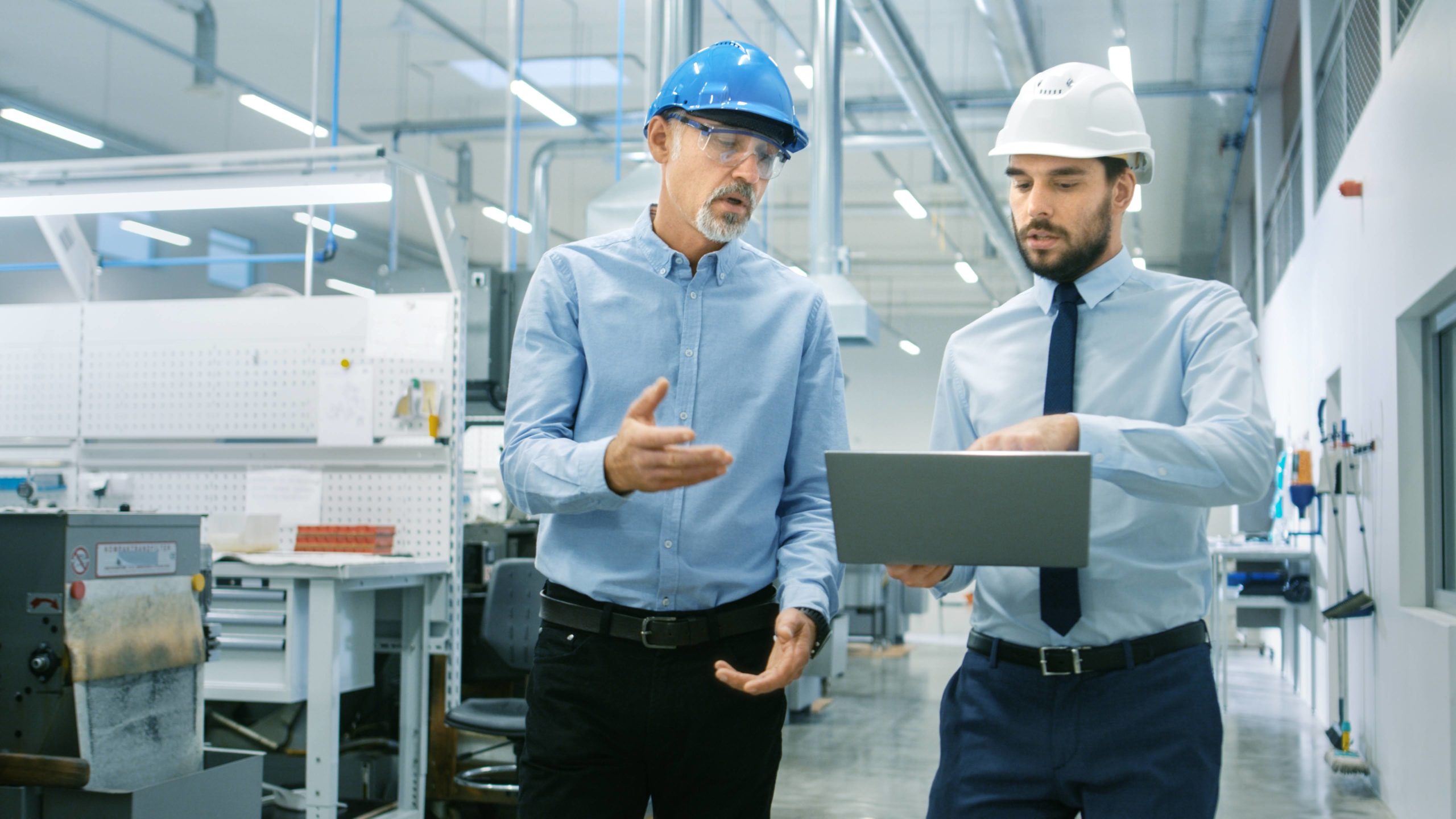
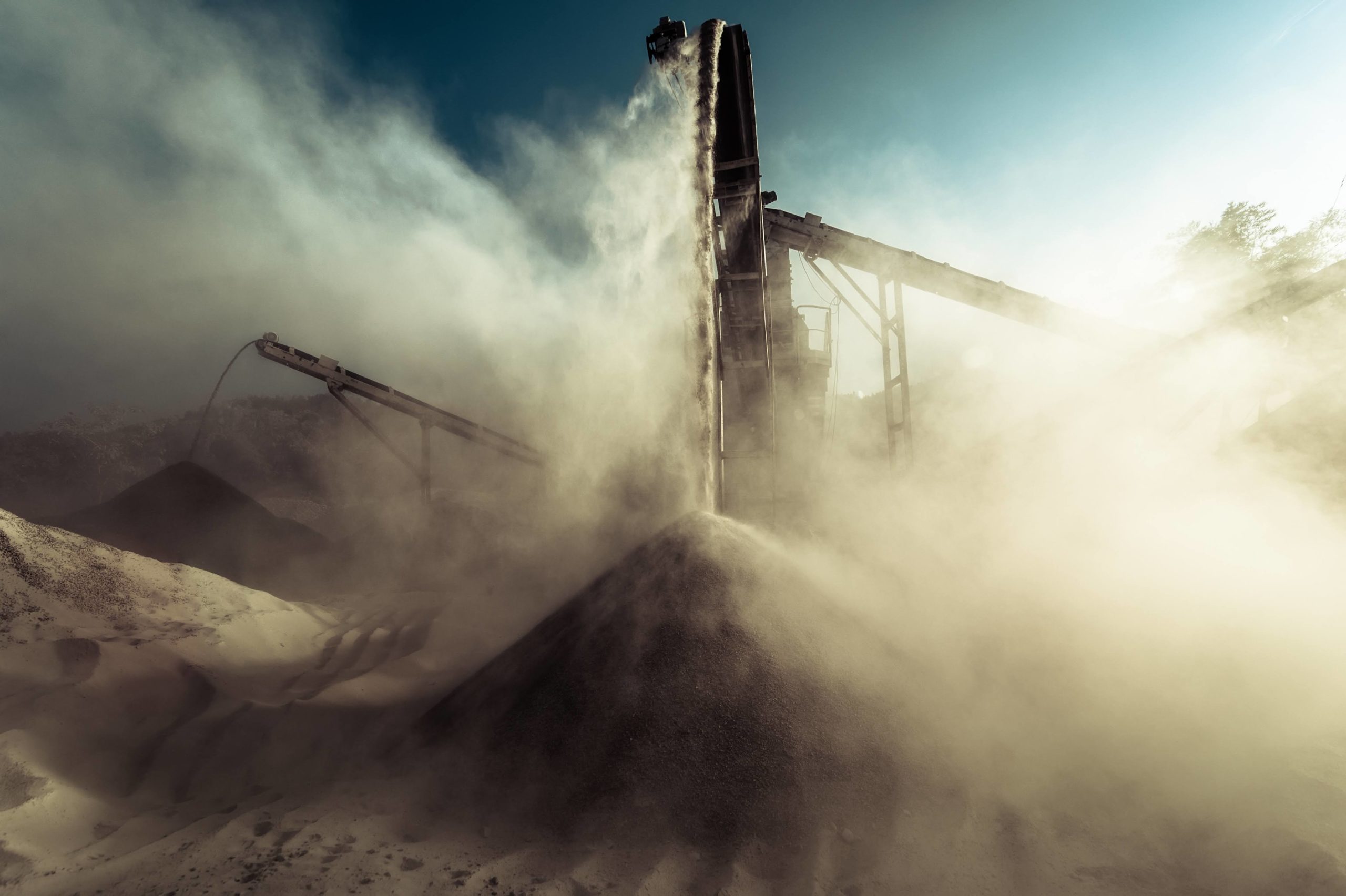
Dust Explosion Mitigation & Prevention Guide
Did you know? Materials considered to be a combustible dust can be found in a variety of industries and can arise from handling everyday materials such as sugar, plastics, and sawdust.
What is a Dust Explosion?
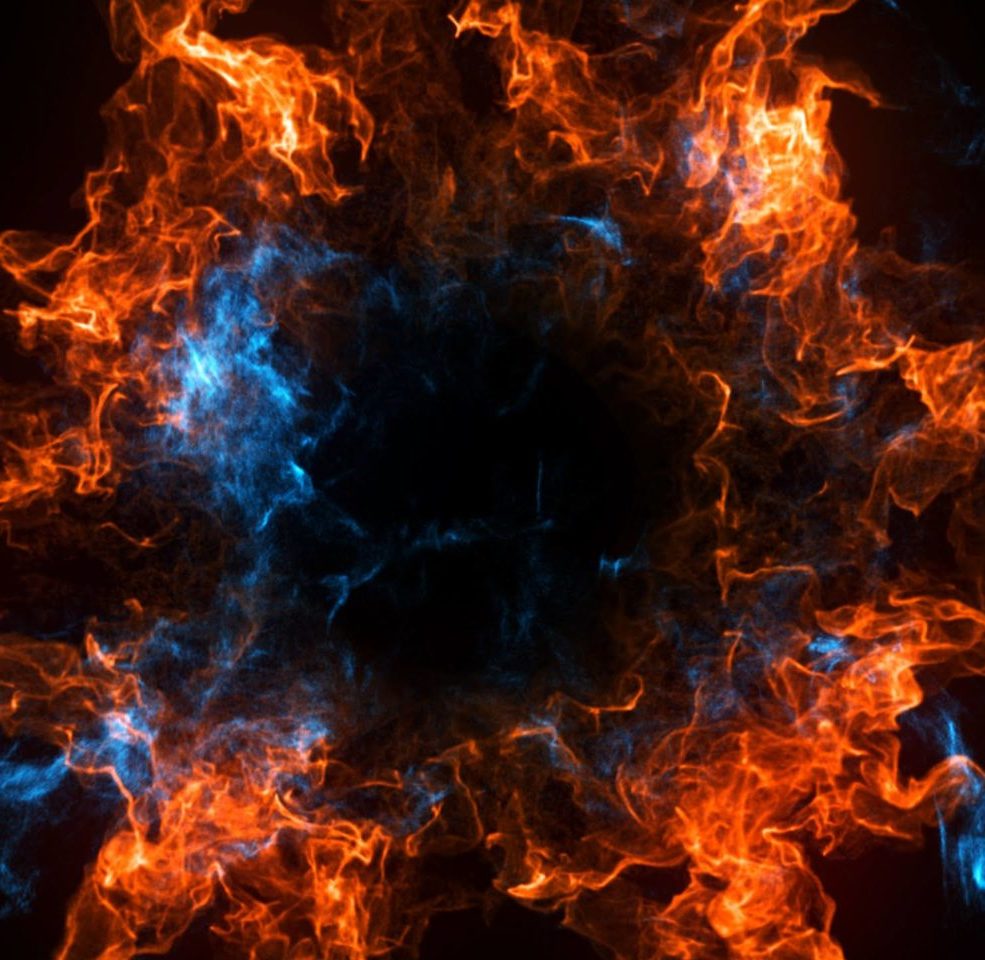
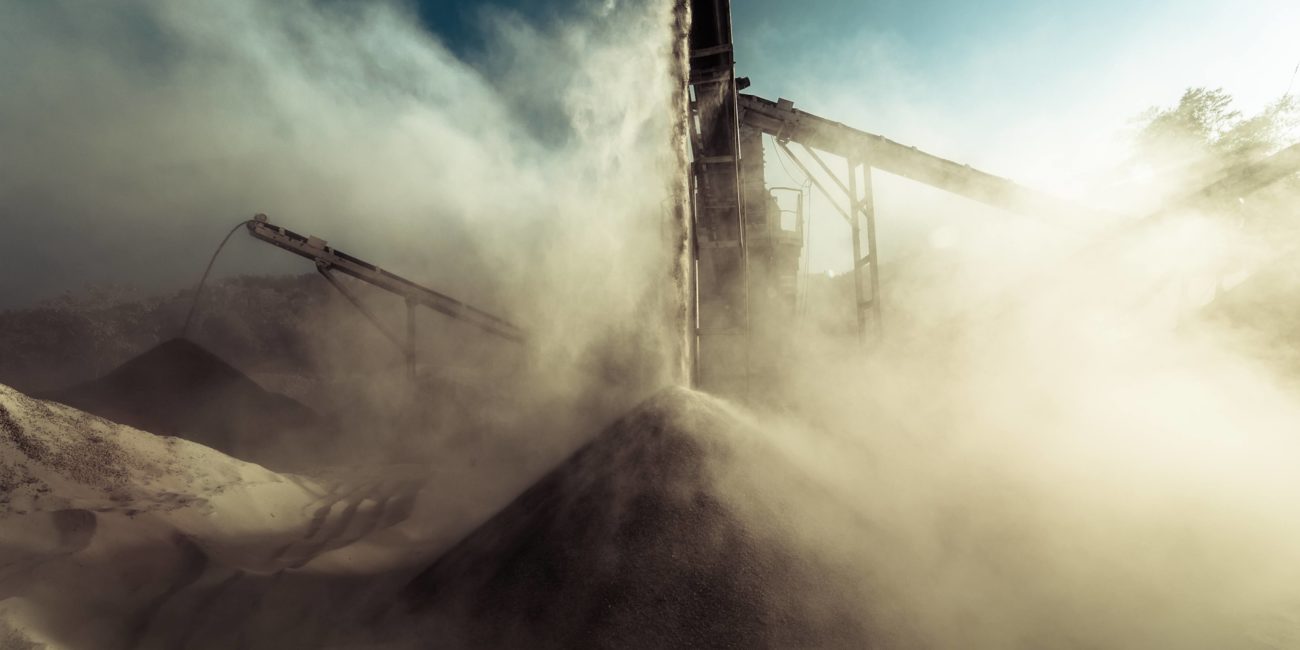
The 5 Elements of a Dust Explosion
1. Oxygen – Air is the most common oxidizing medium. O2 must be present in sufficient concentration to support the combustion.
2. Ignition – Ignition source is often the only leg of the pentagon not readily present. Possible ignition sources include open flame, hot surfaces, static or electrical discharges, and heat from friction or mechanical impact.
3. Dispersion – A suspended cloud of explosive dust with sufficient concentration will allow combustion to occur more rapidly than in a layer.
4. Confinement – A suspended dust cloud must be enclosed in order to build pressure that is characteristic of a dust explosion. Without confinement, the rapid combustion is a Flash Fire.
5. Fuel – Combustible Dusts serve as fuel for combustion. Examples include grain dust, plastics, cornstarch, coal, wood dust, and metals.
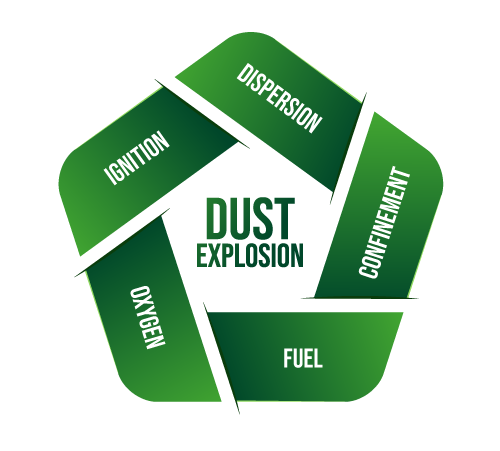
So how can we mitigate against a dust explosion from occuring?
Dust Explosion Mitigation Techniques
NFPA 652, Standard on the Fundamentals of Combustible Dust (2019), requires that facilities and processes are designed to mitigate the dangerous consequences of fires and explosions that are a hazard of handling combustible dust. To meet this requirement, facilities can elect to utilize either a prescriptive approach or a Performance-Based approach.
Performance-Based Approach
Using a Performance-Based approach involves the design of a system or facility that is assessed and evaluated against specific design criteria to demonstrate safety against each identified Fire and Explosion Scenario relevant to the system. The system must be able to adequately address the areas
of Life Safety, Structural Integrity, Mission Continuity, Mitigation of Fire Spread and Explosions, and the Effects of Explosions. When utilizing a Performance-Based design, the proposed system or facility must be tested using appropriate methods and calculations acceptable to the Authority Having Jurisdiction (AHJ).
Prescriptive Approach
Using a Prescriptive approach involves designing and installing Explosion Mitigation or Prevention Systems
as laid out in Chapters 9 of NFPA 652. This means that each vessel that is deemed to have an explosion hazard shall be protected using one of the following acceptable protection methods:
Protection Methods
The following five methods can be used to help aid in protecting against a dust explosion.
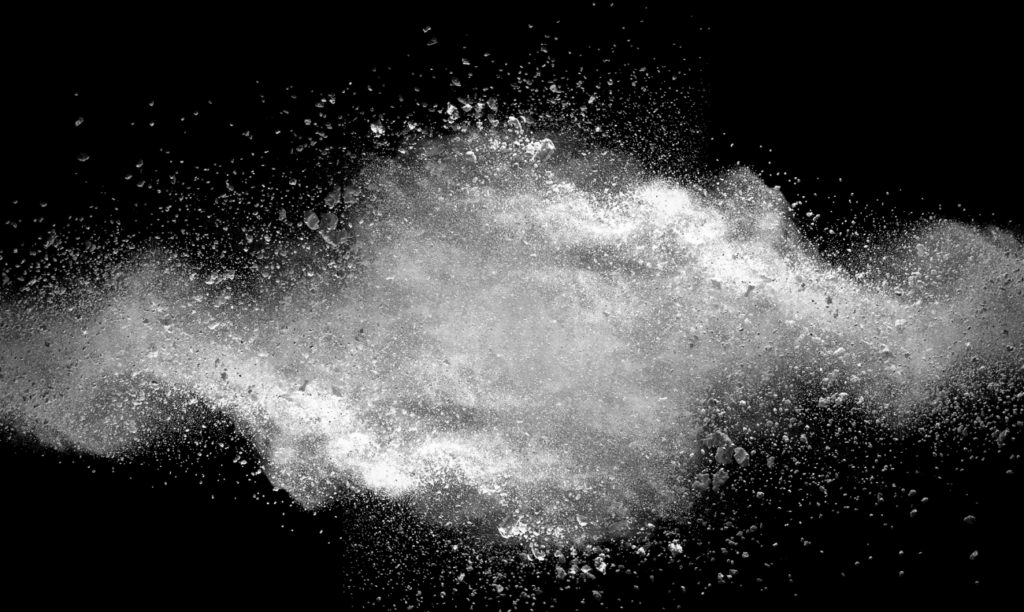
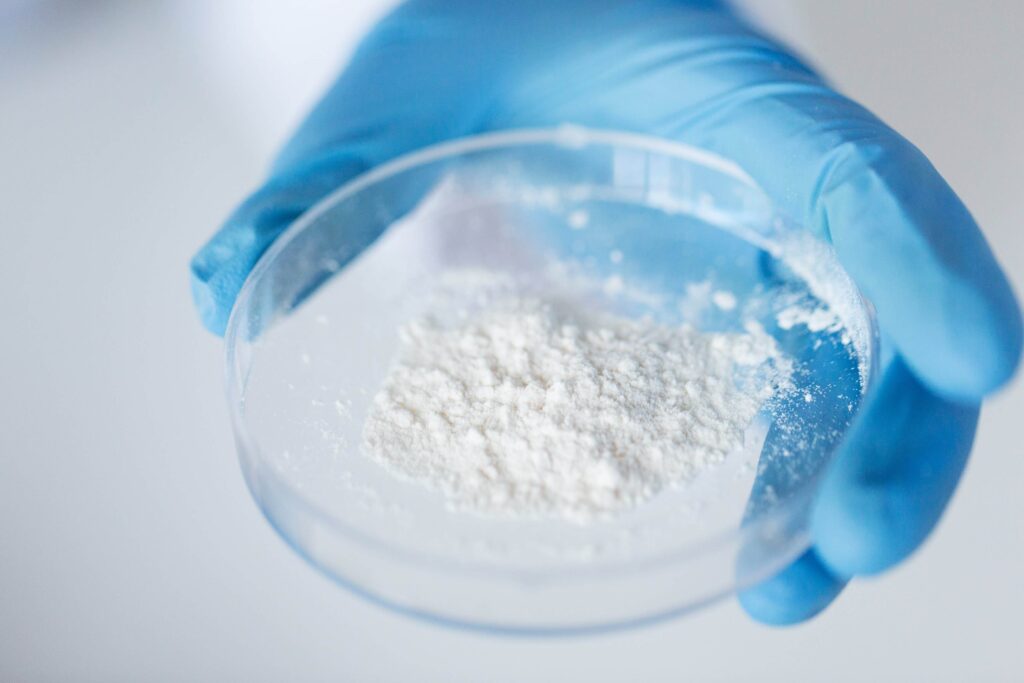
Inerting
Sometimes called Blanketing or Padding, Oxidant Concentration Reduction in accordance with NFPA 69 involves introducing inert gas (such as Nitrogen, Argon, or CO2) into the system in order to reduce the oxidant concentration to a point at which combustion cannot occur.
This method requires that the Limiting Oxygen Concentration (LOC, EN140344:2004) be
known for the combustible dust and instrumentation shall be installed to ensure the desired oxidant concentration reduction within the protected system. It is also acceptable to utilize so-called spot checks to monitor oxidant concentrations non-continuously. Other hazards related to inerting should be considered as part of the design such as asphyxiation which is a real danger to personnel if not properly trained. Inerting is a method of PREVENTION.
Explosion Venting
Deflagration Venting in accordance with NFPA 68 is a method of preventing the overpressure of a protected vessel or building through the use of a rupture panel or similar device which is designed to release at a low pressure (typically 1.5 psig) and expel the flame ball out of the protected volume.
Explosion venting must be applied to outdoor vessels directed to a safe location or indoor vessels may be vented with a vent duct directed to the outdoors. The required vent area of the explosion vents are described by calculations found in NFPA 68. The Pmax & Kst values for the combustible dust are required in order to properly design a venting solution and these values can be determined with the Explosion Severity Test (ASTM 1226). The strength of the vessel or building must also be known and is communicated in the form of Reduced Pressure (Pred). Explosion Venting is a PASSIVE mitigation strategy.
Flameless Venting
Deflagration venting through a listed flame-arresting device in accordance with NFPA 68 is a method similar to standard explosion venting.
Rather than releasing a flame ball into the area surrounding the
explosion vent opening, the flameless vent will quench the flame and expel only the combustion gases which makes it safe for use indoors. There are several different types of flameless vents on the market, but all rely on the same basic function of using stainless steel mesh as a flame arrestor. Like explosion venting, the design of the flameless vent should be determined in accordance with the calculations found in NFPA 68 and an efficiency factor should be applied. Pmax, Kst and Pred values will all be needed in order to complete the design of this solution. Explosion Isolation is required to be used in conjunction with this solution in accordance with NFPA 69. Flameless Venting is a PASSIVE mitigation strategy.
Containment
Deflagration pressure containment in accordance with NFPA 69is a method in which the vessel handling a combustible dust is built to withstand the pressure of a deflagration within the vessel.
In most cases, this means building the vessel to withstand between 8 and 12 barg (115 to 175 psig) and the pressure that will need to be accounted for is found in the Pmax value obtained by the Explosion Severity Test (ASTM 1226). Typically, this method is employed by manufacturers of milling equipment (e.g. hammermills) and smaller process equipment utilized primarily in the pharmaceutical industry. It is important to ensure that a containment strategy utilizes fastacting mechanical isolation in accordance with NFPA 69 that is appropriate for containment pressures to prevent the pressure and flame from exiting via the inlet and outlet of the protected vessel. Containment can be PASSIVE or ACTIVE, depending on the type of isolation.
Explosion Suppression
Deflagration suppression in accordance with NFPA 69 is a method for detecting and extinguishing the deflagration in its early stages, before the pressure has a chance to build.
This is typically achieved by using pressure detectors and chemical suppression bottles mounted directly to the protected vessel. These chemical suppressant
bottles will usually contain a powder suppressant such as sodium bicarbonate and high pressure gas (e.g. nitrogen) to propel the suppressant into the protected volume. These suppression systems offer
the advantage of not releasing any gas into the area surrounding the protected vessel, but can be prone to false activation if not designed, installed, and maintained properly. When designing a chemical suppression solution, the Kst and Pmax of the material must be known (ASTM 1226), the Pred of the vessel must be determined, and the process conditions must be considered to ensure that the detectors will not false activate the system
due to normal operating conditions. Explosion Isolation is required to be used in conjunction with this solution in accordance with NFPA 69. Explosion Suppression is an ACTIVE mitigation strategy.
Explosion Isolation
In most cases, the Prescriptive approach for vessels with Combustible Dust Explosion Hazard does not stop with the Mitigation Strategies listed above. To mitigate the risk of Secondary Explosion and the effects of pressure piling as a deflagration moves down a constricted pathway (e.g. duct), NFPA 652 requires that explosion isolation devices be installed in accordance with NFPA 69 to contain the effects of pressure and flame. These isolation devices are commonly used on inlets, clean air outlets, product outlets, aspiration ducts, and any other duct or chute to/from a vessel. There are several different methods for isolation that are acceptable under NFPA 69. Below are commonly utilized isolation methods:
Isolation Flap Valve
The Flap Valve is a mechanically operated device similar to a check-valve design that is actuated based on the pressure front from a deflagration that precedes the flame front. These flap valves are becoming increasingly common for explosion isolation of inlet ducts to dust collector and cyclones. However, the flap that protrudes into the air flow can easily be abraded away or obstructed by large amounts of solids in the flow. These should be chosen carefully for the application considering the process design and any limitations outlined in the valve’s Approval. Ensure to utilize a valve with a valid ATEX EN16447 Approval Listing which was created for flap valves asthere have been losses from valves that were not tested and approved to this new Approval Standard. The Flap Valve is a PASSIVE form of Explosion Isolation.
Chemical Isolation System
A chemical suppression bottle containing a solid extinguishing agent (typically sodium bicarbonate) is connected to the duct and triggered using either Pressure Detection or Optical Detection. The suppressant is deployed into the isolated duct in order to extinguish the flame front. This type of isolation system offers the most flexibility for installation and can be used both on small pipes (3”) and large (90”) diameter ducts. False activation concerns and ongoing maintenance requirements should be considered. Explosion Isolation is an ACTIVE form of Explosion Isolation.
Isolation Pinch Valves
The Pinch Valve consists of a rubber bladder which is actuated by compressed air stored in a reservoir tank above. The pinch valve may triggered based on the opening of a rupture panel or by detectors sensing the pressure or light from a deflagration. These valves are ideal for use in pneumatic convey operations and are limited to small duct sizes up to about 12”. Care should be taken to design the valve to minimize wear to the bladder. an be PASSIVE or ACTIVE, depending on how the valve is triggered.
Fast Acting Mechanical Valve
Typically a slide gate, this fast acting valve is triggered based on pressure or optical detection at the vessel. These valves can be built for containment and prevent both the pressure and flame ball from traveling past the valve. Some valves will utilize an ignitor to actuate the valve gate while newer designs utilize compressed air to actuate the valve. Using compressed air allows the valve to be repeatedly opened and closed without need for rebuild. Fast Acting Slide Gate Valves are an ACTIVE form of Explosion Isolation.
Isolation Float Valve
The Float Valve is a mechanical device which operates on many of the same principles as the Flap Valve, but which protects from explosion traveling in the same direction as normal air flow. Due to the design of the float valve with a large poppet in the center of the valve, this should only be used with air flows with very low solids concentrations. Again, ensure that the valve is designed and approved for explosion isolation with a valid ATEX Approval Listing. The Float Valve is a PASSIVE form of Explosion Isolation.
Rotary Airlock
Rotary Airlocks are a common device found at the bottom of hoppers to provide explosion isolation between the vessel above and the drop chute below. However, in order to provide effective explosion isolation, rotary airlocks must conform to the criteria outlined in NFPA 69 regarding material chokes. The criteria include strength of the valve to withstand Pred, the minimum required number of vanes, and the required clearance of the tips. Rotary Airlocks are a PASSIVE form of Explosion Isolation.
Explosion Prevention
While Explosion Mitigation methods aim to minimize the negative effects of a deflagration with the assumption that ignition will occur, Explosion Prevention methods aim to keep the deflagration from occurring in the first place.
Explosion Prevention is achieved by removing one or more of the legs of the Dust Explosion Pentagon. Two methods of explosion prevention, Inerting and Dilution, are described above. The following are some of the Prevention methods
commonly employed:
• Spark Detection & Extinguishing
• Housekeeping
• Bonding and Grounding
• Magnetic Separation
• Preventative Maintenance
• Electrical Classification
• Hot Work Permitting
• Administrative Controls
Summary
As you can see from the details in this guide, it’s important to ensure that risk mitigation and prevention are considered for the occurance of dust explosions. Although relevant mitigation techniques were mentioned, these are not always guaranteed to prevent an explosion from occurring. Prevention is only possible with the removal of one or more of the elements of the Dust Explosion Pentagon.
For more information about the prevention or mitigation of a dust explosion contact the friendly team at Dustcon Solution.
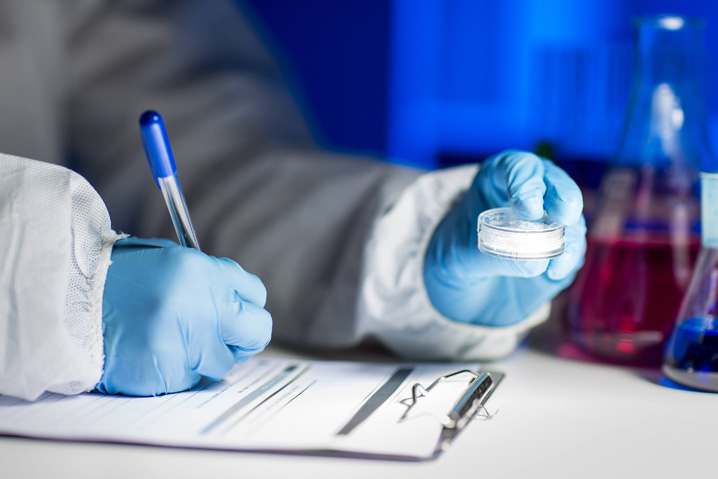
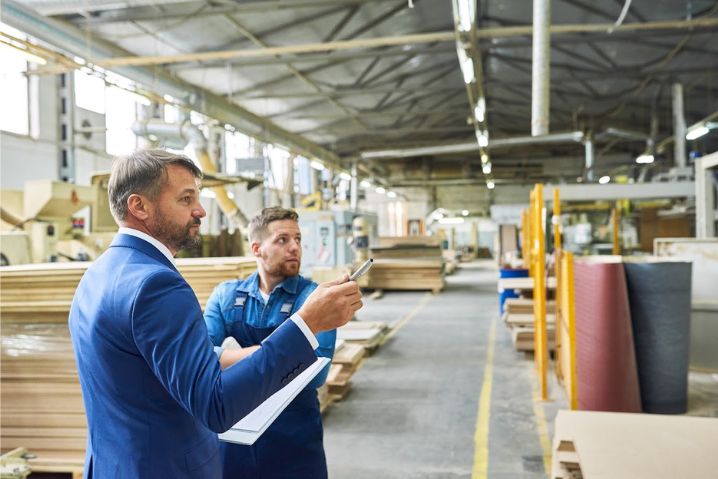
Addressing NFPA 652 Standard Regarding Combustible Dusts
Do you operate a facility that requires you to engage with substances that are dusty or powdery in n
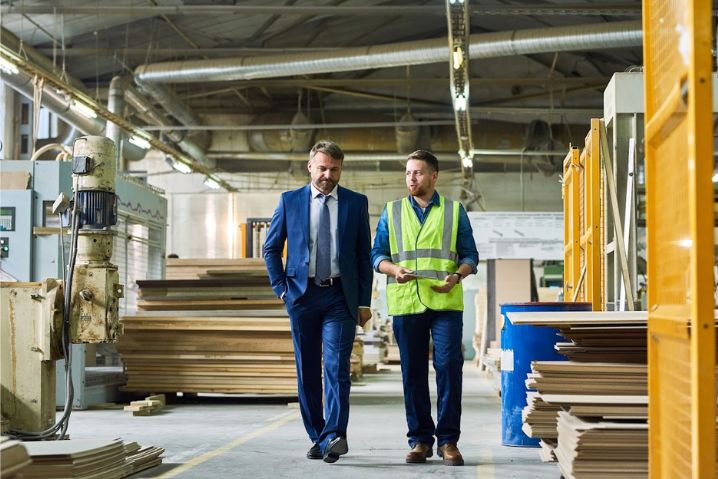
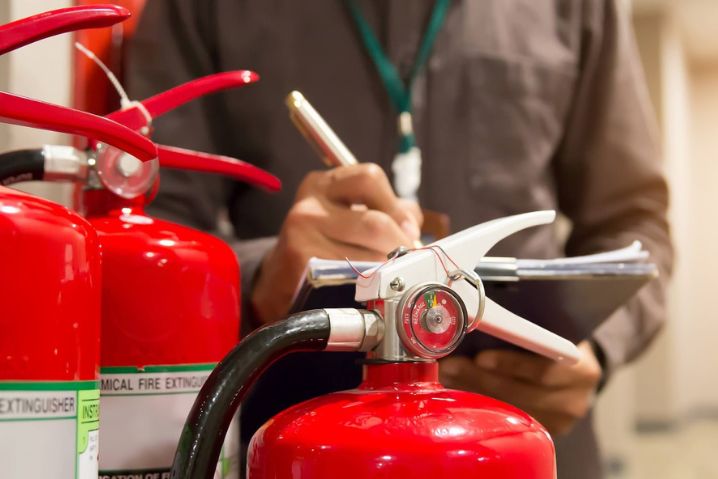
6 Industries Added by OSHA to the Combustible Dust NEP Program
n late January 2023, a new version of the Combustible Dust National Emphasis was issued by the Occup
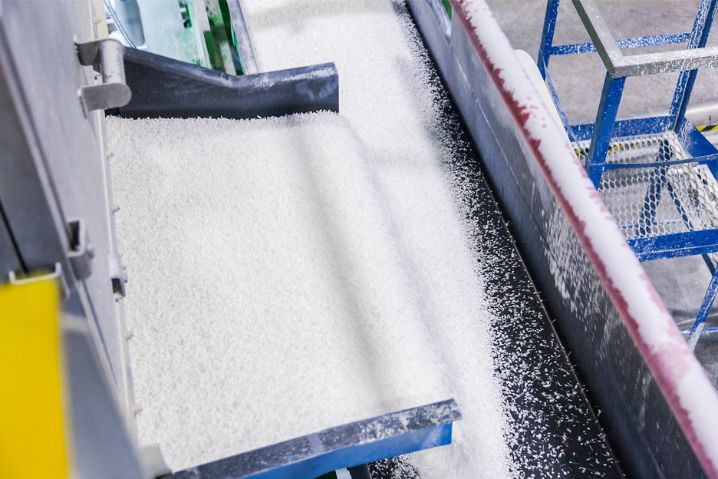
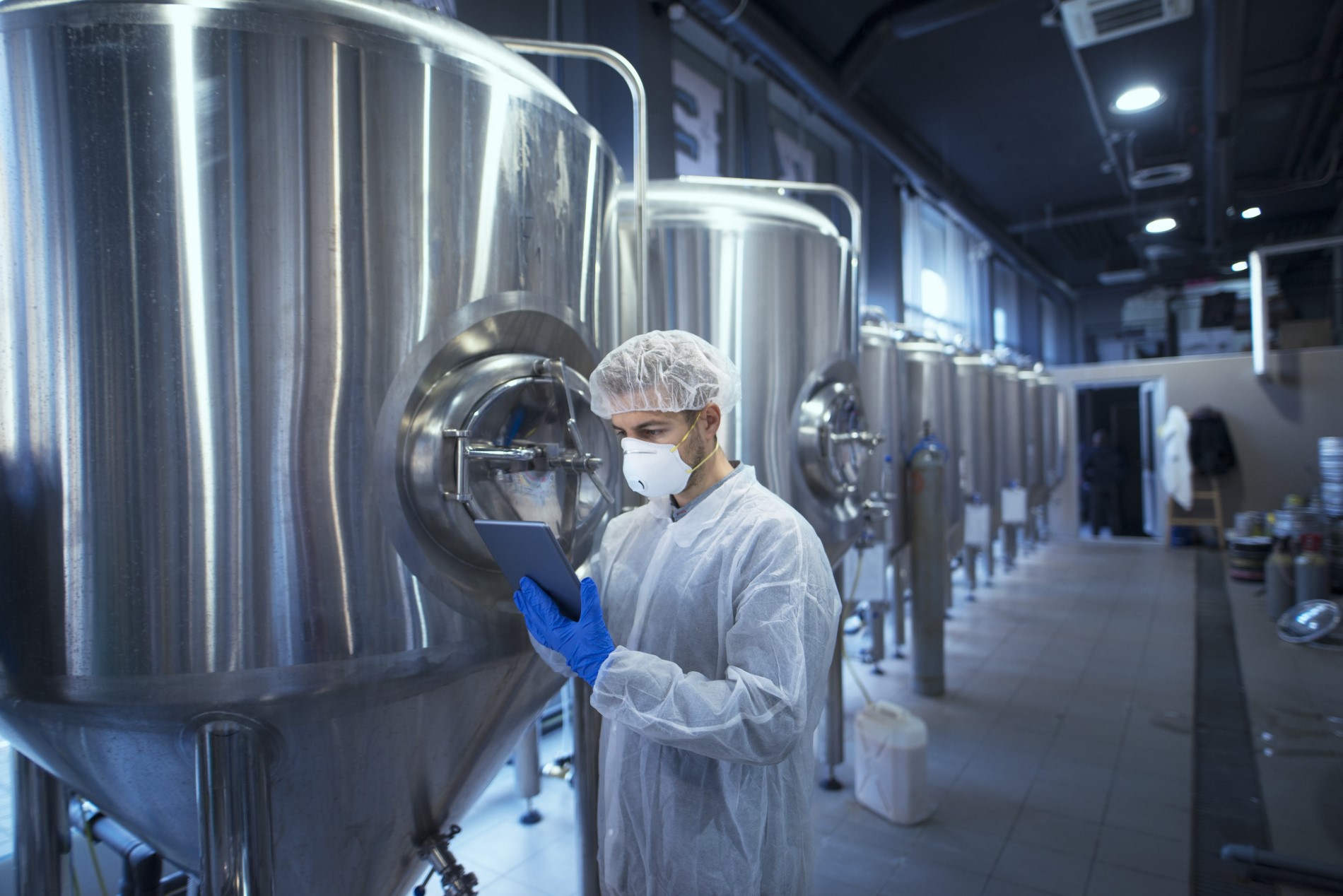
Ensuring the Safety of Facility Through Dust Explosion Test Data
“Could it be a problem if my powder has demonstrated 3mJ of minimum ignition energy and 256 bar.m/