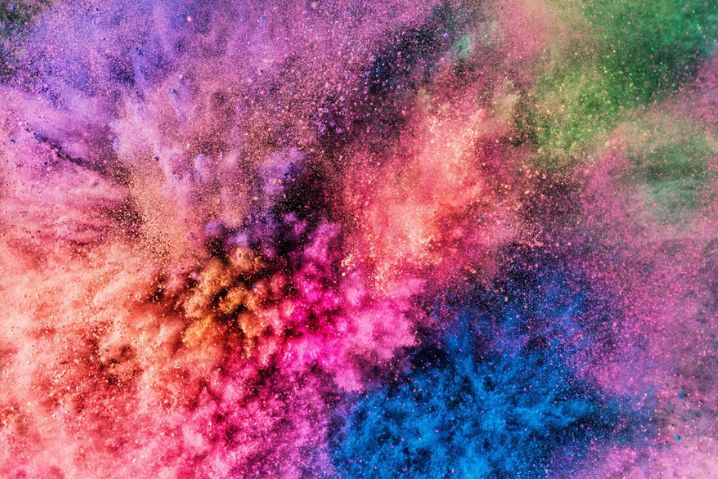
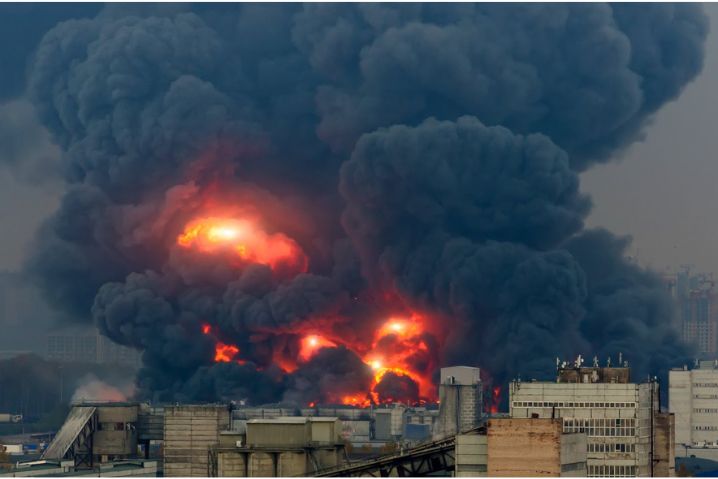
Risk Normalization Leads to Explosions
Dust explosions do not occur very often in processing companies. There are a few cases where a dust explosion has affected organizations but typically, they are perceived as issues that other companies experience. This exact thought process breeds complacency, which can be a costly mistake.
The prevention of explosions is best achieved by understanding risk normalization, which is the main topic of this article. To drive home the point, we will discuss the circumstances that led to a packaging explosion in a flour facility in Switzerland. Let’s begin by understanding what exactly normalization of risk entails.
Normalizing Risks:
The process of normalizing risks entails:
* Gradually becoming complacent or even accepting of practices that are considered dangerous or hazardous.
* Viewing hazardous scenarios from a habitual lens since they happen every day.
* Since the existing processes that are quite hazardous haven’t led to serious instances in the past, accepting them unwittingly.
We are all comfortable with a certain level of risk. Otherwise, we would miss out on several normal experiences such as eating out, driving a vehicle, or traveling via a plane. But when a risk can lead to disastrous implications, it is crucial to not over-normalize it. When a combustible dust explosion occurs, it could adversely affect your facility while also harming your employees and the environment. Thankfully, combustible dust explosions are rare occurrences. Because we get through each day working on similar processes and using the same equipment, we may begin to overlook the potential hazards associated with them, leading to the “normalization of risk.”
Anyone who is responsible for process safety should focus on breaking the chain of normalization of risk. This may be achieved through the use of internal resources. However, in such cases, the over-familiarization with the facility may prove to be a hindrance. It is unlikely that an individual who engages with the facility on a daily basis can look at it from a fresh perspective and identify uncovered issues. At Dustcons Solutions, we have often encountered the problem of over-familiarization when it comes to identifying issues. A facility may have various problems that remain unaddressed, such as a buildup of dust in the electrical mortar or a dust collector inside the facility that remains unprotected. It may even be a powder receiving vessel that is generating an electrostatic discharge. There are even times when managers used inappropriate equipment in classified hazardous areas.
Flour Packaging Explosion
Switzerland was home to a flour mill that had a packaging station. The facility’s experience spanned several years when it came to milling and packing flour. On an unfortunate day, the sample room of the flour, which was entirely made of wood, witnessed a fire. The cause was not detected. However, since the conveyor belts were open, the fire spread at a quick pace, right from the first floor to the third floor, which was the area of temporary flour storage. The third floor eventually witnessed a dust explosion as the pressure resulted in the dust rising off the floor, ledges, and equipment. The ignition of this dust led to a secondary combustible dust explosion, which gradually led its way to the main packaging area. When a massive explosion occurred, the entire flour storage building collapsed. This gradually led to more explosions, severely injuring 17. Fourteen fatalities were reported. This incident led to damages exceeding $100 million.
In cases such as this, the typical issue is that dust deposits are considered normal and this leads to avoiding the employment of preventative measures as well as precautionary measures against dust explosions. Often, people remark that there is a lot of dust in flour mills and packaging units or that open conveyors are a norm. Companies often also claim that since they have employed safety officers, they check for potentially hazardous sources of ignition. Others state that since they never witnessed an explosion, it is not an issue. However, it doesn’t completely eliminate the risk.
Although it may seem easy to retain the status quo, it is important to fix any existing issues. Now, the question arises – what is the best way to break this habit and minimize the normalization of risk?
From the example above, it is evident that there were not adequate measures undertaken in the flour facility, which subsequently caused an explosion. This could have been avoided by ensuring closed conveyors, utilizing dust extraction in a more efficient manner, and employing effective vents providing protection against dust within dust collectors. With proper housekeeping, the dist present on the ledges, floor, and equipment could have been avoided, which could have prevented a secondary explosion. Belt slip detection, vibration detection, classification of hazardous areas, and appropriately rated, bonded, and grounded electrical equipment could have prevented ignition sources. A better building design or isolation valves would have also prevented the propagation of explosions between plant regions. Finally, it is pertinent to incorporate devices that can provide protection against explosions, including vents for explosion relief in the process region that can help ensure that in case of a source of ignition in the plant, any explosion will lead to minimal damage.
Summary
In any plant, it is crucial to be aware of the threats of normalizing risks. This can be avoided through periodic safety reviews in line with reliable regulations and standards. When hazards and risks are identified and assessed systematically, the assessor will be forced to consider all major hazards. It may also be beneficial to involve third parties in safety studies since they can bring experience, expertise, and a new perspective to the study that can enhance safety outcomes. In this way, the problem of risk normalization can be eliminated.
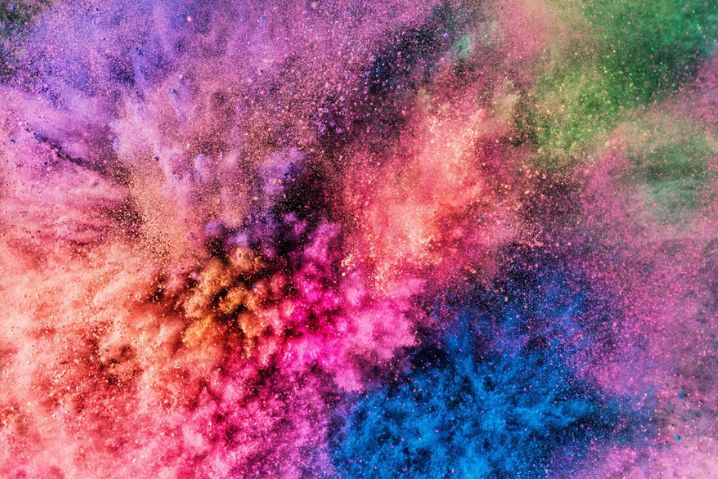
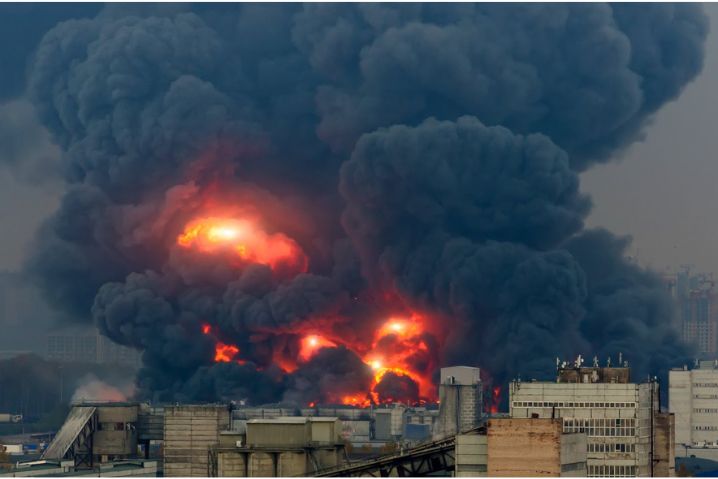
Risk Normalization Leads to Explosions
Dust explosions do not occur very often in processing companies. There are a few cases where a dust