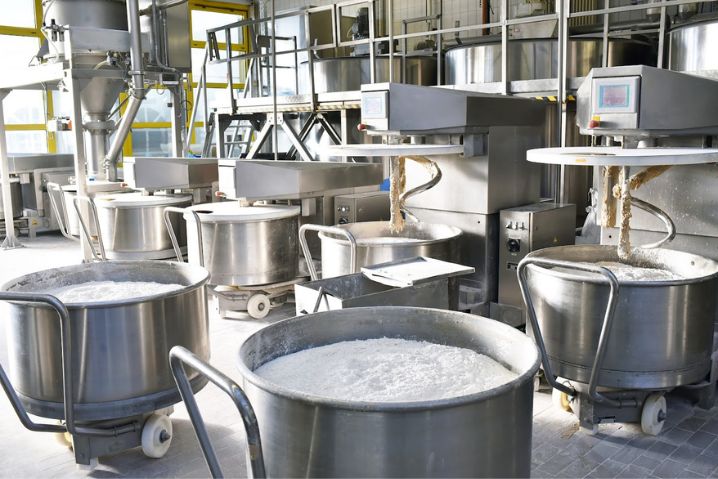
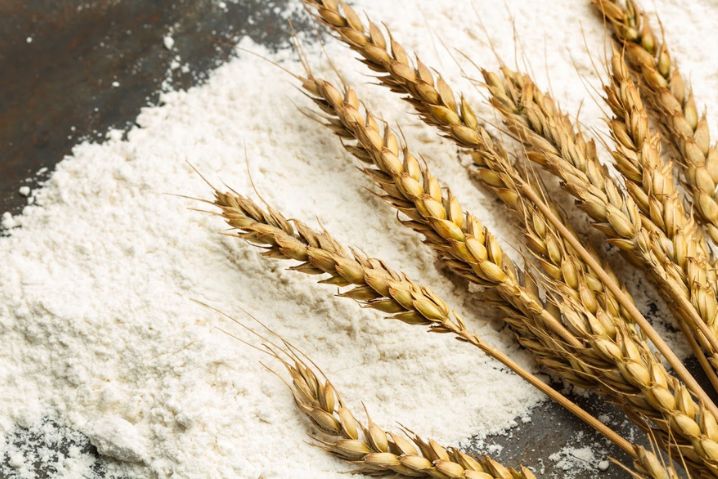
Your Dust Hazards Analysis Requires an Update
North America witnessed multiple dust explosions across various facilities in 2015. In the aftermath, a new standard was drafted and implemented by the National Fire Protection Association, known as the NFPA 652 Standard on the Fundamentals of Combustible Dusts. It was agreed upon as a crucial measure for mitigating dust explosion risks and fire hazards in the industry. With this standard, the requirement for the Dust Hazards Analysis was also introduced and was defined as:
“The owner/operator of a facility where powders that have been determined to be combustible or explosible [….] are present in an enclosure, shall be responsible
Every five years, the DHA will need to be assessed and modified according to a new version of the standard released in 2019.
We have recently been receiving multiple requests concerning the review and the updating of various DHAs because of reasons beyond the expiration of the five-year period. This article will identify and address various valid reasons for reviewing and updating your DHA.
What makes this the right time to modify your DHA:
Inadequate or inaccurate implementation of DHA findings
Our research revealed that several companies that were recruited to conduct DHAs for various facilities did not implement the recommendations in an efficient manner. In addition to a certain level of inertia within the company, DHA recommendations were occasionally impractical or extremely expensive and the costs were not justifiable. In certain cases, the inaccurate interpretation and implementation of the recommendations have also rendered them ineffective. This has led several companies to seek our assistance in understanding the DHA. A few have also sought recommendations on alternative measures to attain safety, which are more pragmatic or economical.
Companies have also sought our services to verify and validate the implementation of their DHA’s recommendations.
It is important to note that safety measures rely on the operations of the facility and can be multifold. Instead of a complete redesigning of the plant, operations may be made safer through the regulation of various ignition sources. Similarly, it may not be necessary to upgrade the existing electrical equipment or modify the design to make it more explosion-proof. Instead, flammable atmospheres can be controlled or mitigated more effectively. As opposed to implementing expensive solutions, designs can be altered to eliminate electrostatic sparks.
It is a sign of the failure of the DHA assessor if the recommendations do not seem practical. It is recommended that companies only sign off on the projects after analyzing DHA reports and ensuring that they are practical in nature.
A consultant from our company was hired to revisit a site because OSHA had indicted their facility. A quick survey revealed that the company did not implement any of our recommendations.
New products or powders were introduced
There may be cases where a powders supplier may be replaced or the powders that must be processed are altered. In such cases, powder accumulations as well as dust clouds may shift in terms of combustibility properties due to changes in the specification of the powder. Changes in the physical or chemical compositions of powders can certainly impact their combustibility. If a powder is drier or finer than its predecessor, its minimum ignition will decrease (igniting them as dust clouds will be easier) and the severity of the explosion will be greater due to a higher Kst value and maximum explosion pressure. The electrostatic charge’s retention propensity will also change with any alteration in moisture content.
DHA’s safety basis may therefore be affected by such changes in physical and chemical properties. This may lead to insufficient protection against explosions, inadequate arrangements for housekeeping and dust collection, as well as ineffective protection in the face of static electricity. These are all justifiable reasons to update your DHA.
Altered equipment and process
It is common to modify process equipment regularly. A replacement of a conveyor or a hopper will require a change in the unit. When a storage hopper is replaced, a brand-new vent for explosion relief may be fitted. The explosion relief area that is required may change in case the hopper’s volume, strength, or shape are updated.
This holds true for other equipment as well. Electrostatic hazards may emerge when equipment material is changed to plastic from metal. The precautions taken to provide protection in the face of static electricity may change even due to small variations in footwear.
It is also important for DHAs to be revalidated periodically to avoid drift and changes over time.
No review, update, or full implementation of management and training systems
Training
Training must be imparted regarding the hazards facing employees due to dust combustibility, as per the NFPA 652 standard. In particular:
The standard requires that relevant employees undergo training about general safety and hazards pertaining to combustible dust as well as solids. Employees should also undergo training that is job-specific to learn about hazards of fire and explosions caused by particulate solids and combustible dust in their facilities.
An organization can easily neglect dust-specific training as other priorities and training take priority. In addition, the organization must train new employees on their first day.
The Dustcon Solutions team offers both offline as well as virtual training courses for companies of all sizes.
Management Systems
The effectiveness of management systems depends on their proper implementation and maintenance. It is possible to lose focus in the application even in this scenario. According to the NFPA 652 standard, it is the duty of the owner or operator to assess whether the management systems are effective through regular review. It is also their responsibility to assess and maintain the management systems’ effectiveness.
It may help to review the changes in the management systems in place following the completion of your DHA.
It’s time for the periodic review
As stated at the beginning of the article, the NFPA 652 standard was issued in 2016 and for many companies, it may be time to conduct their periodic review. The standard clearly outlines that it is necessary for the DHA to be assessed and updated once every five years.
Next Steps
Several North American organizations are planning to assess and modify their DHAs. Following the review, a letter may be issued if no changes are required. Otherwise, an addendum may be attached defining the required updates. A DHA issued from scratch may be wiser if the facility underwent substantial changes.
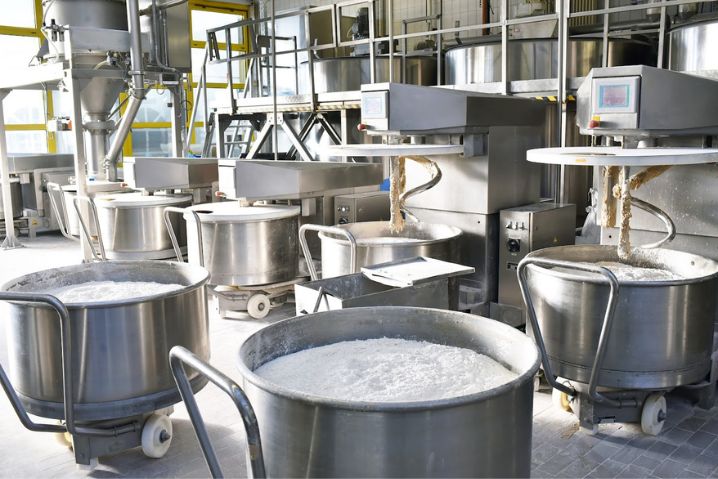
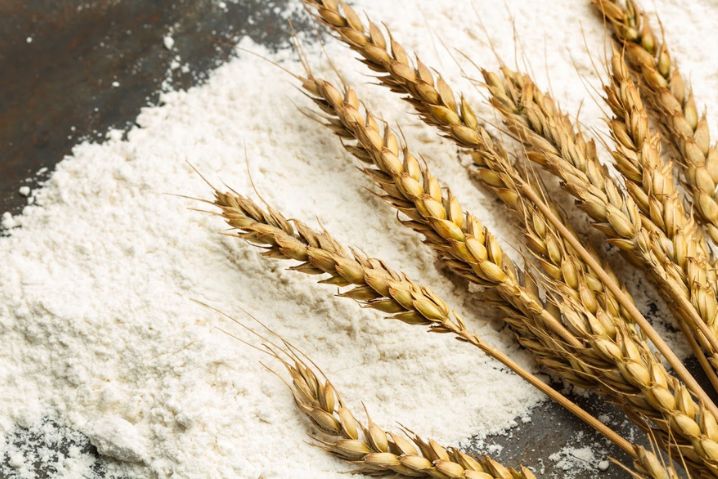
Your Dust Hazards Analysis Requires an Update
North America witnessed multiple dust explosions across various facilities in 2015. In the aftermath
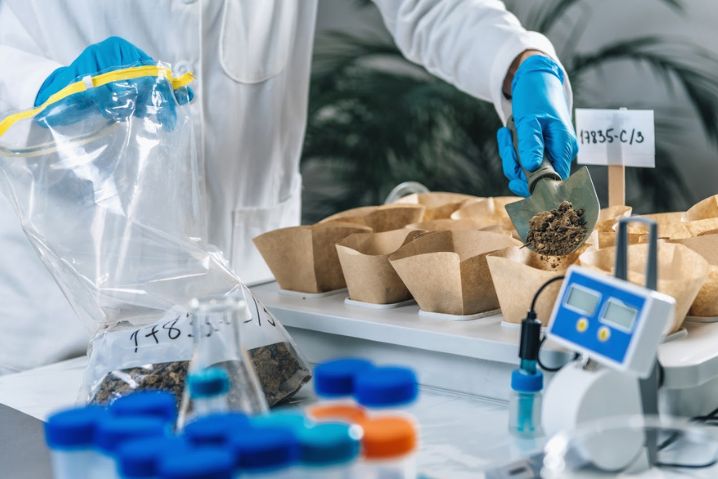
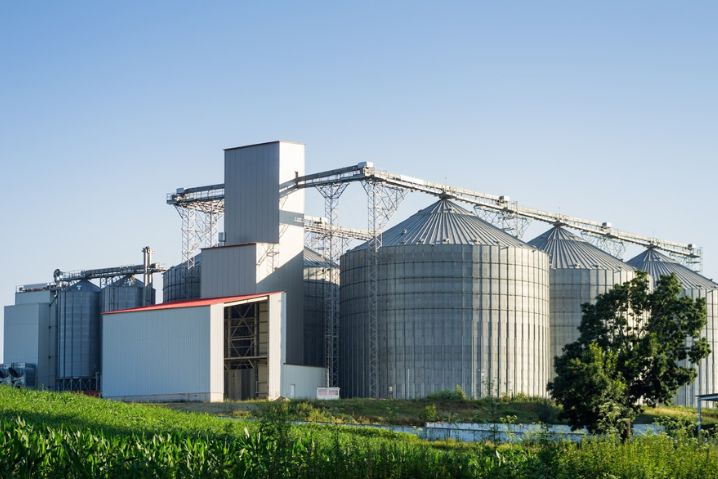
What is a Dust Hazard Analysis (DHA)?
By now, it must be quite apparent to you that a Dust Hazard Analysis is required as per NFPA 652 and
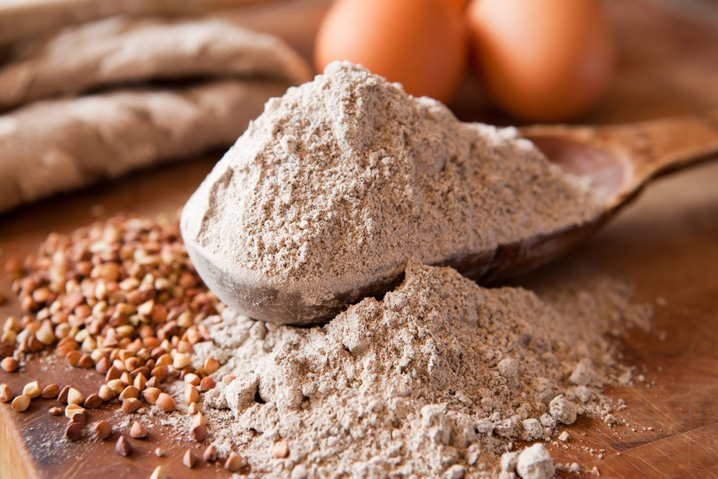
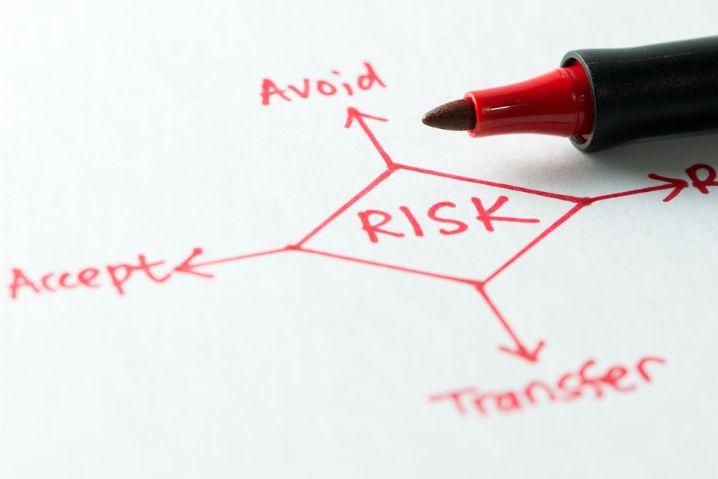
Answers to Frequent Questions on Dust Hazard Analysis (DHA)
1) What are the steps to undertake if I have not adhered to the deadline imposed in NFPA 652 pertain