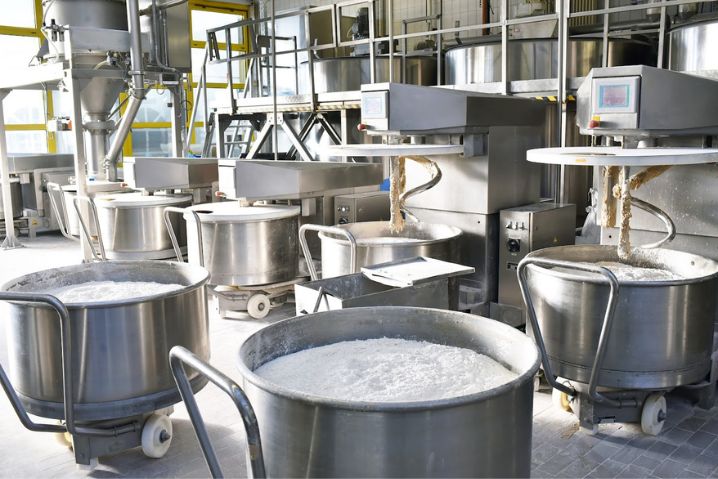
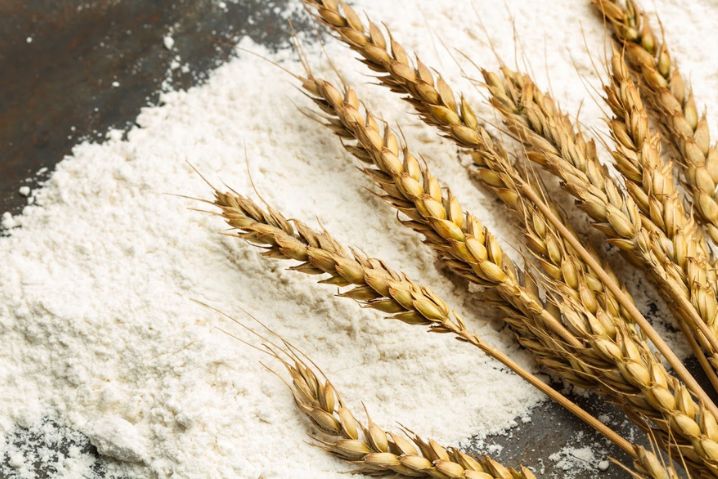
Your Dust Hazards Analysis Requires an Update
North America witnessed multiple dust explosions across various facilities in 2015. In the aftermath
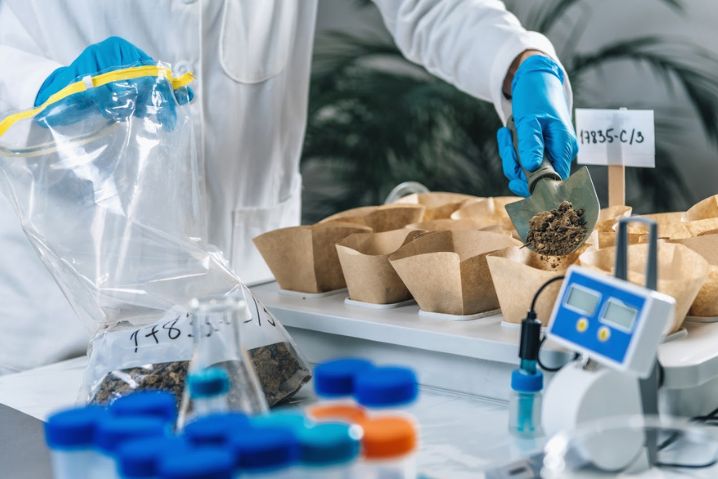
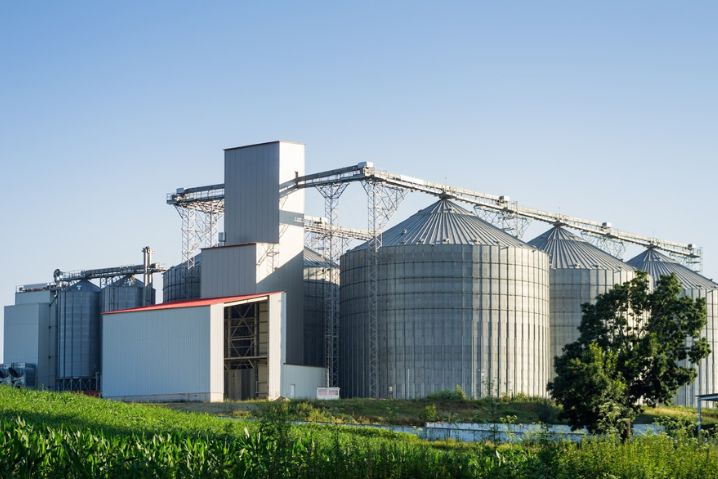
What is a Dust Hazard Analysis (DHA)?
By now, it must be quite apparent to you that a Dust Hazard Analysis is required as per NFPA 652 and
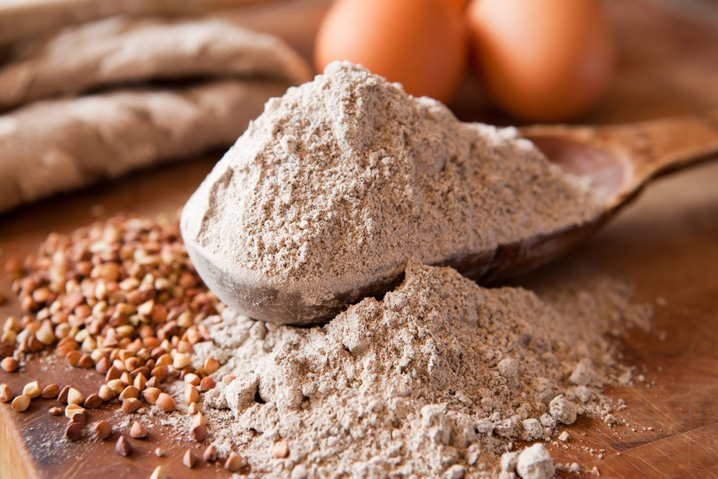
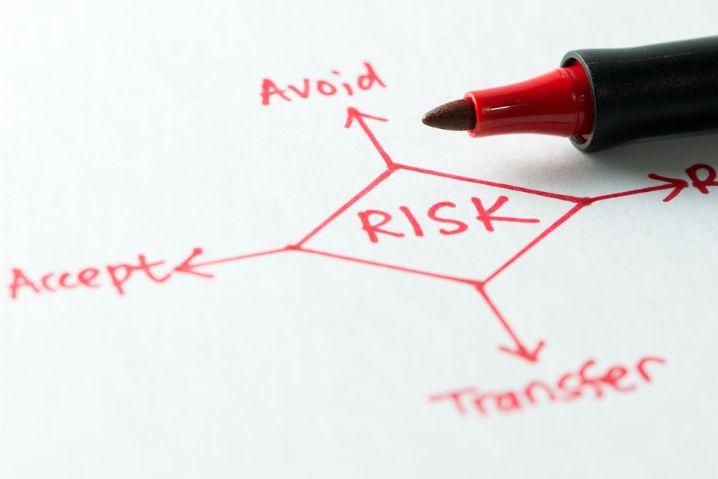
Answers to Frequent Questions on Dust Hazard Analysis (DHA)
1) What are the steps to undertake if I have not adhered to the deadline imposed in NFPA 652 pertain