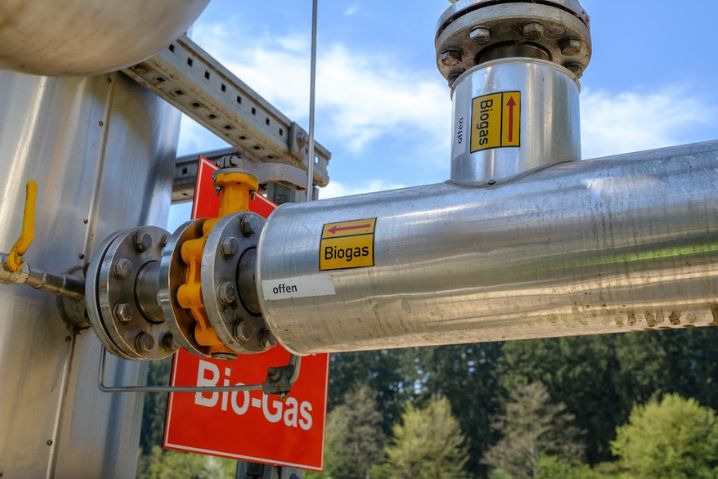
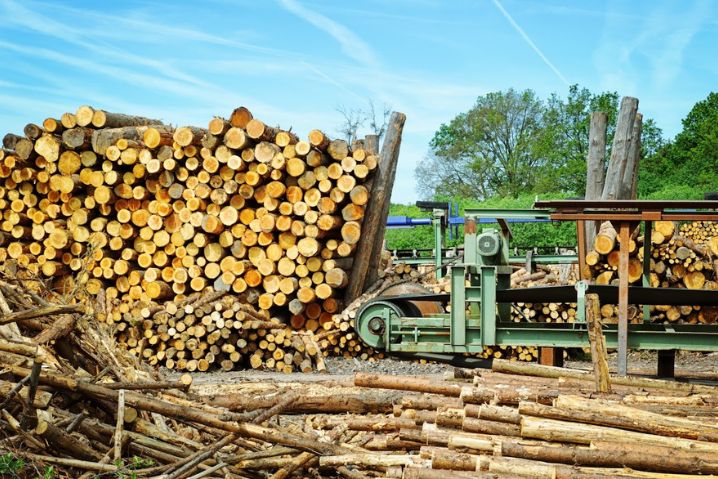
Biomass materials with self-heating properties: hazards
Since the field of biomass energy has undergone expansion, the importance of a larger storage capacity for biomass has skyrocketed, in order to facilitate a consistent fuel supply. With the increase in storage needs, the risks pertaining to such storage also rise – both in terms of health and safety. Specifically, hazards such as off-gassing-initiated suffocations, dust explosions, and sometimes spontaneous occurrences of fires are of utmost concern. This has also led to an increase in reported incidents being reported from biomass facilities. According to data available online, the number of incidents reported between the years 2000 and 2018 was 65. However, the numbers seem to be rising, with nine cases reported only in 2017. Fire was involved in 55% of the cases that were reported, out of which self-heating caused 27.5% of the incidents. While self-heating may have contributed to other incidents, there is no evidence regarding them. The issue of biomass overheating should not be neglected. Thailand witnessed a massive fire in 2017, at the facility of Advanced Agro-Power Plant, when accumulated heat caused a pile of biomass fuels weighing 500 tonnes to catch fire.
Fundamentals
We are all aware at this point that in industries, a large part of bulk materials and powders are combustible. When conditions are problematic, they could lead to explosions, fires, or flash fires. Three components must be present simultaneously within the same location to create a fire hazard – first, a particulate solid that is combustible in nature, an atmosphere that has oxygen, and a source of ignition. Typically, these three components are called the fire triangle. Flash fire or deflagration risks can be propagated by dust clouds when three conditions are present simultaneously: an adequate amount of dust that is combustible to cause deflagration; an atmosphere rich in oxygen; a reliable mechanism for suspension; and a source of ignition.
When dust or any powder material is being handled, conveyed, processed, collected, or packed, the primary three factors are typically present. Dust cloud deflagration occurs when a source of ignition is present simultaneously. In the case of deflagration within a process vessel that is closed or confined, including elevators, conveyors, and buildings, it could lead to the buildup of pressure that can rupture the enclosure and lead to a dust explosion.
According to the existing regulations, facilities with hazards of combustible powders or dust fires, deflagration, as well as explosions, must adhere to the NFPA 652 Standard on the Fundamentals of Combustible Dust, which was issued in 2019. According to the standard, a facility’s owner or operator should meet the life safety, and continuity of the mission, as well as the reduction of the propagation of fire and explosions by undertaking the following steps:
- Provide proper protection against the implications of the fire to occupants who are outside the immediate area of the emergency, so they have adequate time to leave, relocate, or seek shelter.
- To the extent it is possible, ensure that people do not sustain severe injuries due to explosions or flash fires.
- Implement protective measures to ensure that the implications of explosions, fires, and flash fires are mitigated for properties and people in the vicinity.
- Minimize damage levels to the degree that the owners or operators consider ideal to facilitate the facility’s current missions, production, and operations.
- Decrease the risk of fires as well as explosions that may damage nearby buildings, enclosures, storage, or structural elements of the facility.
The following tasks must be completed, as per NFPA 652, to adhere to the aforementioned requirements:
- For the materials used in the facility, determine and analyze the hazards of combustibility as well as explosibility.
- Systematically assess the possible hazards (dust fire, explosions, and deflagrations) via a dust hazard analysis (DHA) and devise solutions to mitigate them.
- Take measures to prevent fires, flash fires, and explosions.
- Develop safety management systems in writing.
In any facility, DHA helps methodically assess potential hazards of dust fire, explosion, and deflagration, while also providing measures to manage them. Through this process, the areas accumulating combustible powders as well as explosible atmospheres with dust clouds are identified. It also helps identify plausible sources of ignition under both regular operating conditions and exceptional cases.
While new constructions must perform DHAs immediately, existing ones should have completed them by September 7, 2020. It is also mandatory to review and revise DHAs once in five years. An expert who has experience dealing with combustible particulate hazards must conduct DHAs.
Many sources of ignition exist, based on the kind of powder as well as the process. Some of the potential sources are open flames, heating or even sparks generated by friction, flames from welding and cutting, as well as electric equipment sparks and discharges of electrostatic nature.
In the case of biomass material, NFPA standards that are commodity- or industry-specific must be consulted, based on their nature. This article looks at the criteria listed in NFPA 652.
Hazards With Self-heating Properties
For bulk material, its inherent instability coupled with the heating processes and their nuanced sources of ignition may prove to be problematic. For instance, in the case of bulk powders and layers, they are capable of self-heating, catching fire, or smoldering because of various biological and exothermic chemical processes, since they tend to generate heat. In the past, there have been instances of spontaneous fires in hay fields, heaps of compost barns, and wood chips. Here, water facilitates biological processes, which can be heat-generating.
Self-heating can gradually touch the critical temperature wherein the smoldering of bulk material occurs. If the temperature continues to rise, it could accelerate. Bulk materials are usually effective thermal insulators, as they hinder cooling while facilitating heat buildup and generation internally.
The phenomenon of self-heating is particularly complex since there are two processes involved: a chemical reaction that generates heat as well as a process involving loss of heat. If the heat generation rate is greater than that of heat transfer, it could increase the temperature at a rapid rate. When interventions are not employed, the self-heating material could smolder. But combustion only occurs when there is air. Consequently, superheating of the bulk material occurs without catching fire. Operators may, however, experience asphyxiation due to gas emissions that are generated.
The introduction of air could cause bulk materials to catch fire and if dust rises at the same time, a dust explosion could occur.
Time is a pertinent factor when it comes to spontaneous heating because a certain amount of time is required for exothermic reactions to occur. Often, a filled bunker or hopper causes a fire.
Processes involving the drying and heating of powders are more vulnerable to fires because of self-heating. However, it is also possible for materials to get heated through mechanical milling or grinding, or the buildup of a fugitive layer of powder over a hot area. The problem becomes particularly apparent when processed material buildup occurs as a bulk or even a layer across the process equipment, in addition to big and small packages, silos, and hoppers. Self-heating commonly occurs when biomass is stored in bulk and the size of the bulk is directly associated with fire hazards.
Bulkier materials do not naturally have a specific temperature at which they begin self-heating, since the temperature relies on various parameters including composition, impurities present within the material, dimensions, accumulated powder’s size, availability of air/oxygen, as well as the period of time over which the powder is exposed to a particular temperature.
Storage, Transportation, and Processing of Powder
Comprehending a material’s self-heating properties is of utmost importance to incorporate safety measures that protect against fires as well as explosions erupting from self-heating.
A sampler must be heated in a controlled environment in order to determine at what point its temperature begins to rise, regardless of the source of heat. This helps measure exothermic activity. It is essential that the test sample represents the process powder in order to provide useful information about the hazards. The conditions of packing and processing along with handling the materials must also be simulated accurately in the laboratories. Screening tests are first conducted when the temperature of the test sample is raised by 1 degree Celsius every minute. A self-heating temperature that is proximal to the storage or process temperature indicates a need for an isothermal self-heating test. This also holds true if, at a temperature higher than the process temperature, the length of the process cycle exceeds the test period.
- Grewer Oven: A stream of hot air is permeated into the sample to heat the material. The sample’s onset temperature of self-heating is determined to be the temperature surrounding the sample at which it starts increasing at a faster rate than when compared to the inert reference sample in this test.
- Isothermal basket test: Powder samples are heated in an oven uniquely sized cubical wire baskets (usually three). The objective is to identify the minimum self-heating temperature of the sample. Through this test, it is possible to evaluate the scale’s effect on the onset temperature of the material in a precise manner.
- Bulk powder test: Helps assess materials’ ability to self-heat, wherein the quantities are not more than 1 ton, during bulk heating.
- Aerated powder test: A hot air stream is propagated through the bulking powder and the conditions present during heating processes are simulated, wherein the quantity of the material does not cross 1 ton.
- Powder layer test: A simulation of hot air flowing within a dryer on top of a material deposit or layer. Materials can be deposited internally in all dryers, for example, in tray dryers.
Using the above tests for bulk biomass storage will produce useful screening outcomes, but using basket tests could help mimic the effect of a hopper or bunker storage volume. It is generally true that if the storage volume is higher, the temperature at which self-heating starts creating issues will be lower.
Preventing Hazards
- The temperature of the material must be lowered to a safe margin, which is significantly less than the temperature at which self-heating onsets, as determined by laboratory tests.
- Decrease the period of storage.
- Levers, dead zones, corners, etc., should be avoided in equipment or facility design to prevent inadvertent accumulation of material.
- Ensure that process equipment’s internal surfaces do not accumulate hazardous levels of material deposits.
- In addition to fire as well as explosion protection, a DHA must review approaches to prevent other sources of ignition.
Conclusion
Both chemical and biological processes can cause powders and bulk materials to self-heat and smolder.
In order to prevent self-heating, fires, as well as explosions caused when handling or processing bulk materials, we must understand their inherent thermal instability. This goal can be achieved by tailoring laboratory tests that will reasonably mimic actual storage and processing conditions.
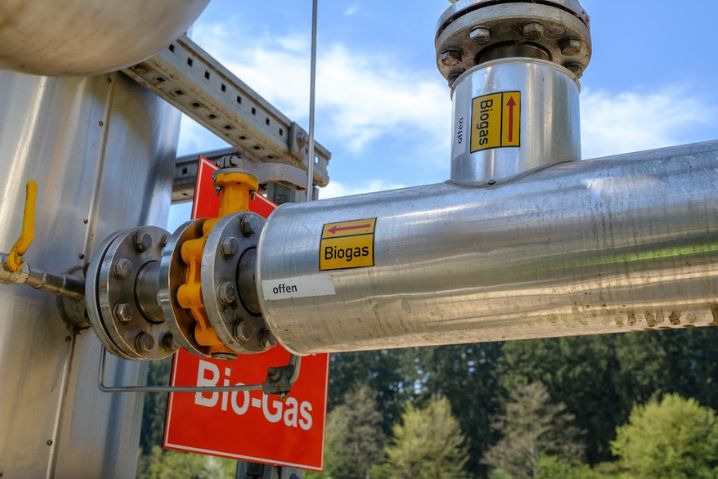
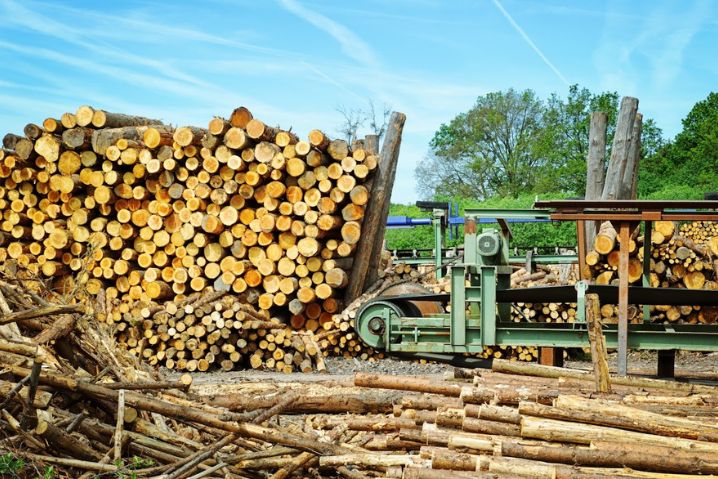
Biomass materials with self-heating properties: hazards
Since the field of biomass energy has undergone expansion, the importance of a larger storage capaci